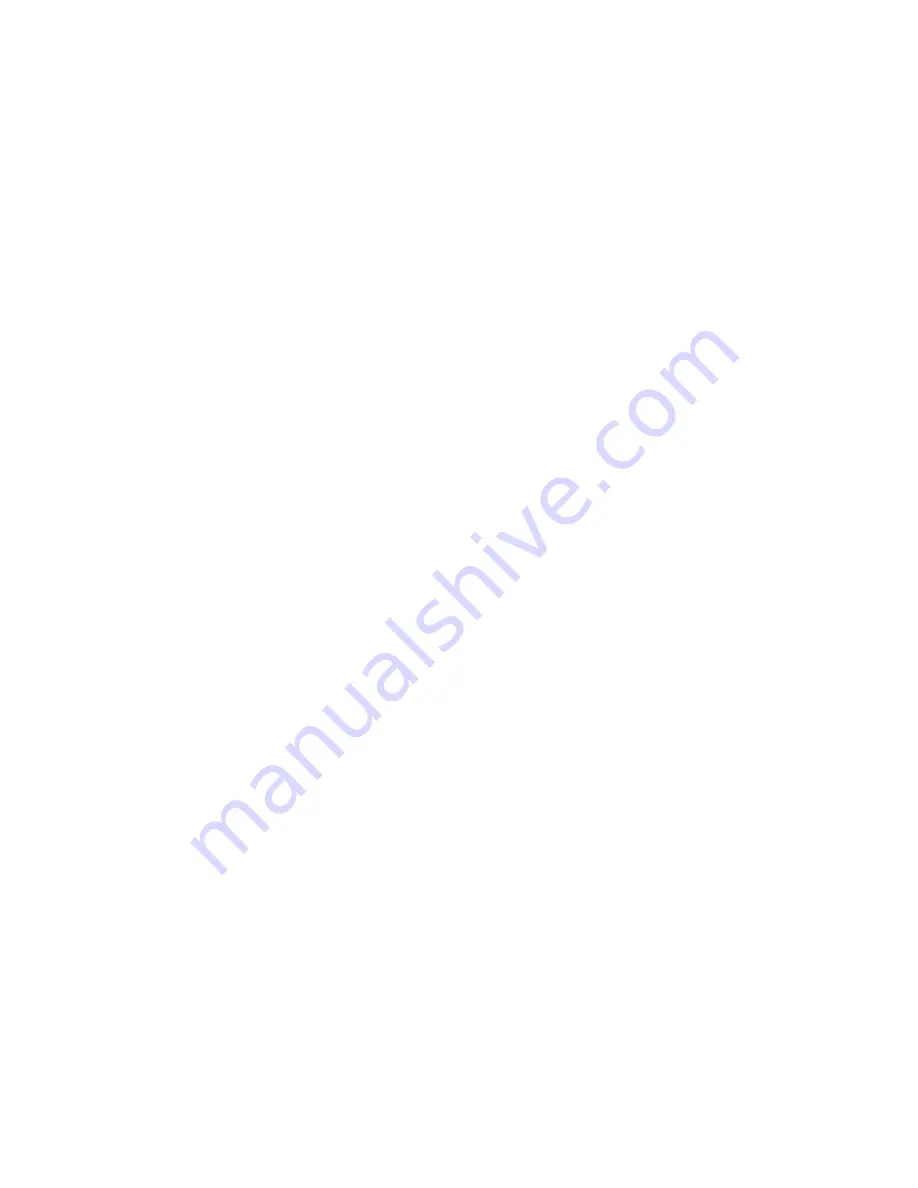
4
the rear frames in place. Detail the rear frames as shown in Fig.7.
Bend part F36 to shape and solder around part F35 to make the lower firebox. Add the washout plugs at the corners from
0.5mm square wire and the blowdown tap (part BR6), before soldering in place on top of part F25. Add part F37 as shown in
Fig.7.
Fold up the spring wire bracket and side play stops on part F33. Fold up part F34 and attach part F33 and check for free, but
not sloppy, movement in the hornguides. Solder the small top hat bearings in place and fit the radial truck wheels using the
washers (part F40) to eliminate any side play. Bend up the spring wire to give some downward pressure and solder in place
through the bracket on part F25 and the hole in part F4. The radial truck is retained with lengths of 0.5mm square wire
soldered across the bottom of each horn guide.
SECTION 9: PONY TRUCK
Emboss all the frame rivets as shown in Fig.10. Solder guard irons (part P3) in place on the outside of the frames. Fold up
part P6 or part P10 and solder the appropriate stays in place as shown in Fig. 10. For the original pony truck form the dust
shields (part P8) to shape and solder in place. Solder parts P1 and P2 together to make the radius arm as shown in Fig. 10.
Solder the radius arm in place. Attach part WM3 and ream through the axle holes 2mm.
Using appropriate washers (part P4) fit the wheels so that there is a minimum of side play. Form the guard irons to shape.
Bend up the spring wire (0.3mm phosphor bronze) to give some downward pressure and solder in place through the holes
in part P5. The pony truck is retained with a 10 BA screw.
SECTION 10: COMPLETING THE CHASSIS MECHANICALLY
Emboss the rivets in parts F16 & F17. Now fold these components to the correct angle using the jig (part F42) as a guide. Pass
part F6 (short side on the left) through the slots in parts F16 and locate all three components on the frames. Check that all is
correctly located, before soldering in place. Similarly solder parts F17 in place. Check the angle of parts F16 & F17 again using
the jig.
Chamfer the curved edges of the splasher tops, parts F18 & F19, and curve to shape over a suitable rod. Now solder them in
place over the top of the frames and against the angle plate. Now trim the excess material from the outer edges of the angled
plate and round off the rear corner as shown in Fig.3. Solder part F15 to the lower edges of part F6 and trim to length. Solder
in place parts F12 and the brake hanger pivots from 0.45mm wire (Fig.3).
In P4, the clearance between the leading crankpin and the slidebar is very limited. Potential problems here can be tackled
by:
Using a recessed crankpin nut as sold by Ultrascale
Ensuring side play on the leading axle is kept to an absolute minimum
Omitting one lamination of the slidebars (LEFT 2 & RIGHT 2).
Fit the crankpins to the wheels making sure the screw heads do not foul, countersinking them if necessary. Attach the balance
weights to the wheels as in Fig. 19. Assemble the wheel sets, bearings and motor/gearbox selecting 1/8" axle washers of
appropriate thickness to control side play.
The cranks on the right hand side should lead the left by 120°. I find the easiest way to achieve this consistently on all three
axles is by looking through the wheels with a magnifier against a strong light and lining up corresponding spokes. The wheels
have 18 spokes which gives 20° between each spoke. 20° x 6 = 120°. So you simply adjust the wheel sets until the right hand
side is 6 spokes ahead of the left. This method is surprisingly accurate and, for me at least, gives by far the best results.
Now connect the motor to your pick-ups and test run.