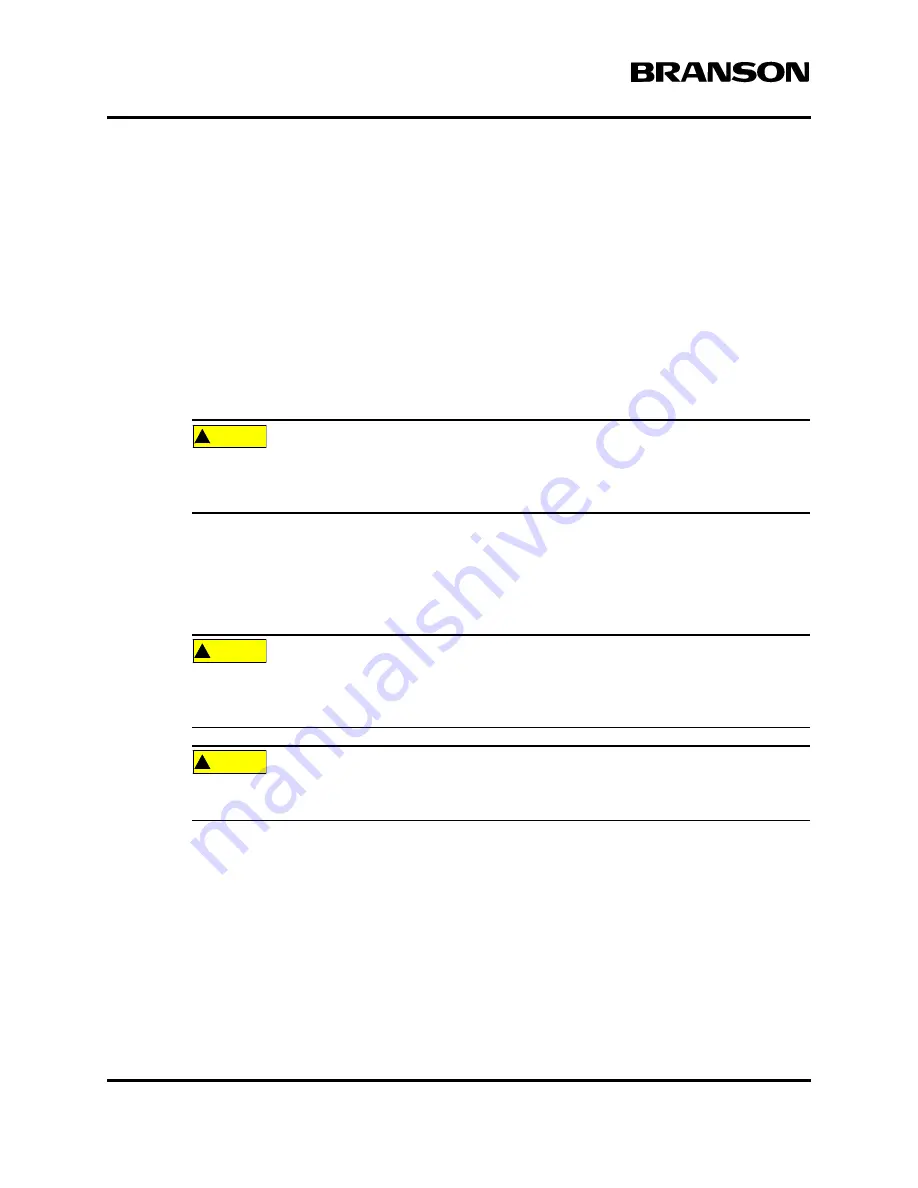
4-20
100-214-276 Rev. 3
Chapter 4: Installation and Setup
Installation Steps
3.
Connect factory air to the air hose on the stand (1/4 NPT male fitting on the hose). A quick-discon-
nect fitting is suggested. Use a lockout device on the air line if required.
4.
Verify the base/start switch control cable is properly connected to the
back of actuator
.
5.
Verify the linear encoder connector is properly connected to the
back of the actuator
.
6.
Use jack screws to fine adjust the system level. A 3/16" allen wrench should be used for the 3/8"-
16 x 3/4" jack screws.
7.
Verify earth ground is connected with #8 gauge wire to the ground terminal on the rear of the
actuator.
4.5.3 Actuator (Alone)
The actuator (alone) is intended for installation on your custom-made mounting support. It is located in
place with a mounting pin and secured using three metric bolts.
CAUTION
!
In a custom installation, the actuator must be mounted on an I-beam or other rigid structure.
The mounting surface must be flat within 0.004 in (0.1mm) Total Indicator Reading, in a
tolerance zone of 16 x 3.5 in (410 x 90 mm).
1.
Lift the actuator from the box. Carefully lay the assembly on its right side (NOT on the side with the
linear encoder).
2.
Use of a guide pin is suggested. It is not provided with the actuator. If you require a guide pin, use
a solid metal dowel pin, 12mm diameter, which must not extend into the actuator more than 0.40
inch (10mm) from your support.
CAUTION
!
The actuator support bolts for the 2000X-Series actuators are metric, M10 x 1.5 thread pitch,
25mm long. The support pin and mounting bolts must not extend more than 0.40 in (10 mm)
into the actuator, otherwise, binding or damage to the carriage may occur.
CAUTION
!
DO NOT use 900-Series M10 x 1.25 mounting bolts. They have a different thread pitch and
will not interchange with those used on the 2000X-Series
DOC EXPIRES 12PM 7/24/2012. Article or Material must comply with the requirements
stipulated by RoHS in its current version