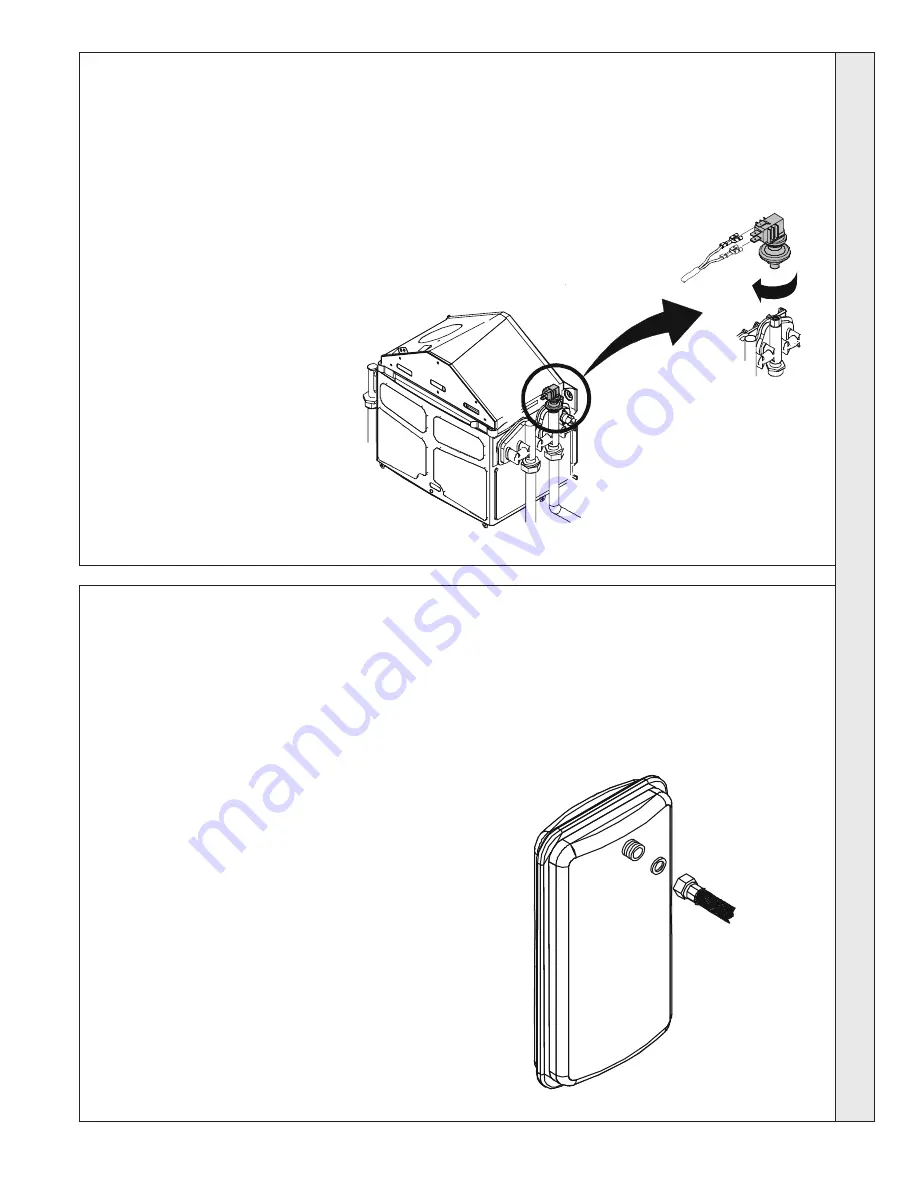
43
BOXER
combination boiler -
Installation and Servicing
SERVICING
68 LOW WATER SWITCH REPLACEMENT
1.
Refer to Frame 49.
2.
Remove the casing. Refer to Frame 41.
3.
Drain the boiler. Refer to Frame 44.
4.
Disconnect the electrical lead from the low
water switch.
5.
Unscrew the low water switch nut and
remove the switch.
6.
Fit the new
low water switch
and re-
assemble in reverse order, using a suitable
sealant material.
7.
Refill the boiler. Refer to Frames 4 and 28.
5
4
69 EXPANSION VESSEL REPLACEMENT
1.
Refer to Frame 49.
2.
Remove the casing. Refer to Frame 41.
3.
Drain the boiler. Refer to Frame 44.
4.
Undo the union nut on the vessel water flexible connection
pipe.
5.
Remove the expansion vessel.
Refer to Frame 43.
6.
Fit the new expansion vessel using the new sealing
washer provided.
7.
Re-assemble in reverse order.
8.
Refill the boiler. Refer to Frames 4 and 28.
4
Note.
If preferred, and for convenience, a new expansion vessel
may be installed on the return pipework elsewhere in the
heating system providing it ensures equivalent system
protection.
SER
VICING
All manuals and user guides at all-guides.com