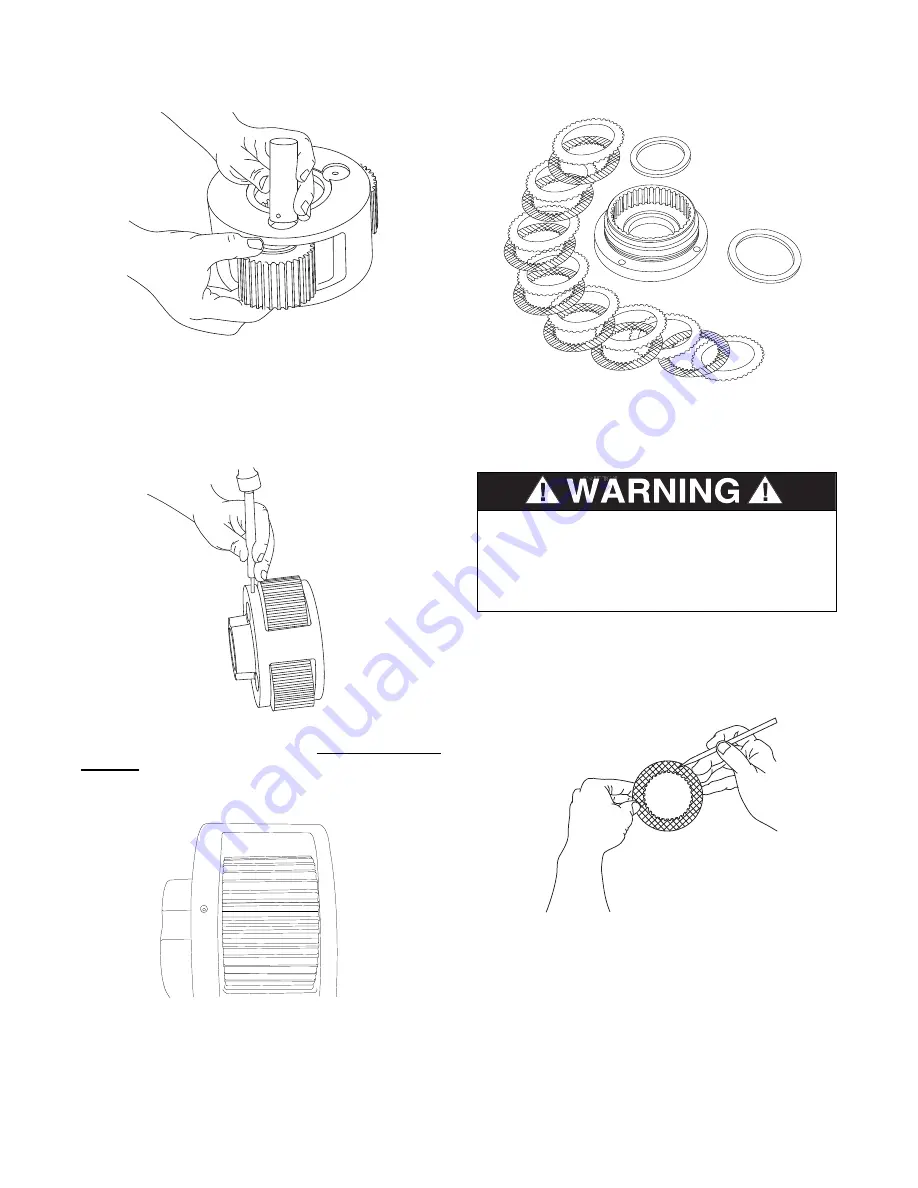
STATIC BRAKE SERVICE
1. Remove all friction and steel discs (items 27 & 28)
and both spacer plates (item 24) from the motor adapter.
1. Thoroughly clean and inspect all parts at this time.
Check brake piston sealing surfaces on motor adapter
and brake cylinder (item 2) for damage or excessive
wear. Be sure the brake release port in the brake cylin-
der is open and free of contamination.
2. Place each friction disc on a flat surface and check
for distortion with a straight edge. Friction material should
appear even across entire surface with groove pattern
visible. Replace friction disc if splines are worn to a point,
disc is distorted, friction material is worn unevenly, groove
pattern is worn away or friction material is burned. Place
each steel disc on a flat surface and check for distor-
tion with a straight edge. Check surface for signs of mate-
rial transfer or heat. Replace steel disc if splines are
worn to a point, disc is distorted or heat discolored.
16
Assembly
1. Insert two bearings with a spacer between them into
a planet gear. Place a thrust race on each side of the
gear and position this assembly in the planet carrier.
Slide the planet gear shaft through the carrier and gear
assembly, aligning the pin hole in the shaft with the hole
in the carrier.
2. Drive a NEW rollpin into place.
Always use NEW
rollpins.
When properly positioned, 50% of the rollpin
length should be engaged in the planet gear shaft with
the remaining 50% in the carrier.
3. With a center punch, stake the carrier next to the pin
hole. This will distort the hole in the carrier so the rollpin
will not back out when in service. Repeat steps 1 through
3 for each of the other two gears.
DO NOT CLEAN BRAKE FRICTION DISCS
IN SOLVENT. SOLVENT MAY CAUSE
DAMAGE TO FRICTION MATERIAL WHICH
MAY RESULT IN BRAKE FAILURE AND
LOSS OF LOAD CONTROL.