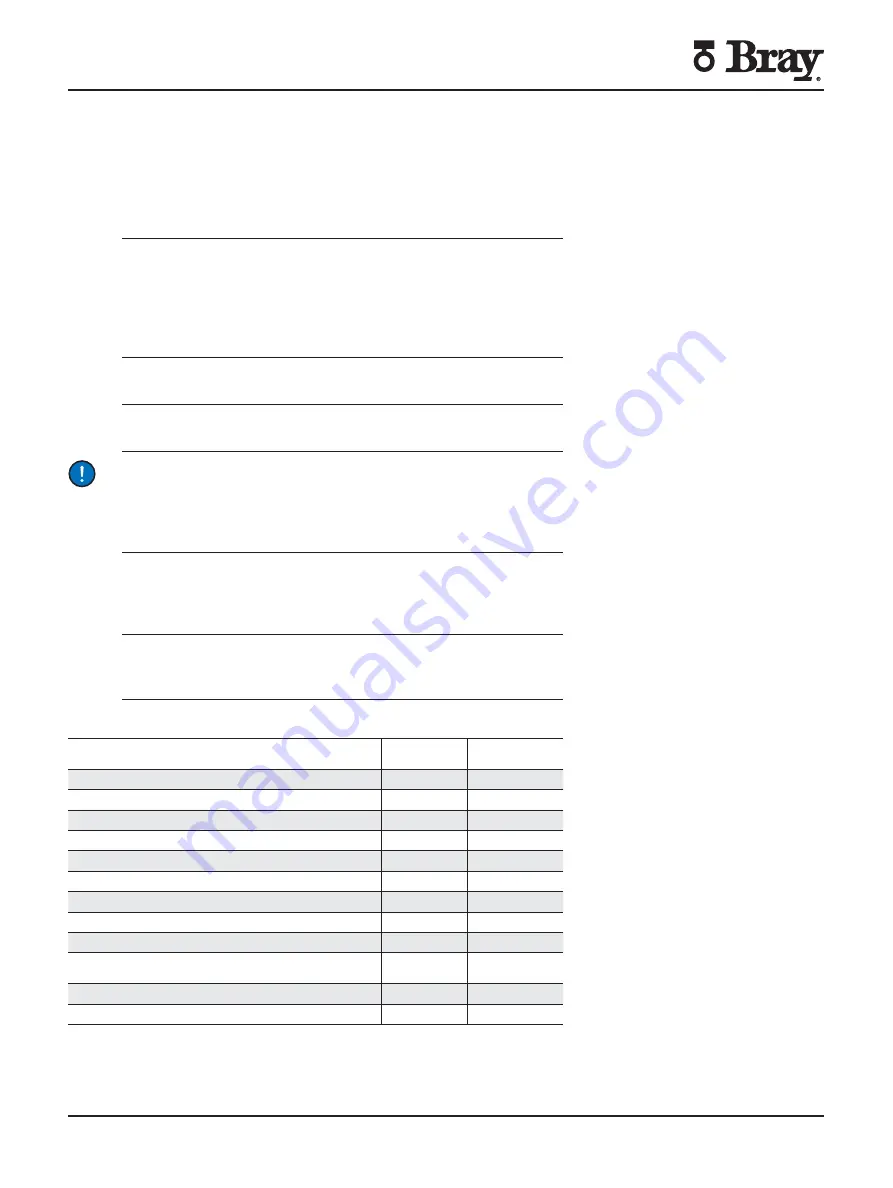
FLOW-TEK FTG SERIES
MANUAL GEAR OPERATOR
Installation, Operation, and Maintenance Manual
10 of 11
© 2022 BRAY INTERNATIONAL, INC. ALL RIGHTS RESERVED. BRAY.COM The Information
contained herein shall not be copied, transferred, conveyed, or displayed in any manner that would
violate its proprietary nature without the express written permission of Bray International, Inc.
5.0
GEAR LUBRICATION
FTG gears come from the factory with lubricant already applied.
Proper lubrication is necessary to ensure smooth operation and
long life of the unit. These instructions are to be used during
original assembly and prior to reassembly following service or
scheduled maintenance.
Worm and worm gear -
lubricate both hubs and shoulders, apply
grease to the worm and worm gear teeth in such a way that it
is carried through the meshing of the gears. After applying the
grease, rotate the worm at least two (2) complete cycles (one
cycle being from closed-open-closed or open-closed-open). After
cycling inspect and re-apply grease as needed.
Apply grease liberally to all mating surfaces, O-rings, gaskets,
and shafts.
Cover inside of gear box with thin layer of grease as to prevent
rust build up caused by condensation.
NOTICE
Gear operators intended for marine service, high-humidity, or
buried service, and so specified on the Purchase Order or Sales
Order, must have housing(s) filled with grease and properly
sealed.
The lubricant must be a high-pressure or extreme pressure
petroleum grease with a lithium based thickener, which meets the
NLGI Grade 2. The grease must exhibit a high degree of tackiness,
which enhances its ability to cling to the intended surfaces.
The grease should meet the following specifications as a
minimum. Any deviation below these specifications must be
approved by Flow-Tek Engineering.
Typical Properties
ASTM
Test Method
Result
NLGI
1
Grade Number
–
2
Soap Type
–
Lithium
Color
–
Brown
Mineral Oil Viscosity, SUS @ 210°F [100°C]
D2161
80
Penetration (Worked 60 Strokes)
D217
285
Dropping Point (Maximum Temperature)
D566
363°F [184°C]
Oil Separation
D1742
5.0%
Rust Preventative Test
D1743
Pass
Timken EP Test
D2509
45 lbs [20.4 kg]
Wheel Bearing Test
(60 mph [660 rpm] 250°F [121°C] leakage)
D1263
2.8 gms
Oxidation Stability 100 hrs, psi drop
D942
6
Water Washout Test (% loss @ 175°F [80°C], typ.)
D1264
7
1
National Lubricating Grease Institute