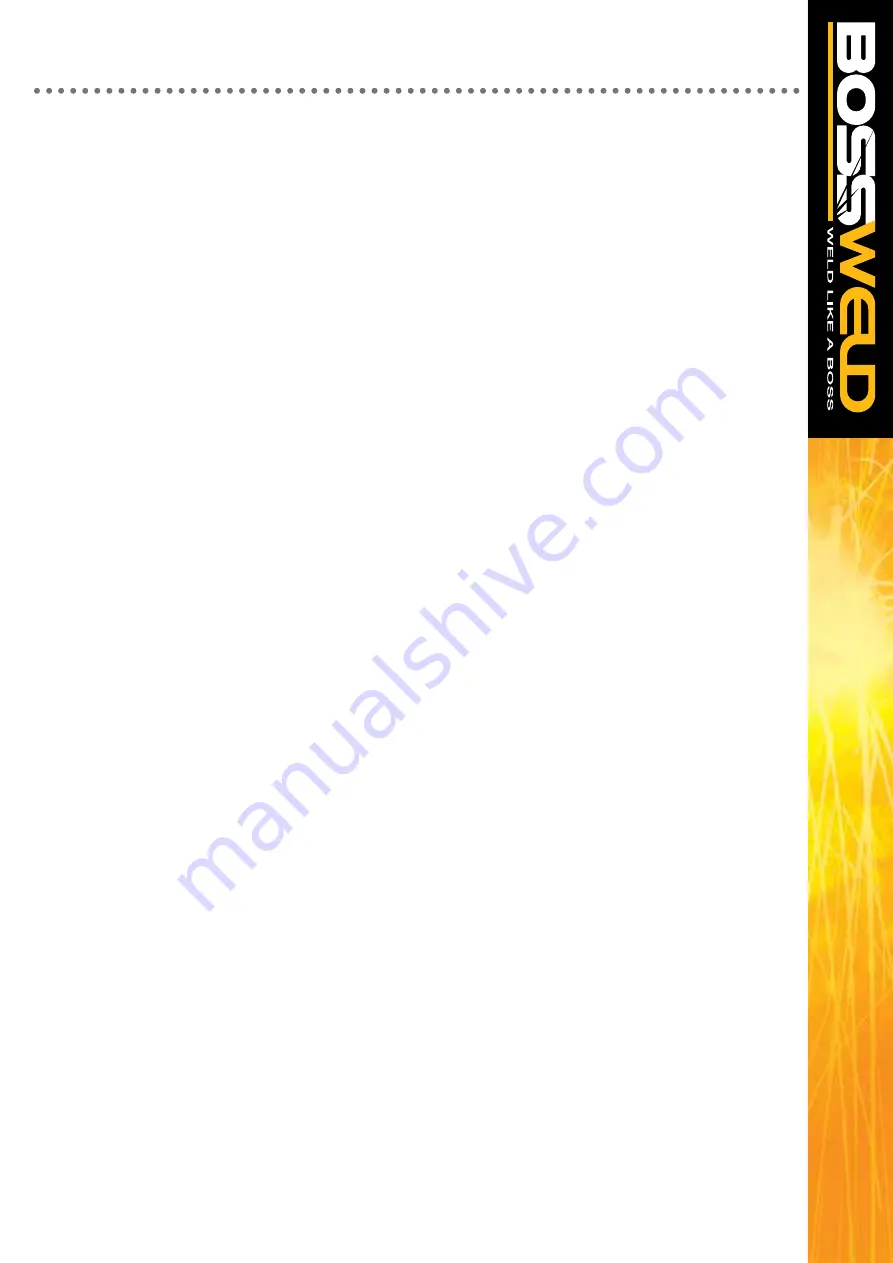
13
AC / DC WELDING
Alternating current (AC) is electricity that switches direction back and forth so the voltage also periodically
reverses because the current changes direction. Typical AC currents are what you would expect to see from
your electrical outlets in your home and often used in higher voltage devices such as household appliances.
AC current changes its polarity 120 times per second with a 60-hertz current. Reversed polarity (AC) results
in deeper penetration.
In Alternate Current (AC) welding, since the current and the magnetic field of the arc reverse direction many
times a second, there is no net deflection of the arc.
Applications of AC Welding
AC welding can be used to weld magnetic metals. This cannot be done with DC welding. AC welding is ideal
for the following types of welds:
• Downhand heavy plate
• Fast fill
• Aluminum TIG welding with high frequency
The primary advantage of using AC welding is that it allows the weld operator to weld on magnetized
materials. In AC current, the current changes direction and is not affected by magnetism. The arc remains
stable and is easier to control.
AC welding is also the preferred method for:
• TIG welding aluminum, because the current supports welding at a higher temperature.
• Making repairs on machinery because the machinery usually has a magnetized field and is older and may
have rusty areas where there is concern about the higher heat penetration that can occur with DC welding.
• Seam welding in shipbuilding because the current settings can often be higher than those used in DC
welding and a deeper penetration of plate metals can be obtained.
The biggest drawback to using AC welding is the quality of the weld. It is not as smooth as DC welding
because of the continuous change in directional flow and there is likely to be more spatter.
Applications of DC Welding
Welding with DC is best used for:
• Hard facing
• Overhead or vertical welding
• Single carbon brazing
• Build-up of heavy deposits
• Stainless steel TIG welding
• Cutting tap
As a rule of thumb, DC is preferred for welding because:
It produces a smoother weld and there is less spatter because of the constant linear direction of the current.
It maintains a constant and stable arc and is thus is easier to handle and more reliable than AC current.
Machinery that uses DC current is generally cheaper and easier to use.
It welds thinner metals better than AC current.
Overall Strength of Welds
Overall the strength of the weld can be determined by many factors, such as:
• Proper electrode, welding apparatus and procedures;
• Properties of the materials being welded-magnetic vs. non-magnetic;
• Proper edge preparation-the cleaner the edge, the better the weld;
• Current settings – DC vs. AC;
• Speed of travel – the angle of the electrode needs to be maintained throughout the length of the joint as it is
being welded.
A strong weld can be achieved in both AC welding and DC welding so long as you weld with the current and
polarity appropriate for the material being welded. One doesn’t necessarily, always and everywhere, produce
a better weld than the other. It’s a matter of choosing the right one for your job.