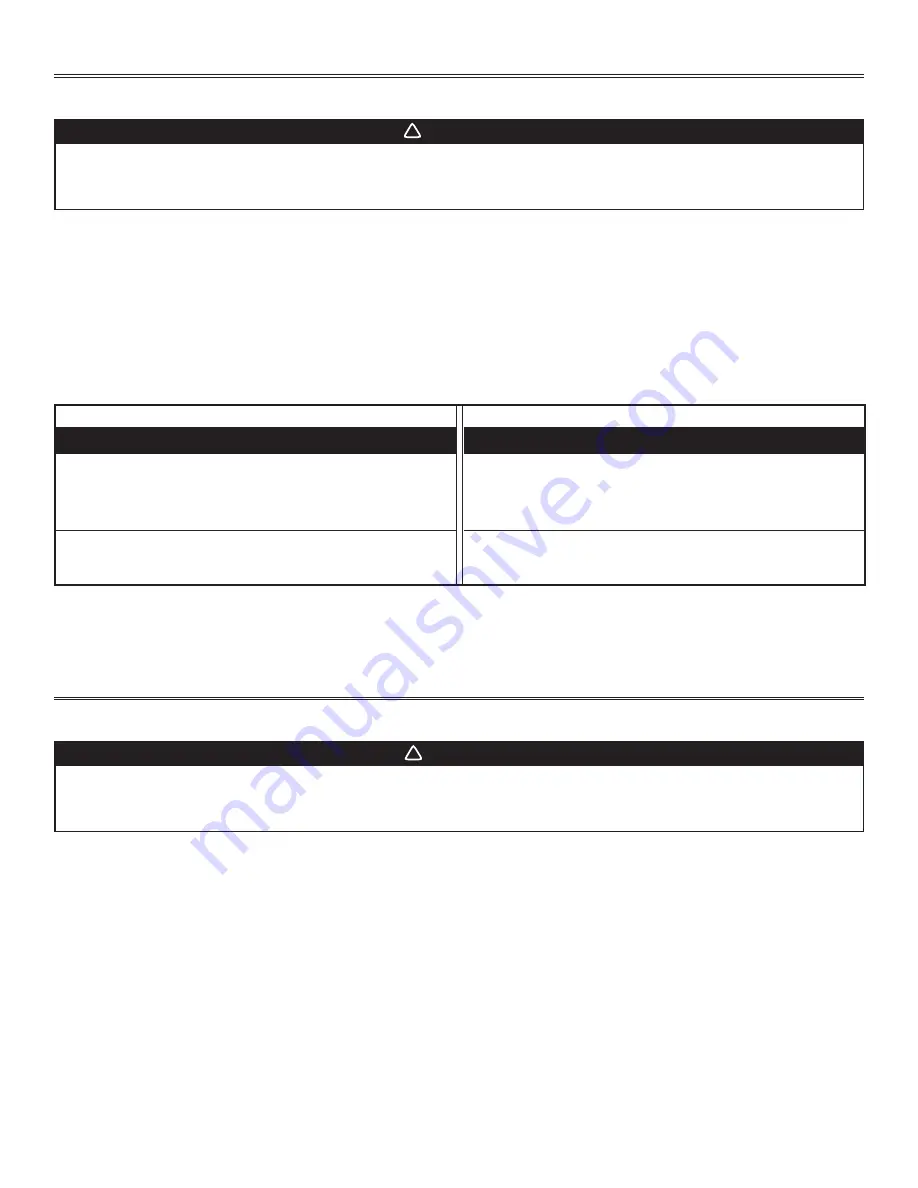
8
5. Maintenance (cont’d)
5.2 Annual Maintenance
Annual maintenance should include:
A
IR
F
ILTERS
Vacuum and wash standard foam fi lters. Replace medium effi ciency fi lter if present.
D
RAIN
P
ANS
AND
I
NTERIOR
OF
U
NIT
Wash the foil faced insulation surfaces and wipe the drain pans with a soft cloth and mild cleaning solution. Check the drain fi ttings to
ensure they are draining freely.
R
ECOVERY
C
ORE
The recovery core must be handled with care. It is recommended that it be washed once a year following the season of most intense
use, in order to ensure maximum effi ciency of the partitions.
F
ANS
Blower wheels and fan housing should be checked for dirt build-up. If they appear dirty, it may be necessary to remove the blower
assembly and then vacuum the dust out through the fan mouth. See next page for instructions on removing the blower assembly.
WARNING
!
Risk of electric shocks. Before performing maintenance or repairs, always stop the unit, then turn power off at
service panel. The wearing of safety glasses and gloves is recommended when handling unit components to
prevent injuries caused by sharp edges.
H
EAT
R
ECOVERY
C
ORE
ERV HM C
ORE
CAUTION
CAUTION
Hot water and a strong cleaning agent could damage
the polypropylene core. Ensure the core is returned to
the unit in the correct orientation. Use the sticker as a
guide.
Do not soak the ERV HM core in water. This core can
easely be damaged especially if it is soaked.
Allow the heat recovery core to soak for three hours in warm water
and mild soap. Rinse under a heavy stream of water.
For ERV HM core, use a vacuum cleaner or low pressure air jet. It
is not recommended to use solvents or detergents as these may
damage the media or structure of the core.
6. Service
6.1 Parts Replacement
S
YSTEM
O
PERATION
C
HECK
Verifi cation of all control modes should be checked to ensure proper operation. Refer to
3.2 Sequence of Operation section.
T
ESTING
AND
R
EPLACEMENT
OF
THE
D
AMPER
A
CTUATOR
Check damper operation by switching between LOW - COM or HIGH - COM on the dry contact terminal or by switching through the
modes on the optional remote wall control. If the damper does not respond in one or both directions, check all connections.
CAUTION: 120 VAC.
Check for 120 volt output across the WHITE/BLACK wires. If 120 volts can be measured at the motor, replace
the motor. If 120 volts cannot be measured at the motor, check pins J1-9 at the printed circuit board.
M
AIN
C
IRCUIT
B
OARD
R
EPLACEMENT
The main circuit board must be replaced if an electronic problem arises. For example, the unit suddenly stops, the unit stays in defrost
all of the time or if control functions are not working properly. Ensure that power is reaching the board. Test the blower motors and
damper actuators for operation when directly connected to the appropriate power voltage. If the motor and damper actuators function
normally, replace the main circuit board.
WARNING
!
High voltage, risk of electric shocks. Only qualifi ed service personnel should service this equipment. The wearing
of safety glasses and gloves is recommended since a few diagnosis procedures may require the unit to be in
operation while proceeding. Be careful with moving and live parts to prevent injuries.