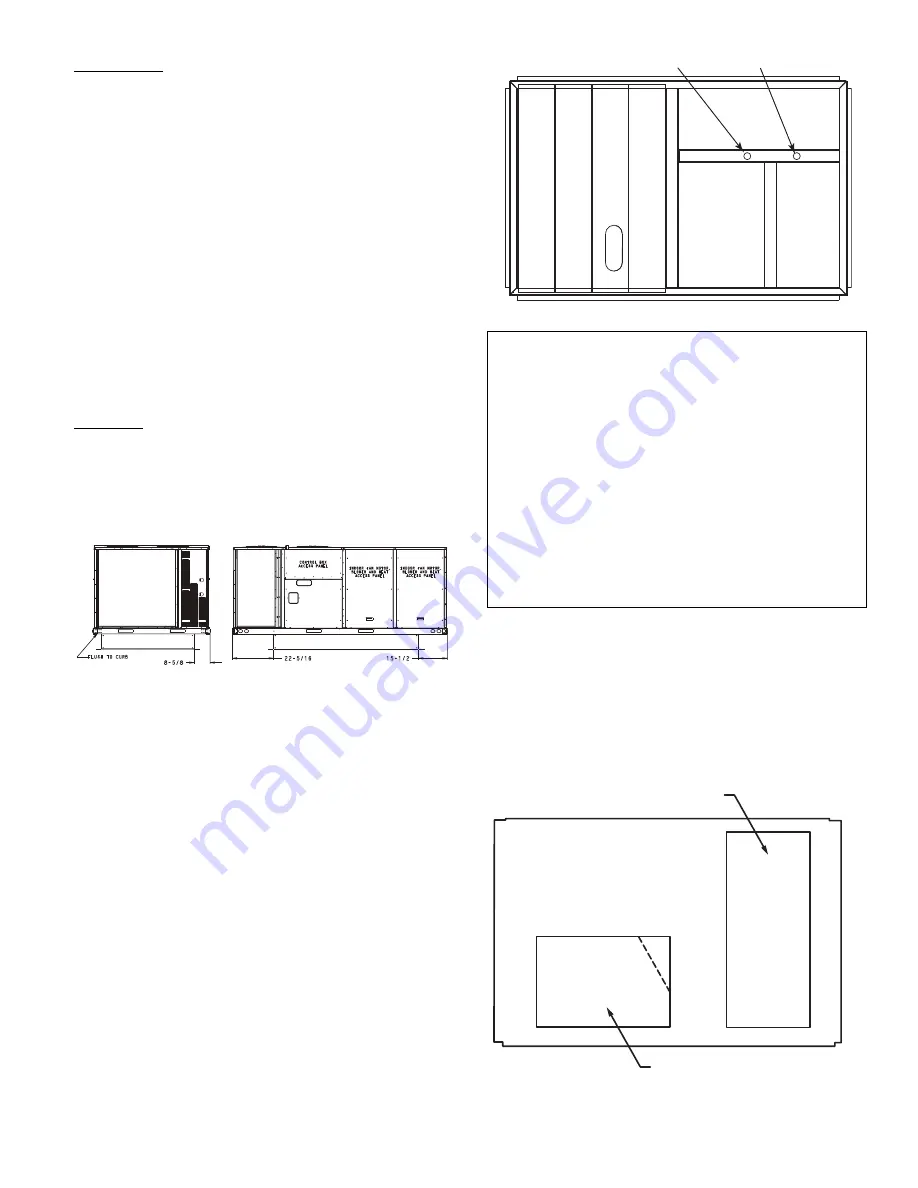
17
POSITIONING ON CURB
For Size 08-14 position unit on roof curb so that the following
clearances are maintained:
1
/
4
in. (6.4 mm) clearance between the
roof curb and the base rail inside the front and back, 0.0 in. clear-
ance between the roof curb and the base rail inside on the duct end
of the unit. This will result in the distance between the roof curb
and the base rail inside on the condenser end of the unit being ap-
proximately
1
/
4
in. (6.4 mm).
Although unit is weatherproof, guard against water from higher
level runoff and overhangs.
Flue vent discharge must have a minimum horizontal clearance
of 4 ft (1220 mm) from electric and gas meters, gas regulators, and
gas relief equipment. Minimum distance between unit and other
electrically live parts is 48 in. (1220 mm).
Flue gas can deteriorate building materials. Orient unit such
that flue gas will not affect building materials. Locate mechanical
draft system flue assembly at least 48 in. (1220 mm) from an adja-
cent building or combustible material.
NOTE: Installation of accessory flue discharge deflector kit
will reduce the minimum clearance to combustible material to
18 in. (460 mm).
After unit is in position, remove rigging skids and shipping
materials.
For Size 16, full perimeter curbs CRRFCURB074A00 and
075A00, the clearance between the roof curb and the front and
rear base rails should be
1
/
4
in. (6.4 mm). The clearance between
the curb and the end base rails should be
1
/
2
in. (13 mm). For
retrofit applications with curbs CRRFCURB003A01 and 4A01,
the unit should be position as shown in Fig. 11. Maintain the
15.5 in. (394 mm) and 8
5
/
8
in. (220 mm) clearances and allow the
22
5
/
16
in. (567 mm) dimension to float if necessary.
Fig. 11 — Retrofit Installation Dimensions
(Size 16 Shown)
If the alternative condensate drain location through the bottom
of the unit is used in conjunction with a retrofit curb, the hole in
the curb must be moved 12.5 in. (320 mm) towards the duct end of
the unit. See Fig. 12.
Although unit is weatherproof, guard against water from higher
level runoff and overhangs.
Remove all shipping materials and top skid. Remove extra cen-
ter post from the condenser end of the unit so that the condenser
end of the unit matches Fig. 39 and 40. Recycle or dispose of all
shipping materials.
Fig. 12 — Alternative Condensate Drain Hole Positions
Step 7 — Convert to Horizontal and Connect
Ductwork (When Required)
SIZES 08-14 CONVERSION —
Unit is shipped in the vertical
duct configuration. Unit without factory-installed economizer or
return air smoke detector option may be field-converted to hori-
zontal ducted configuration. To convert to horizontal configura-
tion, remove screws from side duct opening covers and remove
covers. Using the same screws, install covers on vertical duct
openings with the insulation-side down. Seals around duct open-
ings must be tight. See Fig. 13.
Fig. 13 — Horizontal Conversion Panels
IMPORTANT: If the unit has the factory-installed thru-
the-base option, make sure to complete installation of the
option before placing the unit on the roof curb.
See the following sections:
Factory-Option Thru-Base Connections
(Gas Connection) on page 22 for sizes 08-14 and page 22
for size 16
Factory-Option Thru-Base Connections
(Electrical Connections) on page 29 for sizes 08-14 and
page 30 for size 16
NOTE: If gas and/or electrical connections are not going
to occur at this time, tape or otherwise cover the fittings so
that moisture does not get into the building or conduit in
the interim.
Original
Position
New Position
(moved 12.5 in.)
REMOVABLE HORIZONTAL
RETURN DUCT OPENING COVER
REMOVABLE HORIZONTAL
S
UPPLY DUCT OPENING COVER
Summary of Contents for 580J*16D Series
Page 4: ...4 Fig 2 Unit Dimensional Drawing Sizes 08 09 and 12 ...
Page 5: ...5 Fig 2 Unit Dimensional Drawing Sizes 08 09 and 12 cont ...
Page 6: ...6 Fig 3 Unit Dimensional Drawing Size 14 ...
Page 7: ...7 Fig 3 Unit Dimensional Drawing Size 14 cont ...
Page 8: ...8 Fig 4 Unit Dimensional Drawing Size 16 ...
Page 9: ...9 Fig 4 Unit Dimensional Drawing Size 16 cont ...
Page 15: ...15 Fig 9 580J 16 Roof Curb Details ...
Page 32: ...32 Fig 58 580J 08 14 Typical Perfect Humidity Dehumidification System Humidistat Wiring ...
Page 33: ...33 Fig 59 580J 16 Typical Perfect Humidity Dehumidification System Humidistat Wiring ...
Page 48: ...48 Fig 67 580J 08 12N P Typical RTU Open System Control Wiring Diagram ...
Page 49: ...49 Fig 68 580J 08 14 Typical RTU Open System Control Wiring Diagram ...
Page 50: ...50 Fig 69 580J 16 Typical RTU Open System Control Wiring Diagram ...
Page 52: ...52 Fig 71 580J 16 Typical RTU Open System Control Wiring Diagram with Perfect Humidity System ...