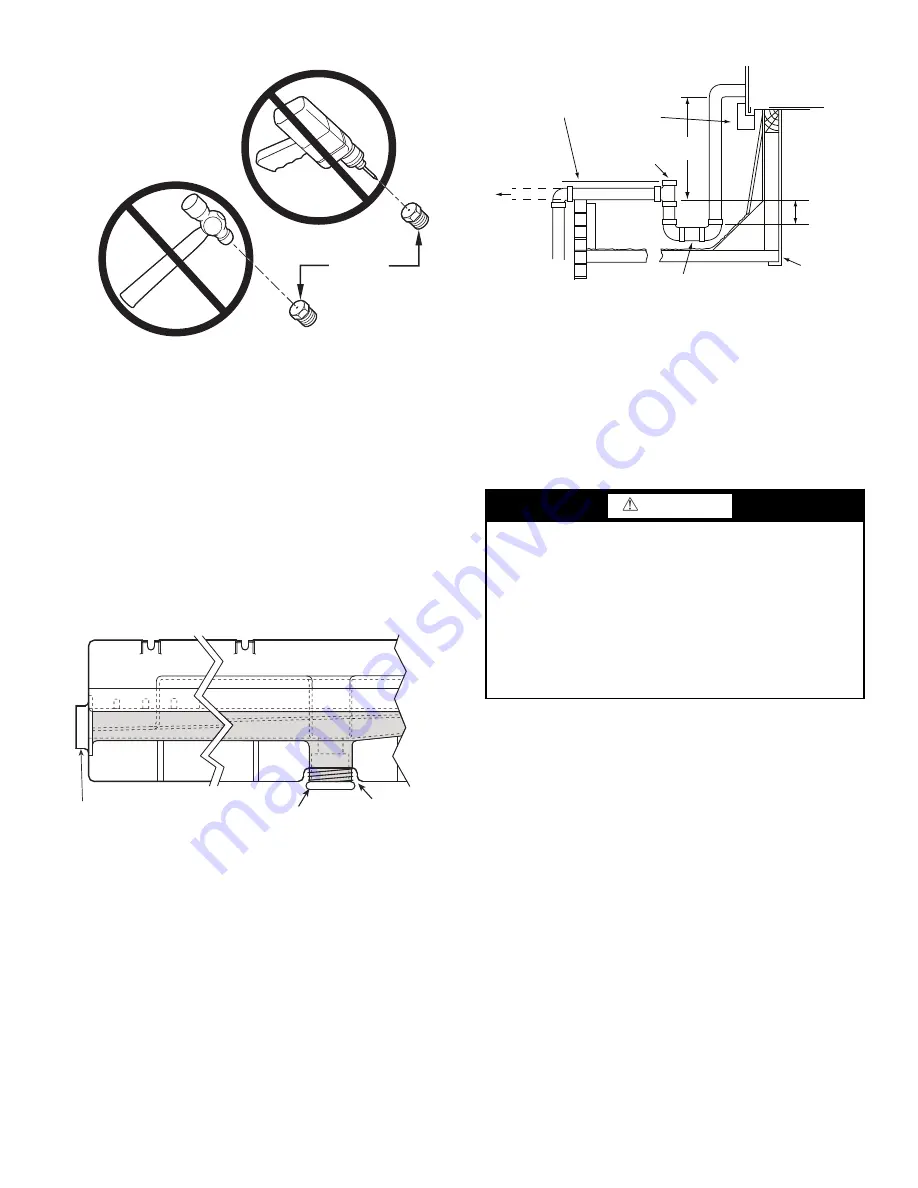
15
Fig. 23 — Orifice Hole
Step 12 — Install External Condensate Trap and Line
The unit has one
3
/
4
-in. condensate drain connection on the end of
the condensate pan and an alternate connection on the bottom. See
Fig. 24. Unit airflow configuration does not determine which
drain connection to use. Either drain connection can be used with
vertical or horizontal applications.
When using the standard side drain connection, ensure the red
plug in the alternate bottom connection is tight. Do this before set-
ting the unit in place. The red drain pan can be tightened with a
1
/
2
-
in. square socket drive extension.
To use the alternate bottom drain connection, remove the red drain
plug from the bottom connection (use a
1
/
2
-in. square socket drive
extension) and install it in the side drain connection.
The piping for the condensate drain and external trap can be com-
pleted after the unit is in place. See Fig. 25.
Fig. 24 — Condensate Drain Pan (Side View)
Fig. 25 — Condensate Drain Pan Piping Details
All units must have an external trap for condensate drainage. In-
stall a trap at least 4 in. (102 mm) deep and protect against
freeze-up. If drain line is installed downstream from the external
trap, pitch the line away from the unit at 1 in. per 10 ft (25 mm
per 3 m) of run. Do not use a pipe size smaller than the unit con-
nection (
3
/
4
in.).
Step 13 — Make Electrical Connections
NOTE: Field-supplied wiring shall conform with the limitations
of minimum 63°F (33°C) rise.
FIELD POWER SUPPLY
If equipped with optional Powered Convenience Outlet, the power
source leads to the convenience outlet’s transformer primary are
not factory connected. Installer must connect these leads accord-
ing to required operation of the convenience outlet. If an always-
energized convenience outlet operation is desired, connect the
source leads to the line side of the unit-mounted disconnect.
(Check with local codes to ensure this method is acceptable in
your area.) If a de-energize via unit disconnect switch operation of
the convenience outlet is desired, connect the source leads to the
load side of the unit disconnect. On a unit without a unit-mounted
disconnect, connect the source leads to compressor contactor C
and indoor fan contactor IFC pressure lugs with unit field power
leads. See CONVENIENCE OUTLETS on page 17 for power
transformer connections.
The field power wires are connected to the unit at line-side pres-
sure lugs on compressor contactor C and indoor fan contactor IFC
(see wiring diagram label for control box component arrange-
ment) or at factory-installed option non-fused disconnect switch.
Maximum wire size is #2ga AWG (copper only) per pole on con-
tactors and #2ga AWG (copper only) per pole on optional discon-
nect. See Fig. 26 and unit label diagram for field power wiring
connections.
BURNER
ORIFICE
DRAIN
(FACTORY-INSTALLED)
PLUG
CONDENSATE PAN (SIDE VIEW)
STANDARD
SIDE DRAIN
ALTERNATE
BOTTOM DRAIN
WARNING
Failure to follow this warning could result in personal injury or
death.
Do not use gas piping as an electrical ground. Unit cabinet
must have an uninterrupted, unbroken electrical ground to
minimize the possibility of personal injury if an electrical fault
should occur. This ground may consist of electrical wire con-
nected to unit ground lug in control compartment, or conduit
approved for electrical ground when installed in accordance
with NEC (National Electrical Code); ANSI/NFPA 70, latest
edition (in Canada, Canadian Electrical Code CSA [Canadian
Standards Association] C22.1), and local electrical codes.
NOTE: Tr
a
p
s
ho
u
ld
b
e deep eno
u
gh to off
s
et m
a
xim
u
m
u
nit
s
t
a
tic
difference. A 4-in. (102 mm) tr
a
p i
s
recommended.
MINIMUM PITCH
1˝ (25 mm) PER
1
0´
(
3
m) OF LINE
BA
S
E RAIL
OPEN
VENT
TO ROOF
DRAIN
DRAIN PLUG
ROOF
CURB
S
EE NOTE
3
˝ (76 mm)
MIN
Summary of Contents for 582J 04-06
Page 4: ...4 Fig 2 Unit Dimensional Drawing ...
Page 5: ...5 Fig 2 Unit Dimensional Drawing cont ...
Page 21: ...21 Fig 38 Typical Perfect Humidity Adaptive Dehumidification System Humidistat Wiring ...
Page 23: ...23 Fig 40 Typical Control Wiring Diagram Electro Mechanical with W7212 ...
Page 25: ...25 Fig 43 Typical IGC Control Wiring Diagram ...