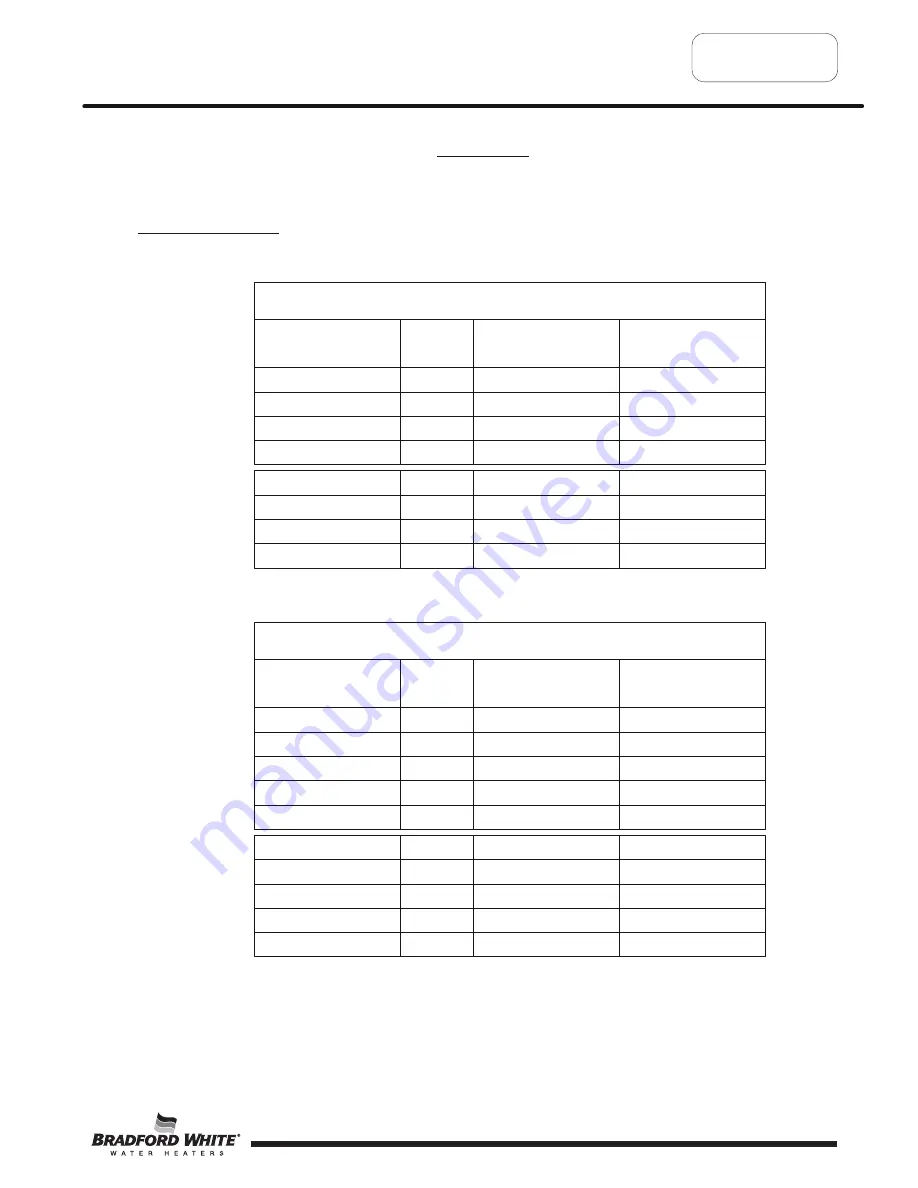
Specifications
V
enting Specifications
:
Through
the
Wall
Terminating
#
of
E
lbows
M
aximum
Length
ft
(m)
M
inimum
Length
ft
(m)
3
"
Diameter
(
7
.
6
cm)
PVC
Vent
Connector
Lengths
1
4
5 (
1
3
.
7)
2
(.
6
)
Through
the
Wall
2
4
0 (
12.2
)
2
(
.6
)
Through
the
Wall
3
35
(
1
0.
7
)
2
(
.6
)
Through
the
Wall
4
30
(9.
1
)
2
(
.6
)
Through
the
Wall
Terminating
#
of
E
lbows
M
aximum
Length
ft
(m)
M
inimum
Length
ft
(m)
4
"
Diameter
(
1
0.2
cm)
PVC
Vent
Connector
Lengths
1
17
5
(53.3)
1
0
(3.
1
)
Through
the
Wall
2
17
0
(5
1
.
8
)
1
0 (3
.1
)
Through
the
Wall
3
16
5
(50.3)
1
0 (3
.1
)
Through
the
Wall
4
16
0
(4
8
.
8
)
1
0 (3
.1
)
Through
the
Roof
0
50
(
1
5.2)
7
(2.
1
)
Through
the
Roof
1
4
5 (
1
3
.
7)
7
(2.
1
)
Through
the
Roof
2
4
0 (
12.2
)
7 (
2.1
)
Through
the
Roof
3
35 (
1
0
.
7)
7 (
2.1
)
Through
the
Roof
0
18
0
(54.9)
1
5
(4.
6
)
Through
the
Roof
1
1
75 (53
.
3)
1
5 (
4.6
)
Through
the
Roof
2
1
70 (5
1.
8)
1
5 (
4.6
)
Through
the
Roof
3
16
5 (50
.
3)
1
5 (
4.6
)
Through
the
Wall
5
1
55
(4
7
.2)
1
0 (3
.1
)
Through
the
Roof
4
16
0 (
4
8
.
8)
1
5 (
4.6
)
V
ent
T
a
bl
es
Page
7
7