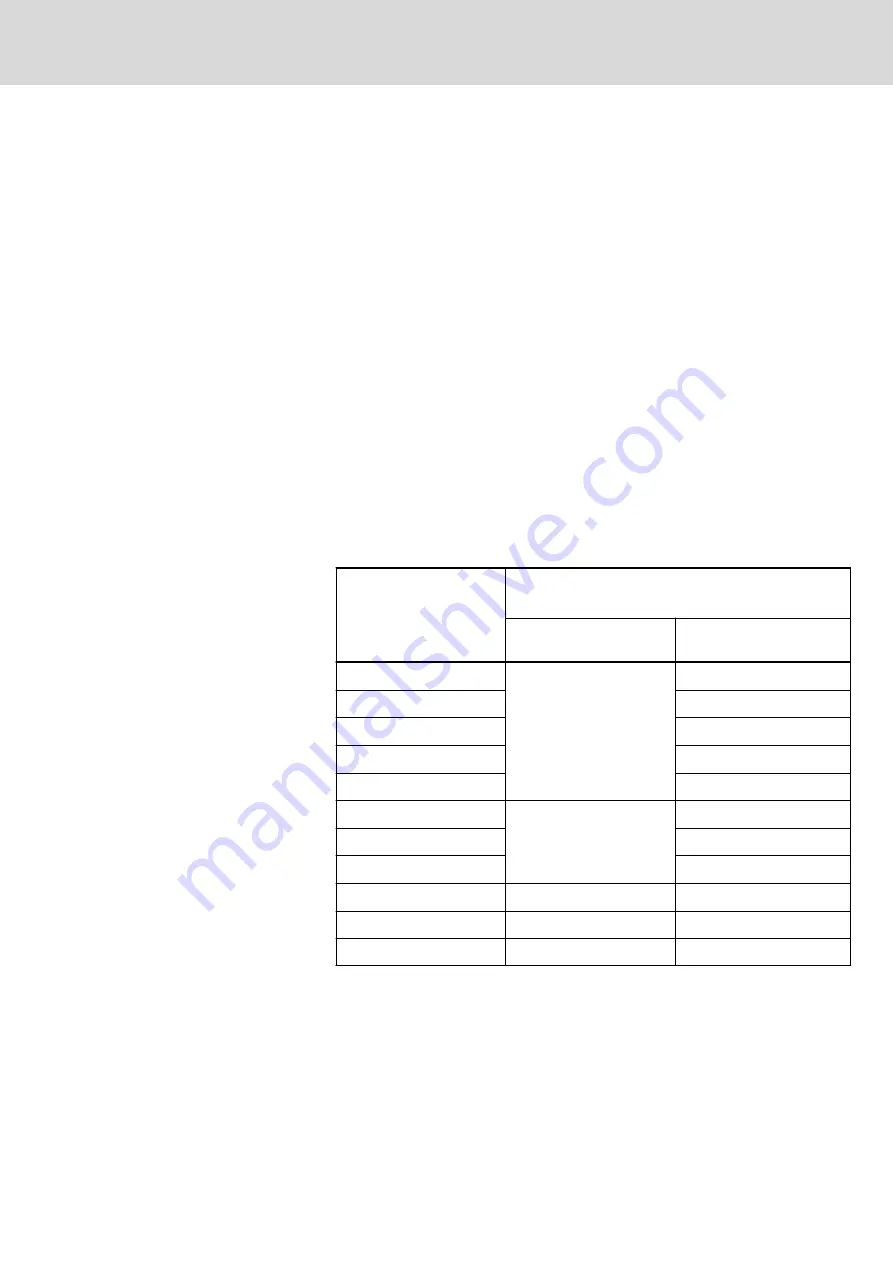
●
Do not remove or plug in connectors when the component has been
powered.
●
Under specific conditions, electric drive systems can be operated at
mains protected by residual-current-operated circuit-breakers sensitive
to universal current (RCDs/RCMs).
●
Secure built-in devices from penetrating foreign objects and water, as
well as from direct contact, by providing an external housing, for exam‐
ple a control cabinet.
High housing voltage and high leakage current! Danger to life, risk of injury
by electric shock!
●
Before switching on and before commissioning, ground or connect the
components of the electric drive and control system to the equipment
grounding conductor at the grounding points.
●
Connect the equipment grounding conductor of the components of the
electric drive and control system permanently to the main power supply
at all times. The leakage current is greater than 3.5 mA.
●
Establish an equipment grounding connection with a minimum cross
section according to the table below. With an outer conductor cross sec‐
tion smaller than 10 mm
2
(8 AWG), the alternative connection of two
equipment grounding conductors is allowed, each having the same
cross section as the outer conductors.
Cross section outer con‐
ductor
Minimum cross section equipment grounding conductor
Leakage current ≥ 3.5 mA
1 equipment grounding
conductor
2 equipment grounding
conductors
1.5 mm
2
(16 AWG)
10 mm
2
(8 AWG)
2 × 1.5 mm
2
(16 AWG)
2.5 mm
2
(14 AWG)
2 × 2.5 mm
2
(14 AWG)
4 mm
2
(12 AWG)
2 × 4 mm
2
(12 AWG)
6 mm
2
(10 AWG)
2 × 6 mm
2
(10 AWG)
10 mm
2
(8 AWG)
-
16 mm
2
(6 AWG)
16 mm
2
(6 AWG)
-
25 mm
2
(4 AWG)
-
35 mm
2
(2 AWG)
-
50 mm
2
(1/0 AWG)
25 mm
2
(4 AWG)
-
70 mm
2
(2/0 AWG)
35 mm
2
(2 AWG)
-
...
...
...
Tab. 3-1:
Minimum cross section of the equipment grounding connection
3.3.2
Protective extra-low voltage as protection against electric shock
Protective extra-low voltage is used to allow connecting devices with basic in‐
sulation to extra-low voltage circuits.
On components of an electric drive and control system provided by Bosch
Rexroth, all connections and terminals with voltages up to 50 volts are PELV
MCL Ironless Linear Motors
15/197
Safety instructions for electric drives and controls
R911330592_Edition 06 Bosch Rexroth AG
Summary of Contents for rexroth MCL
Page 1: ...MCL Ironless Linear Motors Project Planning Manual R911330592 Edition 06 ...
Page 16: ...8 197 MCL Ironless Linear Motors Bosch Rexroth AG R911330592_Edition 06 ...
Page 52: ...44 197 MCL Ironless Linear Motors Bosch Rexroth AG R911330592_Edition 06 ...
Page 57: ...MCL Ironless Linear Motors 49 197 Dimension sheets R911330592_Edition 06 Bosch Rexroth AG ...
Page 68: ...60 197 MCL Ironless Linear Motors Bosch Rexroth AG R911330592_Edition 06 ...
Page 90: ...82 197 MCL Ironless Linear Motors Bosch Rexroth AG R911330592_Edition 06 ...
Page 104: ...96 197 MCL Ironless Linear Motors Bosch Rexroth AG R911330592_Edition 06 ...
Page 162: ...154 197 MCL Ironless Linear Motors Bosch Rexroth AG R911330592_Edition 06 ...
Page 174: ...166 197 MCL Ironless Linear Motors Bosch Rexroth AG R911330592_Edition 06 ...
Page 196: ...188 197 MCL Ironless Linear Motors Bosch Rexroth AG R911330592_Edition 06 ...
Page 198: ...190 197 MCL Ironless Linear Motors Bosch Rexroth AG R911330592_Edition 06 ...
Page 204: ...Notes 196 197 MCL Ironless Linear Motors ...