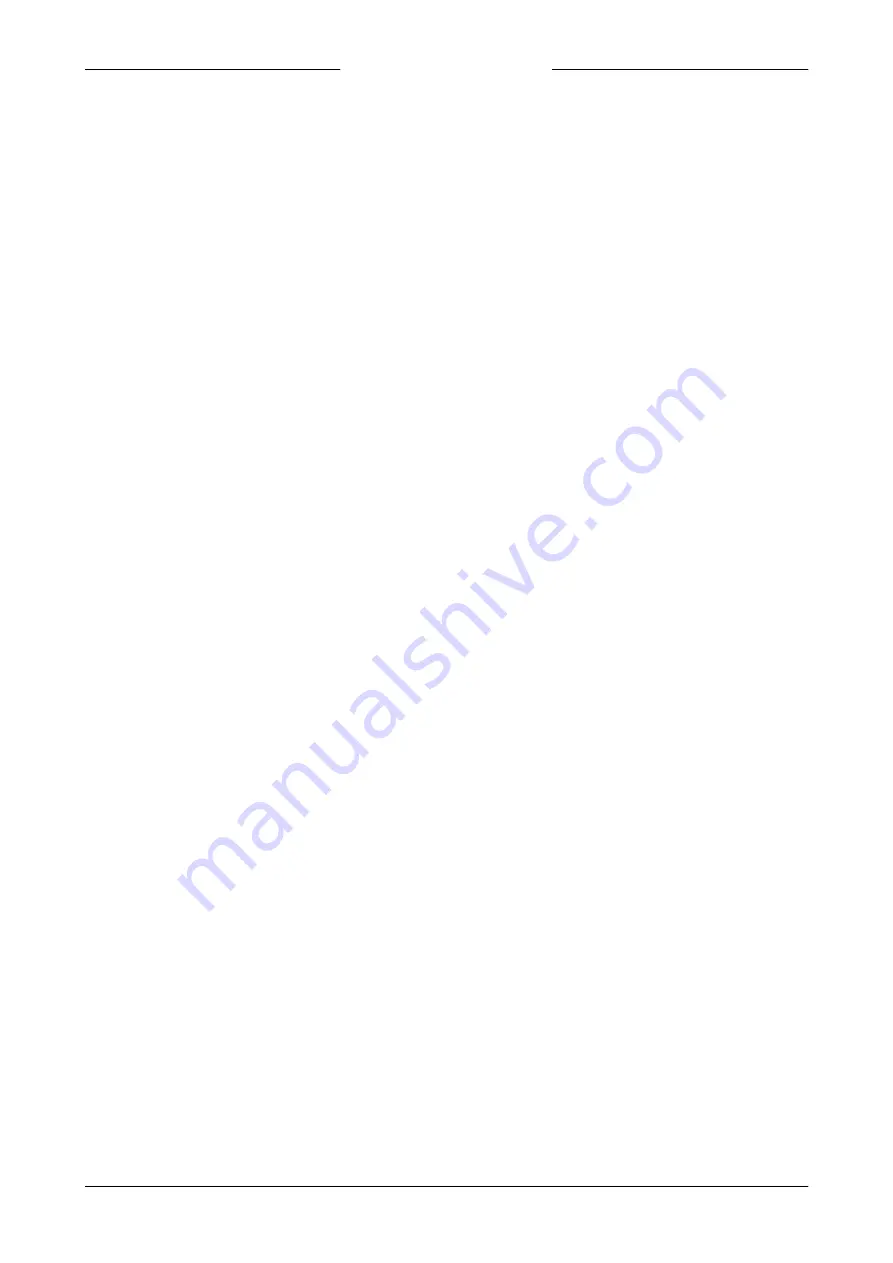
Bronkhorst®
Instruction Manual EL-PRESS™
9.17.101I
45
Parameter index
Parameters
Parameters - Alarms
Alarm Delay Time
Alarm Info
Alarm Maximum Limit
Alarm Minimum Limit
Alarm Mode
Alarm New Setpoint
Alarm Setpoint Mode
Reset Alarm Enable
Parameters - Device identification
BHT Model Number
Customer Model
Device type
Firmware version
Identification number
Serial Number
User Tag
Parameters - Master/Slave
Master Node
Slave Factor
Parameters - Measurement and control
Analog Input
Controller Hysteresis
Fmeasure
Fsetpoint
Measure
Sensor Type
Setpoint
Setpoint Slope
Valve Output
Parameters - Network configuration
Fieldbus1 Address
Fieldbus1 Baud Rate
Fieldbus1 Parity
Fieldbus2 Address
Fieldbus2 Baud Rate
Fieldbus2 Parity
Parameters - Special
Control Mode
Init Reset
IO Status
Reset
Wink