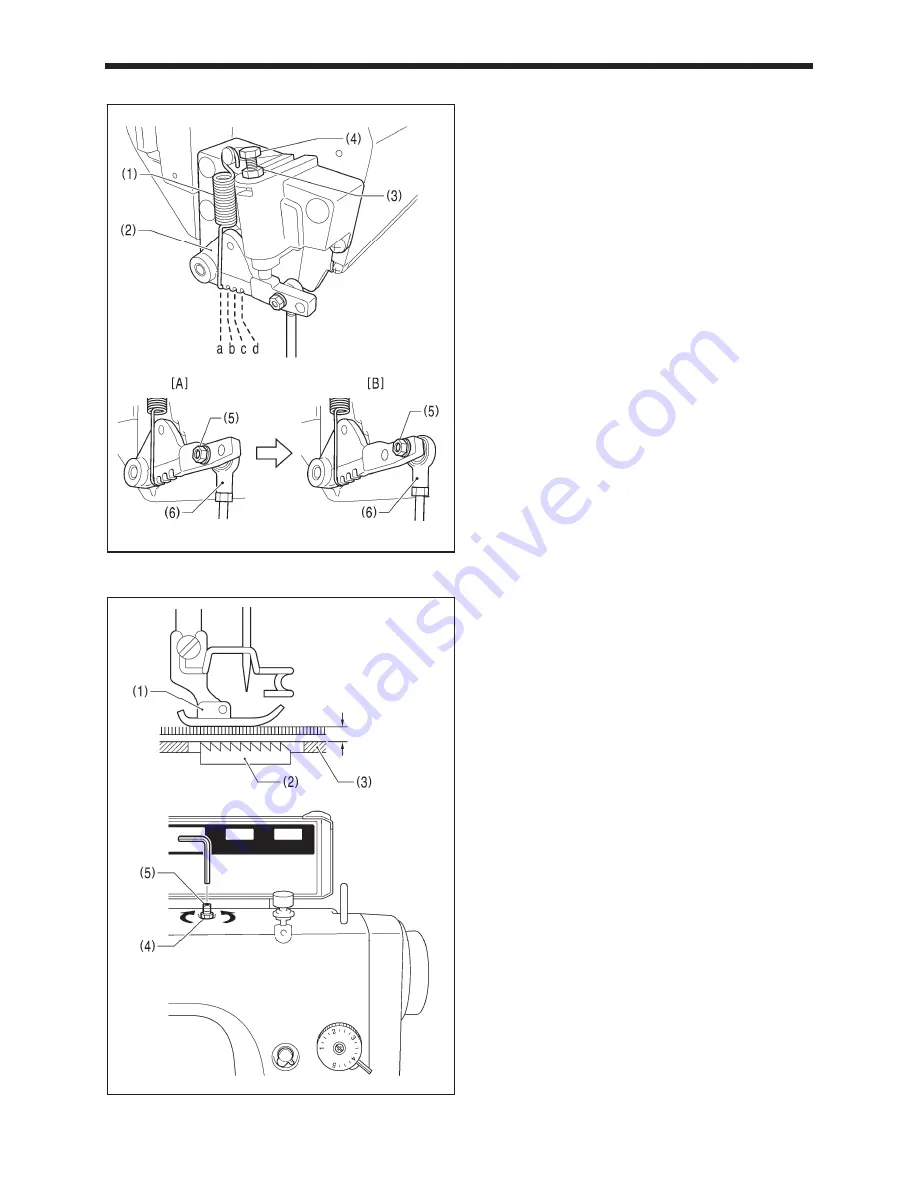
S-7200C
13. STANDARD ADJUSTMENTS
62
13-11. Adjusting the treadle
<Forward depression sensitivity adjustment>
If the machine starts running at low speed when your foot is
simply resting on the treadle, or if the treadle pressure is felt
to be too weak, adjust the position (a to c) at which the
treadle spring (1) is hooked onto the treadle lever (2).
* a is the weakest position, and it becomes gradually
stronger at b, c and d respectively.
<Backward depression sensitivity adjustment>
1. Loosen the nut (3) and turn the bolt (4).
* When the bolt (4) is tightened, the treadle operation
becomes heavier, and when it is loosened, the
operation becomes lighter.
2. Tighten the nut (3).
<
Adjusting the treadle stroke
>
Remove the nut (5), and then move the connecting rod joint
(6) from the position in figure A to the position in figure B.
The treadle stroke will then be increased by approximately
27 %.
At this time, the treadle forward and backward depression
sensitivity will change, so readjust if necessary.
13-12. Adjusting the presser foot floating amount (minute lifting amount)
When sewing stretch materials and materials with long pile,
you can make minute adjustments to the floating amount for
the presser foot (1) in accordance with the material.
1. Turn the sewing machine pulley by hand to move the feed
dog (2) below the needle plate (3).
2. Use the lifting lever to lower the presser foot (1).
3. Loosen the nut (4).
4. Use a hexagon wrench to turn the adjusting screw (5) to
adjust the floating amount.
・
To raise the presser foot (1) ...
Turn the adjusting screw (5) clockwise.
・
To lower the presser foot (1) ...
Turn the adjusting screw (5) counterclockwise.
5. Tighten the nut (4).
* After making the adjustment, sew a piece of material to
check the floating amount.
4259M
2307M
Floating amount
Raise
Lower
4310M
4260M