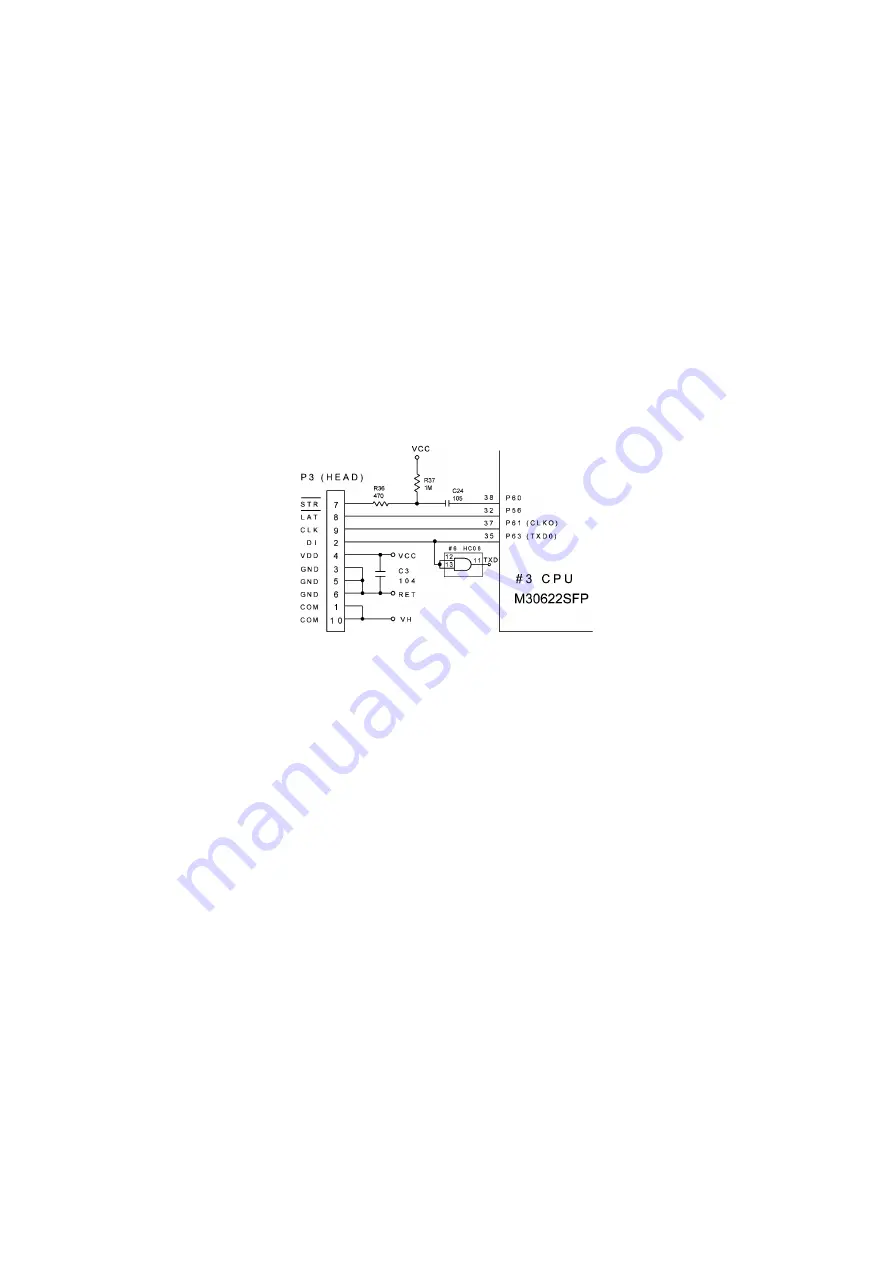
III
- 18
3.2.11
Thermal Print Head Control Circuit
Figure 3.2-14 shows the thermal print head control circuit. The print head integrates a heat
generator (consisting of 128 heating elements vertically aligned in 180 dpi) and a pair of built-in
driver ICs which are designed for 64-element control and cascaded with each other.
Synchronizing with the 2 MHz clock on pin 37 (P61, CLK0), the CPU outputs serial print data
containing 128-dot frame (8 x 16 bit map) through pin 35 (P63, TXD0) to the drivers, printing 96-
dot data in practice.
If the CPU runs out of control, this circuit cuts off power to the thermal head after the specified
time length by the CR time constant of C24
•
R37.
Figure 3.2-14 Thermal Print Head Control Circuit
Summary of Contents for P-Touch PT-530
Page 1: ......
Page 2: ...SERVICE MANUAL MODEL PT 530 550 ...
Page 5: ...Chapter I SPECIFICATIONS ...
Page 11: ...I 5 n PT 550 USA UK Figure 1 1 2 Key Arrangement 1 ...
Page 12: ...I 6 Germany France Figure 1 1 2 Key Arrangement 2 ...
Page 13: ...I 7 Belgium n PT 530 USA Figure 1 1 2 Key Arrangement 3 ...
Page 15: ...Chapter II MECHANISMS ...
Page 54: ...Chapter III ELECTRONICS ...
Page 57: ...III 2 Figure 3 1 1 Control Electronics of PT 550 ...
Page 59: ...III 4 Figure 3 2 1 Block Diagram of Main PCB ...
Page 76: ...III 21 Figure 3 2 16 Voltage Detector Circuit and Temperature Sensor Circuit ...
Page 83: ...Chapter IV TROUBLESHOOTING ...
Page 86: ...IV 2 4 1 3 Troubleshooting Flows 1 Tape feeding failure ...
Page 87: ...IV 3 ...
Page 88: ...IV 4 ...
Page 89: ...IV 5 2 Printing failure ...
Page 90: ...IV 6 ...
Page 91: ...IV 7 ...
Page 92: ...IV 8 3 Powering failure Nothing appears on the LCD ...
Page 93: ...IV 9 ...
Page 94: ...IV 10 ...
Page 95: ...IV 11 4 No key entry possible ...
Page 96: ...IV 12 5 Abnormal LCD indication ...
Page 97: ...IV 13 6 Tape cassette type not identified ...
Page 98: ...IV 14 7 No color printing this applies to the PT 550 European versions only ...
Page 99: ...IV 15 8 Interface port failure this applies to the PT 550 European versions only ...
Page 100: ...APPENDICES Circuit Diagrams A Main PCB B Power Supply PCB ...
Page 101: ......
Page 102: ...B Power Supply PCB ...
Page 103: ......