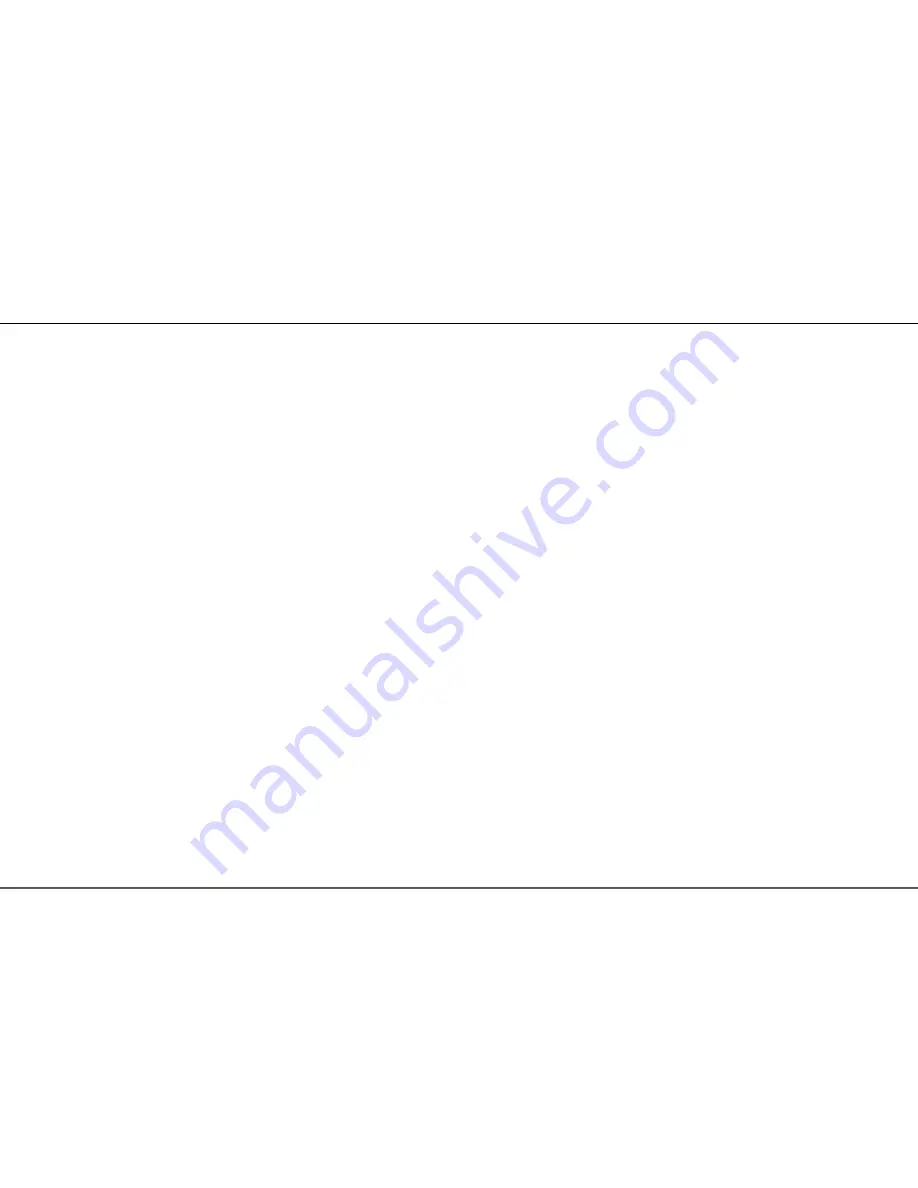
Repair Instructions Laundry - Repair Instruction;T22 - Table of content
2013-10-23 / DIS 113_58300000133444_ara_en_l
Repair Instructions Laundry Repair Instruction;T22
Page 1 of 35
1 Concerning this document
2
1.1
Purpose and target group..................................................... 2
1.2
Other applicable documents..................................................2
2 Safety
3
2.1
Qualification........................................................................... 3
2.2
Information in warnings......................................................... 3
2.3
Basic safety instructions........................................................4
2.4
Basic warning instructions.....................................................5
3 Design and function
7
3.1
Fascia.....................................................................................7
3.2
Conductivity measurement.................................................... 8
3.3
Condensate water container..................................................9
3.4
Temperature control with fan (cooling air)........................... 10
3.5
Heat pump circuit................................................................ 11
3.6
Automatic cleaning function.................................................12
4 Fault diagnosis
13
4.1
Malfunctions.........................................................................13
4.2
Result faults.........................................................................14
4.3
Leaks....................................................................................15
4.4
Odours................................................................................. 16
5 Test
17
5.1
Starting / ending demo programme.....................................17
5.2
Checking electrodes for measuring conductance................18
5.3
Checking interior light..........................................................19
5.4
Read out fault memory........................................................20
6 Repairs
21
6.1
Cleaning the heat pump...................................................... 21
6.2
Installing conversion kit 743988.......................................... 22
6.3
Replacing motor...................................................................23
6.4
Replacing left / right side panel........................................... 24
6.5
Replacing rollers..................................................................26
6.6
Removing / installing the cooling-air panel..........................27
6.7
Opening / closing refrigeration circuit.................................. 28
6.8
Replacing compressor.........................................................29
6.9
Replacing fluff filter..............................................................30
6.10
Removing / installing front panel......................................... 32
6.11
Cleaning the condenser.......................................................33
6.12
Removing / installing drum bearing..................................... 34
6.13
Transporting the appliance.................................................. 35