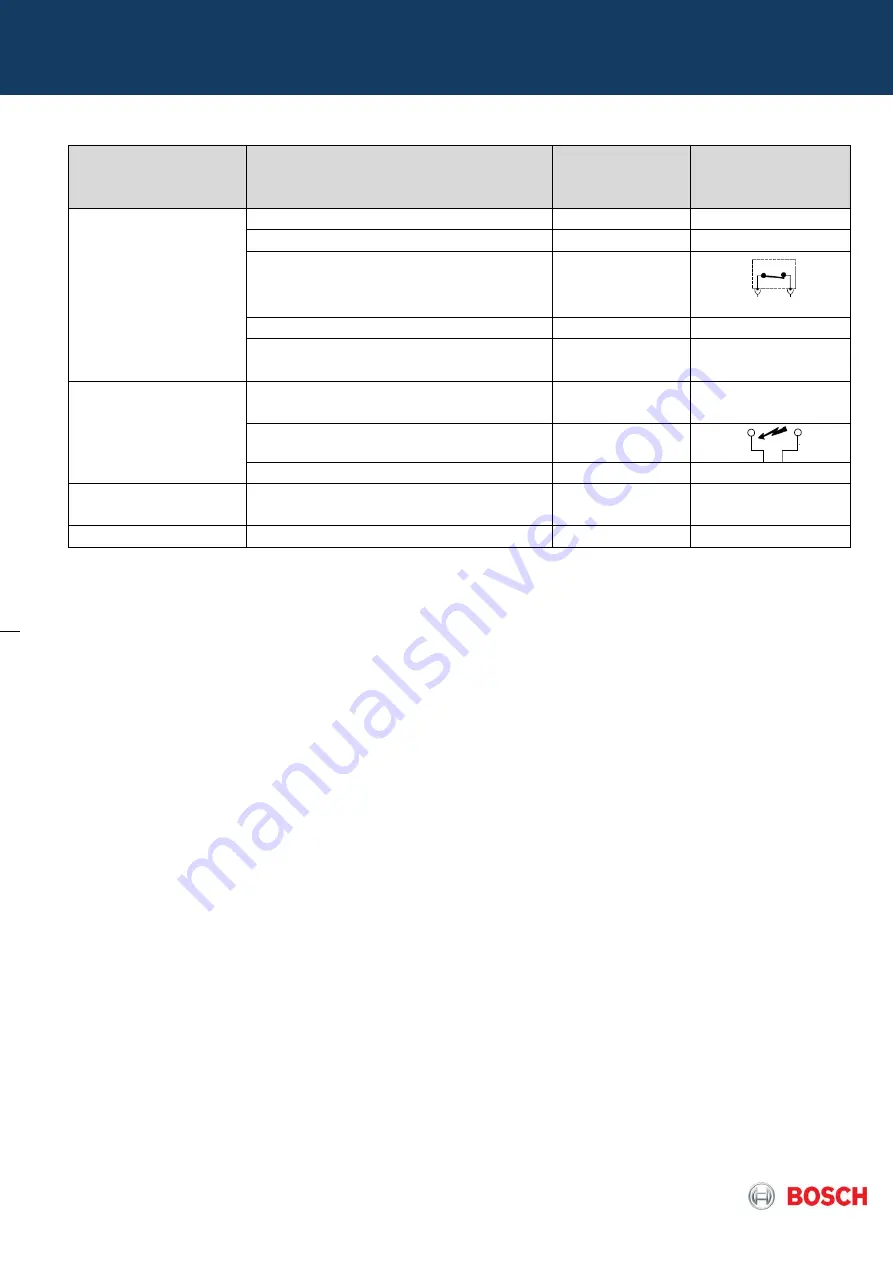
Page 23 from 45
6 720 887 546 “SM FP_ErP LPP-MPP Europe 2018/05 en”
Operation
Action
Connection to
the control
unit
Result
Standby
(Inputs Signals
must be within
expected limits)
Main Switch in control unit
Input
ON
Electrical plug connected
Input
230 V
AC
Thermostat (temperature limiter)
and Thermal fuse with continuity
Input
Contact closed
Ionization reading
Input
0 µA
Temperature sensors OK
Input
Ohm Value inside
range
Hot Water Demand
(tap opening)
Turbine detects water flow
Input
Frequency value
to control unit
Spark to ignition electrodes
Output
Gas valve solenoid activation
Output
V
DC
Flame on main
burner
Ionization detection (spark stops)
Input
I > 8 µA
Hot Water Delivery
Safety devices monitor operation
Input
Table 9 – Operation conditions
Power reduction in case of high temperature risk
A control strategy was implemented in the fix power version (manual selection of segments to
increase power) to avoid overheating of the water when a high power is selected on the power
selector and low water flow is running through. To avoid scalding hazard,
the water heater perform as follows:
-
If the power selector is in level 2 or 3 and the outlet temperature is expected to be
higher than 70ºC, the control unit must automatically decrease the power level. “E1”
warning code must be shown blinking with a frequency of 2Hz, so the user is aware
that the water heater has automatically decreased power;
-
After this, even if the water flow is increased, the water heater shall not increase
power again.
-
The reset of the warning will only be possible by closing of the water tap;
-
If the outlet temperature is higher than 70ºC for more than 20 seconds or if a
temperature higher than 85ºC is achieved (either for level 1, 2 or 3), the water heater
is expected to lockout with “E1” error. If “E1” error has occurred, manual reset is
needed to resolve it
Power reduction at start-up (specific for 11L)
A control strategy was implemented to avoid overheating of the water when a high power is
selected on the power selector and low water flow is running through at start-up. To avoid
scalding hazard, the water heater must perform as follows:
-
If the power selector is in level 3 and the water flow at start-up is lower than 4 l/min,
the control unit must automatically decrease the power level to level 2.