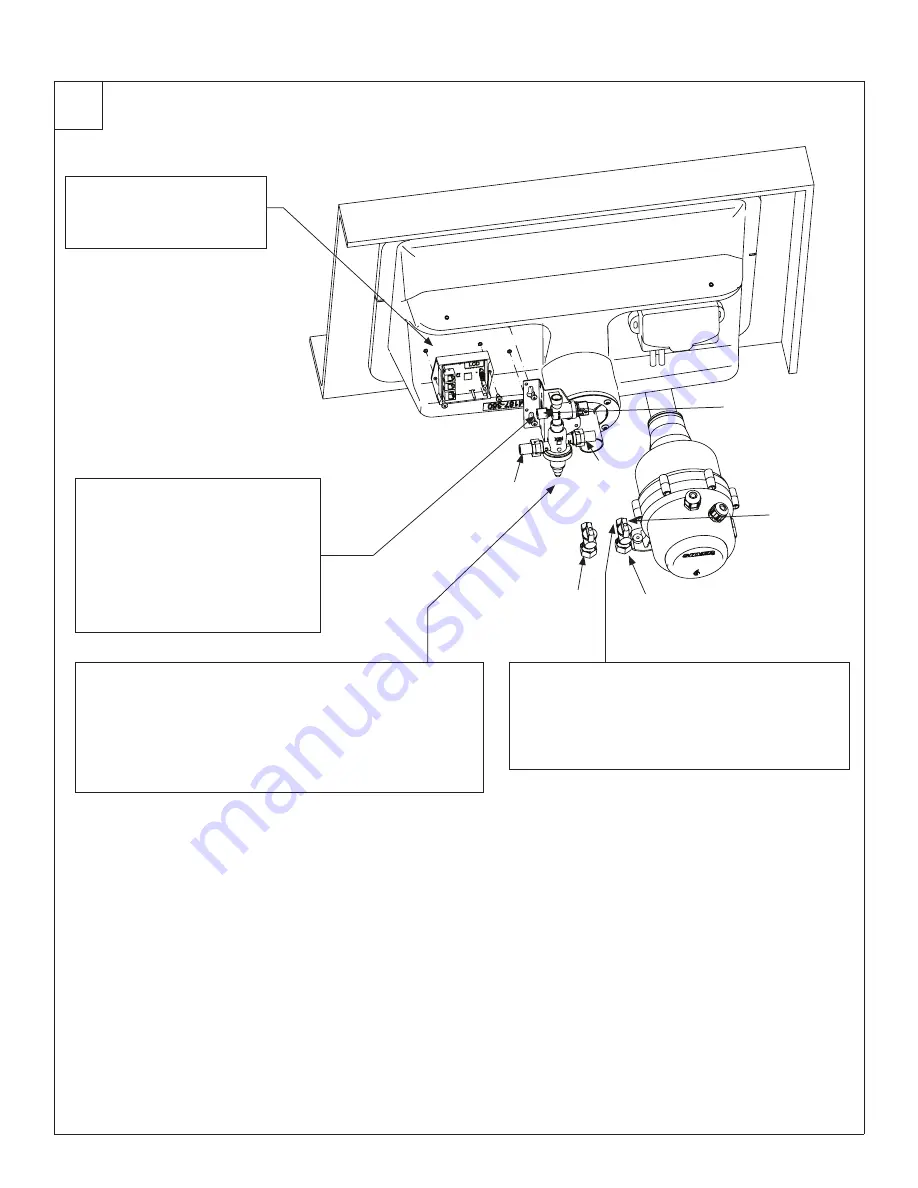
LD-5010
Installation
18
8/24/2017
Bradley
• 215-1869 Rev. B; ECN 17-11-004B
Control Box and Valve Installation
10
Secure control box to
underside of bowl using
(2) #10 x 1/2" long screws
provided.
A
1/4" Water Supply
Outlet with
Compression Nut
Cold Supply
Hot Supply
Cold
Hot
Attach 1/4" supply tube from the
WashBar to the 1/4" supply valve
outlet. Loosen the compression
nut on the valve body. Push the
1/4" supply tube firmly into the
tube connector until it is fully
seated. Tighten the compression
nut by hand.
B
For thermostatic mixing valve installation, secure 1/2" supply
hose to hot water supply valve inlet. Secure the other supply
hose from cold water supply to cold water supply valve inlet.
Secure valve to bowl using (2) #10 x 1/2" long screws.
For tempered line installation, secure 1/2" supply hose
to tempered water supply and TL valve inlet (not shown).
Secure valve to bowl using (2) #10 x 1/2" long screws.
C
3/8"
Compression
Nut
Remove 3/8" compression nut/sleeve from the
hot and cold supply stop valves. Connect 3/8"
end of flexible supply hose to 3/8" compression
on supply stop valve. Ensure hot and cold supply
hoses are connected to hot and cold supply stop
valve. For TL option, only connect cold supply.
D