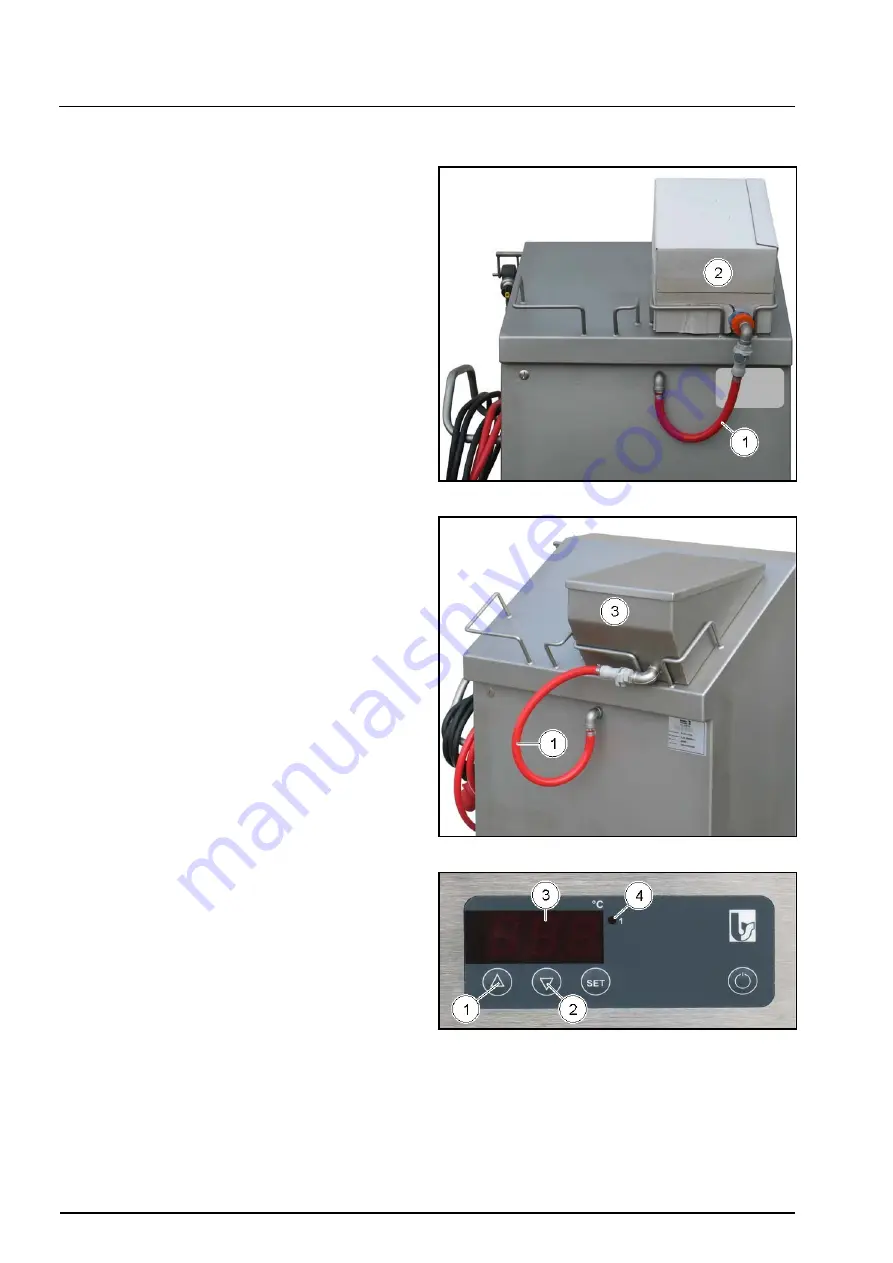
8
Description of the implement
Jelly power pack Edition 09.09
3.2
Functional description
A pneumatically driven, diaphragm controlled agent-
feed-pump sucks the cold jelly via the suction-hose
(1) out off the one-way jelly container (Bag in Box
(BIB)) (2) or the jelly container (3) (special
equipment).
Then the sucked off jelly is delivered via the agent-
feed-pump to the flow-heater. Inside the flow-heater
the jelly is heated to the set processing temperature.
The processing temperature can be set via UP- and
DOWN-keys (1 and 2) between
25.0 and 93.0°C
.
The temperature display (3) shows the actual
system-temperature
in
Degree
Celsius.
The
implement is ready for use when the red
temperature-control light (4) has gone out.
Summary of Contents for Jelly power pack
Page 38: ...38 Circuit diagrams Jelly power pack Edition 09 09 7 Circuit diagrams...
Page 39: ...Circuit diagrams 39 Jelly power pack Edition 09 09...
Page 40: ...40 Circuit diagrams Jelly power pack Edition 09 09...
Page 41: ...Circuit diagrams 41 Jelly power pack Edition 09 09...
Page 42: ...42 Circuit diagrams Jelly power pack Edition 09 09...