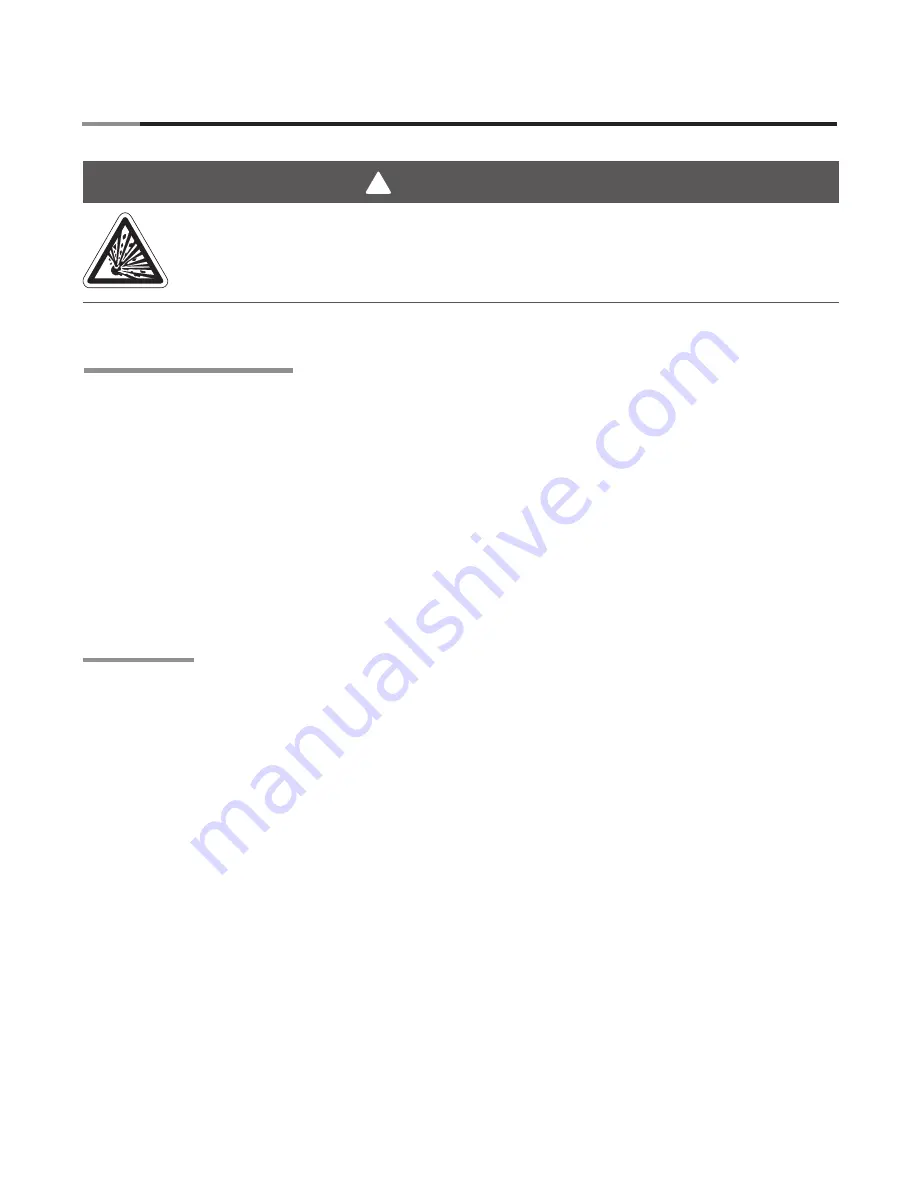
WARNING
!
47
DES3
Series
4.0
Operation • Sequence of Operation • Thermostat
4.0
Operation
Sequence of Operation
Starting Circuit:
Upon a call for heat, the fan is energized. Once operational static pressure is achieved,
the differential switch will close initiating the ignition sequence. After a 7-second pre-purge, the spark
electrode is energized and the gas valve opens. The trial for ignition is 15 seconds. If flame is not
sensed, the heater will attempt two (2) additional ignition sequences before proceeding into hard
lockout.
Running Circuit:
After ignition, the control senses and monitors burner flame through the electrode. If
sense of flame is lost, the control immediately disrupts power to the gas valve and then re-cycles the
unit (identical to the starting sequence). If flame sense is not established within 15 seconds, the
heater will attempt two (2) additional ignition sequences before proceeding to hard lockout. The
control can be reset by briefly interrupting the power source.
Thermostat
NOTE:
Different thermostats operate according to their particular features. Refer to thermostat
specifications for details.
This heater must be installed and serviced by trained gas installation and service
personnel only.
Do not bypass any safety features or the heater’s built in safety mechanisms will be
compromised.