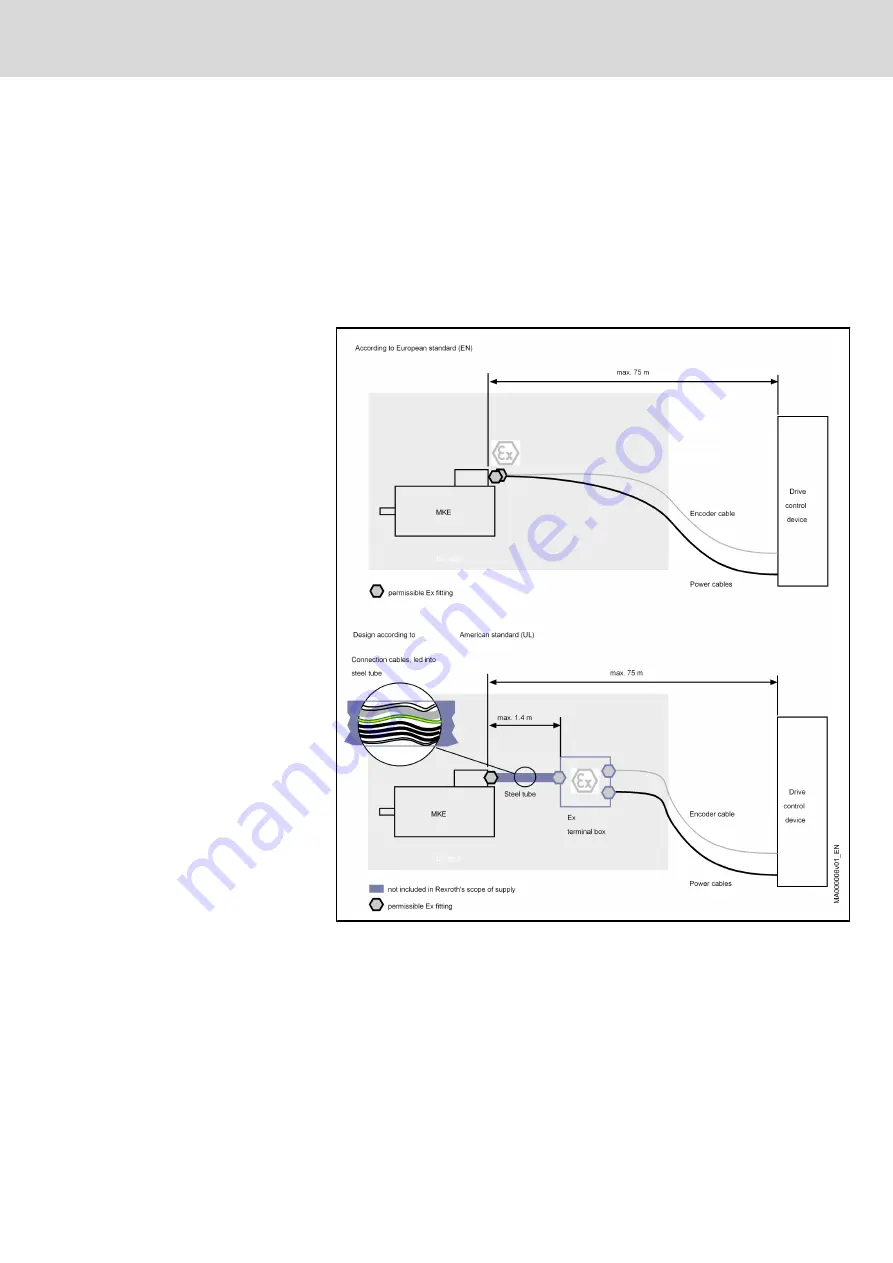
8
Connection Technique
8.1
Variants
MKE motors are available in:
●
Housing type E (according to European standard EN)
●
Housing type U (according to American Standard UL)
The different regulations of the responsible public authority require the con‐
nection variants shown below.
Fig.8-1:
Connection variants MKE motors
Thermostat connection
If MKE motors are used in potentially explosive areas, the analysis of the motor
temperature has to be done at Rexroth by means of the drive control device
●
IndraDrive
●
DuraDrive
●
EcoDrive
●
DIAX04
offered by Rexroth.
Project Planning Manual | Rexroth MKE Synchronous Motors
Electric Drives
and Controls
| Bosch Rexroth AG
65/131
Connection Technique