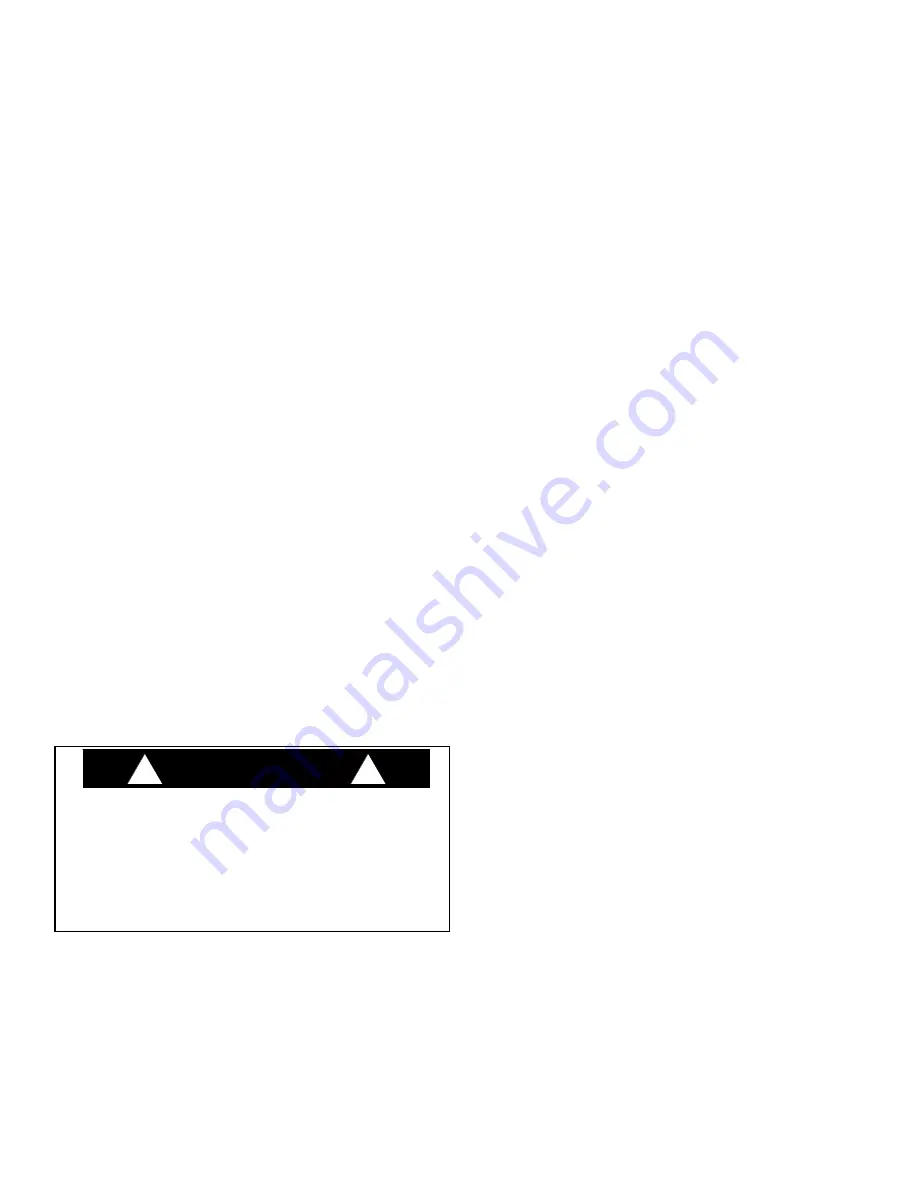
6
THE CABLE ANCHORS ALONE ON HOISTS ARE NOT
DESIGNED TO HOLD RATED LOADS.
Winch loads
applied directly to the wire rope anchor may cause the
wire rope to pull free and result in the sudden loss of load
control and cause property damage, personal injury or
death. A minimum of 3 wraps of wire rope must be left on
the drum barrel to achieve rated load.
INSTALLATION
GENERAL REQUIREMENTS
1. The hoist should be mounted with the centerline of the drum in
a horizontal position. The mounting plane can be rotated to any
position around this centerline.
2. When mounting the hoist, use at least grade five bolts and nuts,
and use both mounting holes in each end gate.
3. It is important that the hoist be mounted on a surface that will not
flex when the hoist is in use, since this could bind the working
parts of the hoist. Also, be sure the hoist is mounted on a flat sur-
face. If necessary, use shim stock to insure proper mounting.
The mounting surface should be flat or -.020 inches.
4. Hydraulic lines and components that operate the hoist should be
of sufficient size to assure minimum back pressure at the hoist.
The motor manufacturer recommends that the back pressure
not exceed 100 psi for maximum motor seal life. 150 psi is the
maximum allowable back pressure. The standard CH150A,
CH175A, CH185A, CH230A, C2H150A, C2H175A, C2H185A
and C2H230A hoists are supplied with the motor internally
drained. If high back pressures are encountered, the motor can
be drained directly to tank to improve motor seal life. To insure
adequate static brake load holding ability, back pressure on the
hoist should not exceed 200 psi. For pressures exceeding 200
psi, consult Braden Engineering.
5. Make certain that the hoist drum is centered behind the first
sheave and the fleet angle does not exceed 1 ½ degrees. The
hoist should also be mounted perpendicular to an imaginary line
from the center of the drum to the first sheave to insure even
spooling.
6. The hoist directional control valve must be a three-position, four-
way valve with a motor spool such that when the valve is in the
center position both work ports are opened directly to tank.
7. The hydraulic oil filter should have a 10 micron nominal rating
and be a full-flow type.
8. High quality hydraulic oil is essential for satisfactory performance
and long hydraulic system component life.
Oil having 150 to 330 SUS viscosity at 100°F (38°C) and vis-
cosity index of 100 or greater will give good results under normal
temperature conditions. The use of an oil having a high viscosi-
ty index will minimize cold-start trouble and reduce the length of
warm-up periods. Ahigh viscosity index will minimize changes in
viscosity with corresponding changes in temperature.
Maximum cold weather start-up viscosity should not exceed
5000 SUS with a pour point at least 20°F lower than the mini-
mum temperature.
Under continuous operating conditions the temperature of the oil
at any point in the system must not exceed 180°. 120-140°F is
generally considered optimum.
In general terms; for continuous operation at ambient tempera-
tures between 50 and 110°F, use SAE 20W; for continuous
operation between 10 and 90°F, use SAE 10W; for applications
colder than 10°F, contact the BRADEN Service Department.
The use of multi-viscosity oils is generally not recom-
mended.
CAUTION
WARNING
!
!
WIRE ROPE INSTALLATION
The wedge and anchor pocket must be clean and dry. The
end of the wire rope being anchored to the drum must be
clean and dry and not frayed. Anything on the end of the
wire rope to keep it from fraying (i.e. tape or wire) must not
be in contact with the wedge when the installation is com-
plete. Consult the wire rope manufacturer on the proper
treatment of the dead end of the wire rope. Some rope
manufacturers recommend when using rotation resistant
wire rope, that the rope end be seized, welded or brazed
before inserting the wire rope into the wedge socket to pre-
vent core slippage or loss of rope lay.
Take the free end of the wire rope and insert it through the
small opening on the cable drum. Loop the wire rope and
push the free end about 3/4 of the way back through the
pocket. Install the wedge as shown in figure 7, then pull the
slack out of the wire rope. The “dead” end of the rope
needs to extend slightly beyond the end of the wedge as
shown in figure 8.
Using a hammer and brass drift, drive the wedge as deep
into the pocket as possible to ensure it is fully seated and
no further movement is detected. Applying a load on the
wire rope will also help seat the wedge in the pocket.
Check to ensure the wedge does not protrude from either
end of the pocket, causing it to interfere with proper spool-
ing of wire rope onto the drum (see figures 9 & 10). If there
is interference or the wedge does not seat firmly, contact
the Braden Product Support Department at 918-251-8511
to determine the proper wedge size.
Summary of Contents for C2H150A
Page 2: ...test...
Page 42: ...test...
Page 43: ...test...
Page 44: ...Copyright 2005 PACCAR Winch Division All rights reserved...