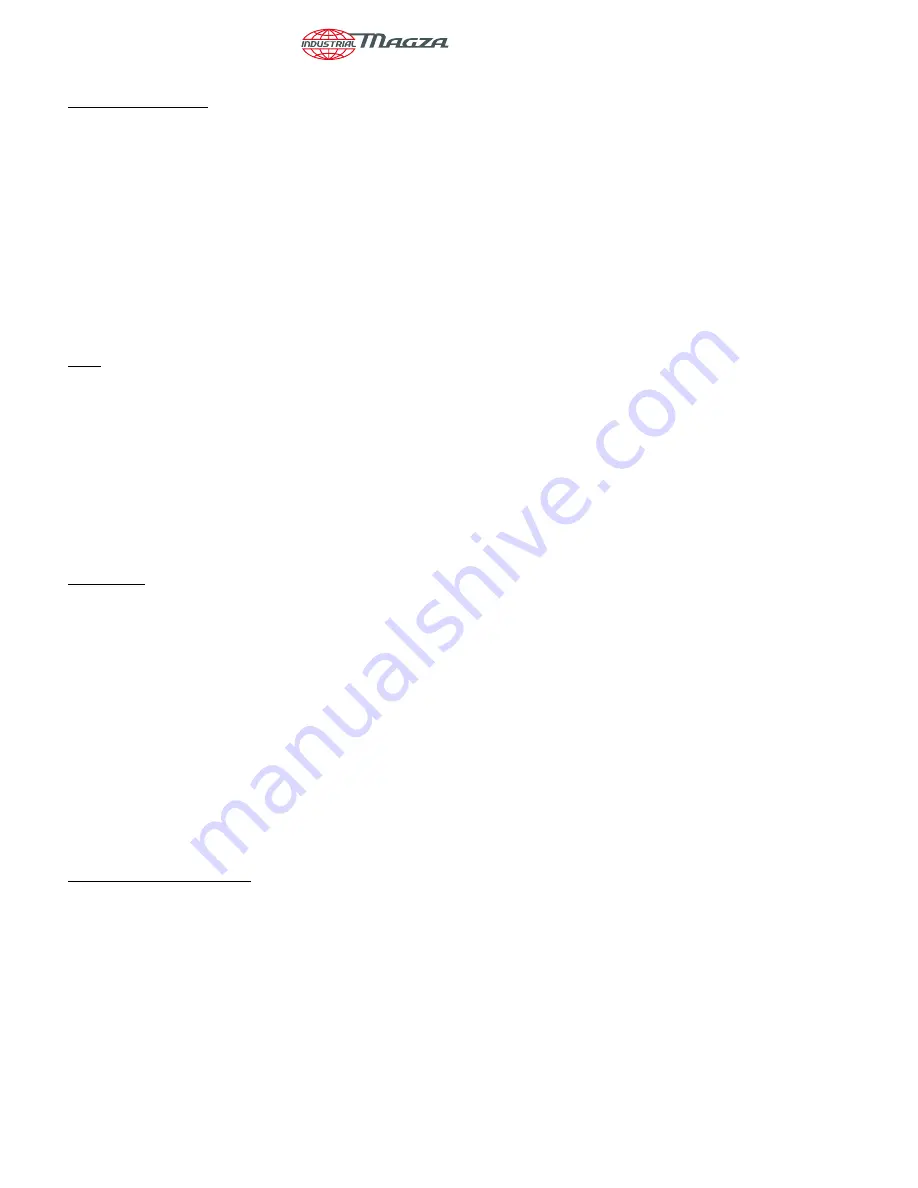
RBS2C-A
16
SPEED CONTROL
Motor speed is directly proportional to the setting of the MOTOR SPEED potentiometer or the magnitude of
an external speed reference signal, as applicable. This potentiometer or the speed reference signal may be adjusted
while the motor is running or may be preset before the motor is started.
The rates of acceleration and deceleration are preset by the ACCEL and DECEL potentiometers, respec-
tively, located on the controller control board.
Maximum speed and minimum speed (or offset) are preset by the MAX SPD and MIN SPD potentiometers,
respectively, located on the control board.
JOG
If a RUN-STOP-JOG switch is used, place the switch in JOG position. Otherwise initiate a Jog command.
Jog is momentary, causing motor rotation only while the switch is held in JOG position or while a Jog command is
active. Release the switch to stop the motor.
Normally, jog speed is directly proportional to the setting of the MOTOR SPEED potentiometer. If a separate
JOG SPEED potentiometer is used, jog speed will be directly proportional to the setting of the JOG SPEED poten-
tiometer.
REVERSE
To reverse motor rotation on controllers with reversing capabilities, initiate a Stop function and then initiate
a reversing command. The motor will then accelerate to the setting of the MOTOR SPEED potentiometer or exter-
nal speed reference signal, as applicable. Forward and reverse speed ranges are identical.
If a FWD-REV switch is used, it must have a center position interlock, which requires a momentary relax-
ation of pressure before the opposite position can be engaged. The center position causes a Stop command and
allows time for the motor to stop before a Reverse command is initiated. If a Reverse command is initiated while
the motor is rotating, motor and controller damage may occur.
Model RBS2CM Controllers have an antiplug feature which prevents reversing the motor before the motor
has stopped.
INOPERATIVE MOTOR
If the motor stops and/or won’t start, turn-off the AC supply to the controller and check the AC line fuse on
the controller control board. For the location of the fuse, see Figure 22, page 37. If the fuse is blown, refer to the
Troubleshooting Table (Table 5).
If the fuse is not blown, the internal overload monitor may have shut down the controller. The overload mon-
itor will shut down the controller if the motor armature current exceeds 120% of rated for a length of time of con-
tinuous operation. The length of time is determined by the amount of the overload. If the overload monitor trips,
reset the controller by initiating a Stop command, removing the overload, and then initiating a Run command to
restart. Repeated shutdown indicates an overload condition (mechanical or electrical) which must be removed.
Refer to the Troubleshooting Table (Table 5).
®
DIST. AUTORIZADO
MEX (55) 53 63 23 31
QRO (442) 1 95 72 60
MTY (81) 83 54 10 18
[email protected]