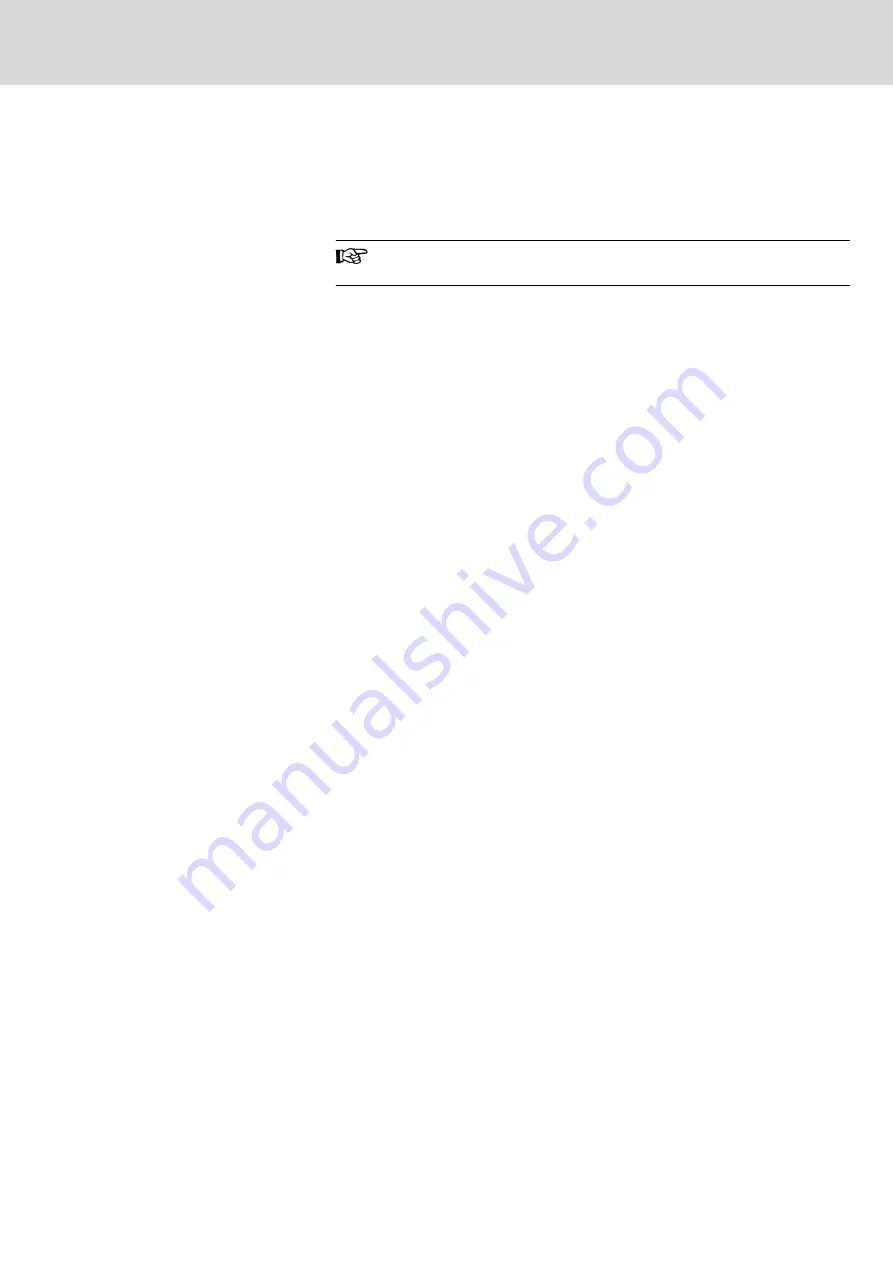
also refer to Rexroth IndraDrive Drive System DOK-INDRV*-SYSTEM*****-
PRxx-EN-P, Chapter "Project Planning of Control Voltage ")
The voltage supply of the holding brake has to be designed so as to make a
voltage of 24 V ±10% available on the motor for safe operation of the holding
brake (releasing/applying).
The voltage incoming at the motor is subject to the line length and
the cable properties, e.g., conductor resistance.
If a fault occurs during operation, causing a voltage deviation, this fault must
be detected and eliminated immediately. The failure can be identified, for ex‐
ample, using a monitoring device for undervoltage.
Event of fault
Only in an event of fault, i.e. in the case of a fault in the system, may the
brake be activated when the motor is turning, e.g. in order to prevent a dan‐
gerous lowering of vertical axes. In this case, sparks may be generated in the
brake and increased temperatures may occur within the motor. When a fault
occurs, the operator must eliminate it immediately.
Function Test
Before commissioning and, during operation, at periodic intervals (e.g. every
8 hours), the function of the brake is to be checked in the framework of an
appropriate brake test. Through the application of a defined motor torque, the
brake is tested for slippage. In case of certain drive control devices, it is pos‐
sible to carry out an integrated brake test using the Brake Monitor command.
Further information can be found in the respective firmware operation manual
for the drive control device.
1.6
Residual risks
Overloading
When the motor is overloaded, including cases where errors in the mechani‐
cal or electrical equipment of the machine cause such overloading, high tem‐
peratures may occur that result in explosion hazards.
An operation in explosive dust-atmosphere can built a layer on the motor dur‐
ing a residence time, which does no longer ensure a sufficient motor cooling
chapter 1.13.2 "Repair" on page 26
Grounding and discharge currents
Variable-speed drive systems cause unavoidable discharge currents. If the
grounding connector in the motor cable and the second separate grounding
connector on the motor housing are not connected as specified or are inter‐
rupted due to corrosion or other defects during their lifetime, the discharge
current flows as leakage current over conducting housing parts, resulting in
the risks of sparking at transfer points and, if explosive materials are present,
explosions.
Material aging
The time of action and penetration of explosive materials depend on the ap‐
plication. It depends on the ageing degree of the seals, on the mechanical at‐
tachment of the motor, the properties of the explosive materials and the aver‐
age temperature occurring during the operating time as a result of the load
cycles.
Impermeability
Due to unavoidable temperature fluctuations as well as due to the deteriora‐
tion of gaskets, the housing is not leak proof. Hence, explosive gases that oc‐
cur within the equipment during a fault can penetrate into the motor. The de‐
sign and checking of the impermeability are carried out according to the de‐
gree of protection IP 65 (EN 60034-5:2001). The maximum temperature of
parts within the motor can reach 155 °C during normal operation at maximum
ambient temperature.
DOK-MOTOR*-MSK*EXGIIK3-IT04-EN-P
Bosch Rexroth AG
17/37
MSK Motors Operation in Potentially Explosive Areas ATEX Directive 2014/34/EU
Instructions