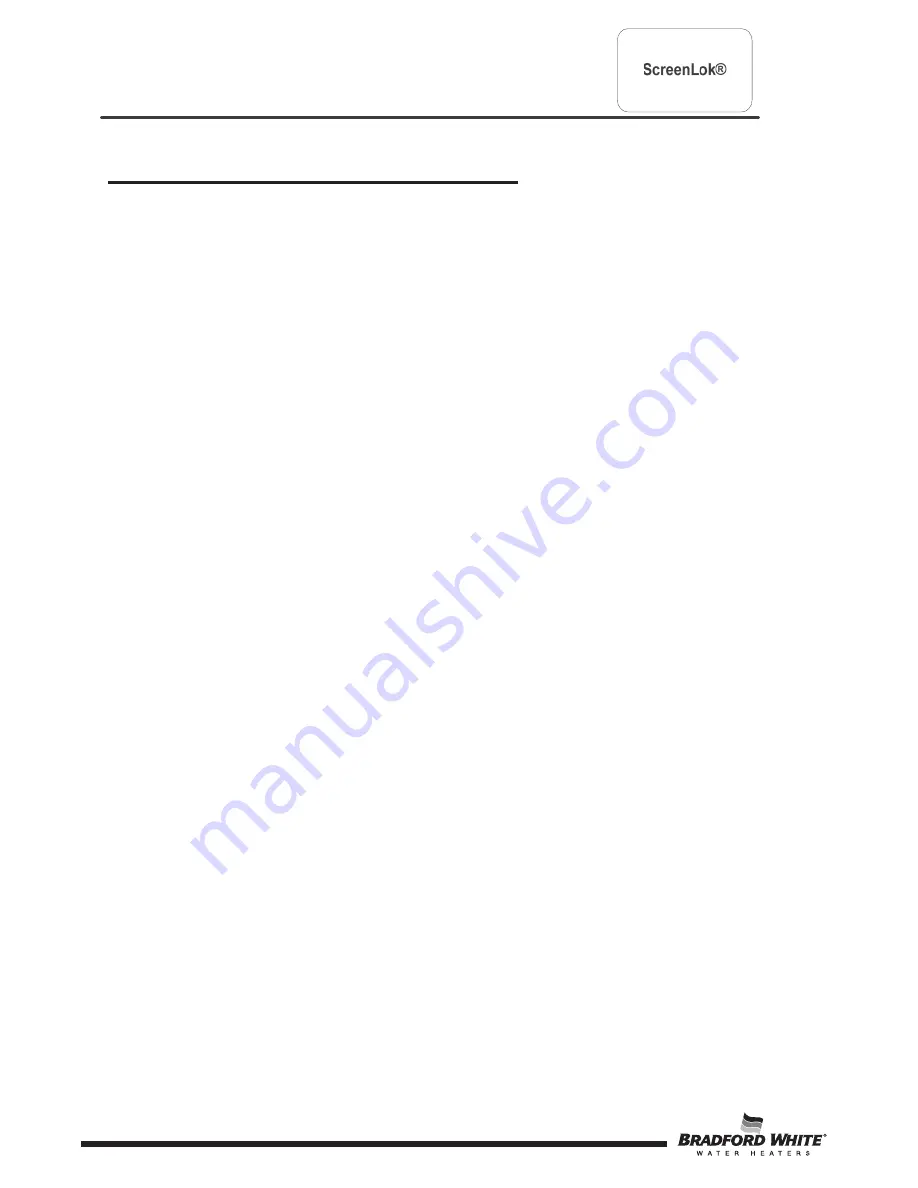
34
Res. D Series
34
ScreenLok
®
Flame Arrestor Cleaning
Step 1. Position Gas Control power switch to the “OFF” position.
Step 2. Remove outer door.
Step 3. Remove outer jacket door and inner door per service procedure IX on page 25.
Step 4. Disconnect main burner feedline (3/4” wrench), pilot tube (7/16” wrench) and
igniter/flame sensor wire from gas control and remove burner assembly from
combustion chamber.
Step 5. Clean ScreenLok
®
Flame Arrestor using a stiff brush, compressed air and/or
shop vacuum to remove any scale or other debris accumulation. Using a soft
brush, clear jacket openings from any dirt, dust, restrictions or other obstructions.
Step 6. Remove any debris from the burner assembly per procedure D-I on page 13 and
reinstall burner assembly into combustion chamber.
Step 7. Reconnect the feedline, pilot tube and igniter/flame sensor wire to the gas control
Step 8. Reinstall the outer jacket door and the inner doors per service procedure D-IX on
page 27.
Step 9. To resume operation follow the instructions located on the lighting instruction
label or the lighting instructions located in the Installation and Operation manual.