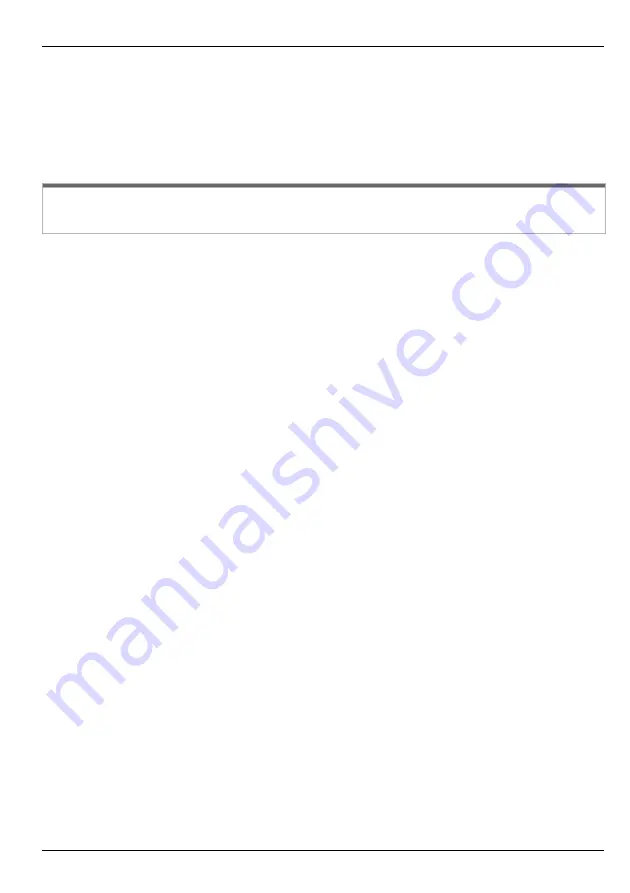
25
Warranty details
Pilot Ignition – 6 720 886 398 (2021/02)
•
as a result of repairs, alterations or modifications to the Product which have been performed by a person who is not suitably
qualified and experienced to perform works on the Product; or
•
from the use of any spare parts not manufactured, sold or approved by Bosch in connection with the repair or replacement of
Product.
This voluntary warranty does not apply to damage that has been caused by continued use of a Product after it is known, or would
have been known with regular servicing, it is defective.
Wrong Deliveries and Transit Damage
Wrong deliveries, incorrect or damaged packing and transit damage claims are not warranty claims. Such cases should be directed
to Bosch's Customer Service line in Australia on ph: 1300 307 037 or in New Zealand on ph: 0800 543 352.
How to Make a Warranty Claim
If a Product fails within the warranty period, the end user must stop using the Product and make a claim as soon as possible, in any
event before the end of the Warranty Period (see Deadlines for Submitting Warranty Claims below).
To make a warranty claim under this voluntary warranty, call the Bosch Customer Contact Centre (in Australia on ph: 1300 307 037
or in New Zealand on ph: 0800 543 352). Please be ready to provide the model and serial number, date of installation, purchase
details and a full description of the problem. Alternatively, for claims in Australia, you can post details of your claim to Robert Bosch
(Aust) Pty Ltd, Attn TT Warranty Department, Locked Bag 66, Clayton Sth, Victoria, 3169. Claims received by post will take longer
to process and we encourage you to call. Bosch may refer you to one of its Bosch Warranty Authorised Service Dealers.
Proof of purchase and purchase date, as well as proof of installation and proper commissioning by a licensed installer, may be
required by Bosch or an authorised service technician.
All warranty service calls will be conducted by an authorised service technician during normal business hours. Bosch will not accept
claims under this voluntary warranty for attendance and repair of the Product by third parties not authorised by Bosch.
Deadlines for Submitting Warranty Claims
Bosch aims to rectify genuine quality problems as a priority. This is generally achieved by investigating why defective products have
failed and by introducing immediate corrective action measures to prevent re-occurring warranty failures. It is therefore critical that
all warranty claims are promptly submitted to Bosch as soon as the product fails, and in any event before the end of the warranty
period.
Product Liability and Product Safety
Bosch should be informed immediately about any potential product safety concerns within and outside the warranty period. Bosch
is well aware of its product liability and product safety obligations and responsibilities. It is our aim to ensure appropriate product
safety standards are met in order to avoid injury, loss and damage caused by defects in any Product.
Privacy
Bosch is required to seek personal information from an end user who seeks to make a claim under this warranty.
Such personal information may be used by Bosch and/or any authorised service technician (who is authorised to process warranty
claims and/or carry out warranty repairs on behalf of Bosch) for the purpose of processing such warranty claim and also for the
provision of customer support and further information about Bosch’s products and services (Purpose).
If an end user does not wish to provide Bosch and/or its authorised service technician with personal information, Bosch may be
unable to process the end user’s warranty claim or to provide the end user with additional customer support, services and
information.
Failure to service Product in accordance with recommendations in instruction manuals for Product may result in a warranty claim
under this voluntary warranty being rejected by Bosch. Bosch alerts end users that instruction manuals for Product contain
specific recommendations for servicing and safety checks to be carried out on Product.
Table 15
Summary of Contents for TF250
Page 27: ...27 Pilot Ignition 6 720 886 398 2021 02 Notes ...
Page 28: ......