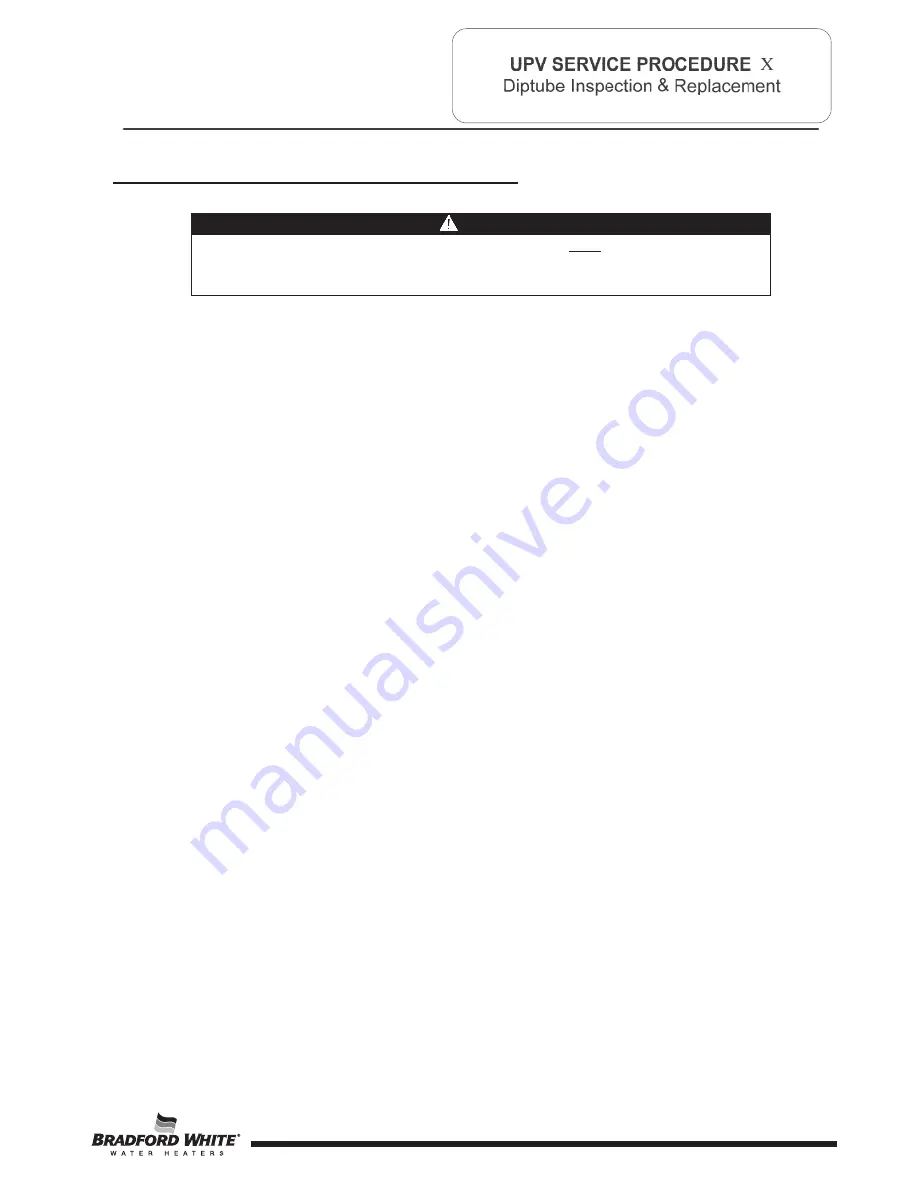
31
UPV Series
31
Diptube Inspection & Replacement
Step 1. Position on/off switch of gas control valve to “OFF” position and unplug water
heater from wall outlet.
Step 2. Turn off cold water supply to water heater. Connect hose to drain valve of water
heater and route to an open drain. Open a nearby hot water faucet to vent
heater for draining. Open drain valve of water heater and allow heater to drain
to a point below the inlet connection nipple.
Step 3. Disconnect inlet nipple from plumbing system.
Step 4. With an appropriate tool such as a pipe wrench, remove inlet nipple/diptube
from the water heater. Use caution not to damage pipe threads.
Step 5. Visually inspect inlet nipple/dip tube. Inlet nipple/diptube should be free of
cracks and any blockage. Hydrojet slots should be open and free of any
blockage. Any damage such as cracks, restriction due to deformation or
unintentional holes are not field repairable and the inlet nipple/dip tube must be
replaced.
Step 6. Upon completion of inspection or subsequent replacement, reinstall inlet
nipple/dip tube into water heater. Ensure pipe dope is used on the nipple’s
threads. Connect nipple to plumbing system, resume water supply and refill
with water.
Step 7. To resume operation follow the instructions located on the lighting instruction
label or the lighting instructions located in the installation and operation manual.
WARNING
Water Heater components and stored water may be HOT when performing the
following steps in this procedure. Take necessary precaution to prevent
personal injury.