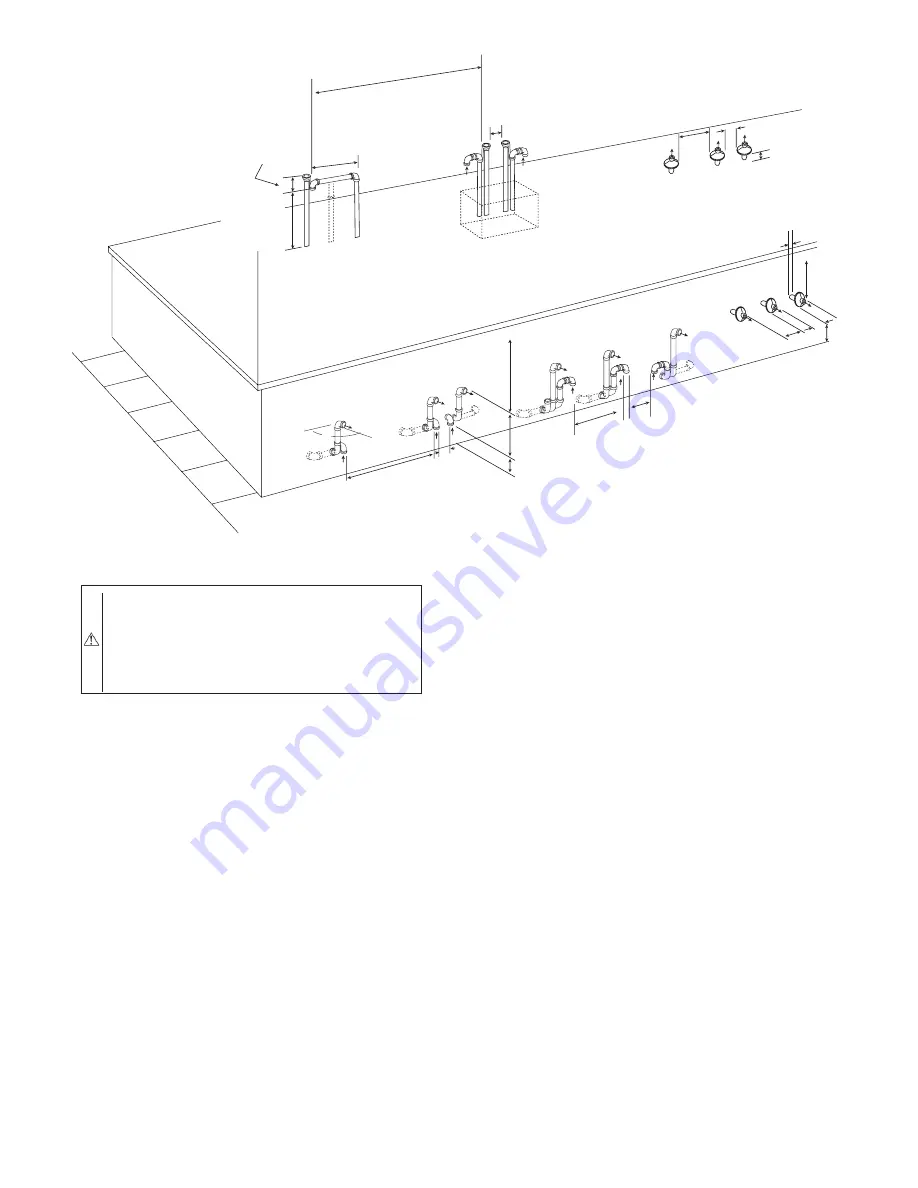
CAUTION:
UNIT DAMAGE HAZARD
Failure to follow this caution may result in unit compo-
nent damage.
Vent pipe must be installed and fully seated against
inducer housing internal stop. Clamp must be tightened to
prevent any condensate leakage.
6. Install casing hole filler cap (factory-supplied in loose parts
bag) in unused vent pipe casing hole.
ATTACHMENT OF VENT EXTENSION PIPE
Furnaces with 100,000 Btuh and larger input are supplied with a
PVC vent extension pipe (2-in. diameter by 12-in. long). This pipe
has a built-in channel to assist vent condensate disposal. When this
vent extension pipe is supplied, it MUST be used to connect the
field vent pipe to furnace inducer housing on ALL upflow and
downflow applications.
NOTE:
See label on vent extension pipe for proper installation.
This pipe may be shortened if an elbow is used to connect vent
extension tube to field-installed vent pipe.
INSTALLATION GUIDELINES FOR COMBUSTION AIR
PIPE AND VENT PIPE
It is recommended that all pipes be cut, prepared, and pre-
assembled before permanently cementing any joint.
1. Attach combustion air pipe and vent pipe per instructions in
sections
″
Combustion Air Pipe
″
and
″
Vent Pipe.
″
2. Working from furnace to outside, cut pipe to required
length(s).
3. Deburr inside and outside of pipe.
4. Chamfer outside edge of pipe for better distribution of
primer and cement.
5. Clean and dry all surfaces to be joined.
6. Check dry fit of pipe and mark insertion depth on pipe.
7. After pipes have been cut and preassembled, apply gener-
ous layer of cement primer to pipe fitting socket and end of
pipe to insertion mark. Quickly apply approved cement to
end of pipe and fitting socket (over primer). Apply cement
in a light, uniform coat on inside of socket to prevent
buildup of excess cement. Apply second coat.
8. While cement is still wet, twist pipe into socket with 1/4
turn. Be sure pipe is fully inserted into fitting socket.
9. Wipe excess cement from joint. A continuous bead of
cement will be visible around perimeter of a properly made
joint.
10. Handle pipe joints carefully until cement sets.
11. Horizontal portions of the venting system shall be supported
to prevent sagging support. Support combustion air piping
(if applicable) and vent piping a minimum of every 5 ft (3
ft for SDR-21 or -26 PVC) using perforated metal hanging
strap.
12. Slope combustion air piping (if applicable) and vent piping
downward towards furnace a minimum of 1/4 in. per linear
ft with no sags between hangers.
13. Horizontal portions of the venting system shall be installed
so as to prevent the accumulation of condensate.
14. Use appropriate methods to seal openings where combus-
tion air pipe (if applicable) and vent pipe pass through roof
or sidewall.
Fig. 42—Combustion Air and Vent Pipe Termination
for Direct Vent (2-pipe) System (All Sizes)
A05090
At least 36 in.
18 in. maximum
Vertical separation
between combustion
air and vent
8 3/4 in. for 3 in. kit
6 3/4 in. for 2 in. kit
Roof Termination (Preferred)
Abandoned masonry
used as raceway
(per code)
At least
36 in.
A
Maintain 12
in.
min. clearance above
highest anticipated
snow level, maximum of
24 in. above roof
Concentric Vent and Combustion Air
Roof Termination (preferred)
1
in.
maximum (type)
12
in.
minimum from
overhang or roof
Maintain 12
in.
min. clearance above
highest anticipated
snow level or grade
whichever is greater
A
At lea
st
36
in.
Concentric Vent
and Combustion - Air
Side Termination
A
At least 36 in.
Side wall termination
of less than 12
in.
12
in.
min from
overhang or roof
12
in.
separation
between bottom of
combustion air and
bottom of vent
Maintain 12
in.
min. clearance above
highest anticipated
snow level or grade
whichever is greater
A
At least 36 in
.
A
Maintain 12 in. min.
clearance above
highest anticipated
snow level
Maximum of 24 in.
above roof
90
°
Note: "A" denotes 0 to < 2 in.
—39—
→