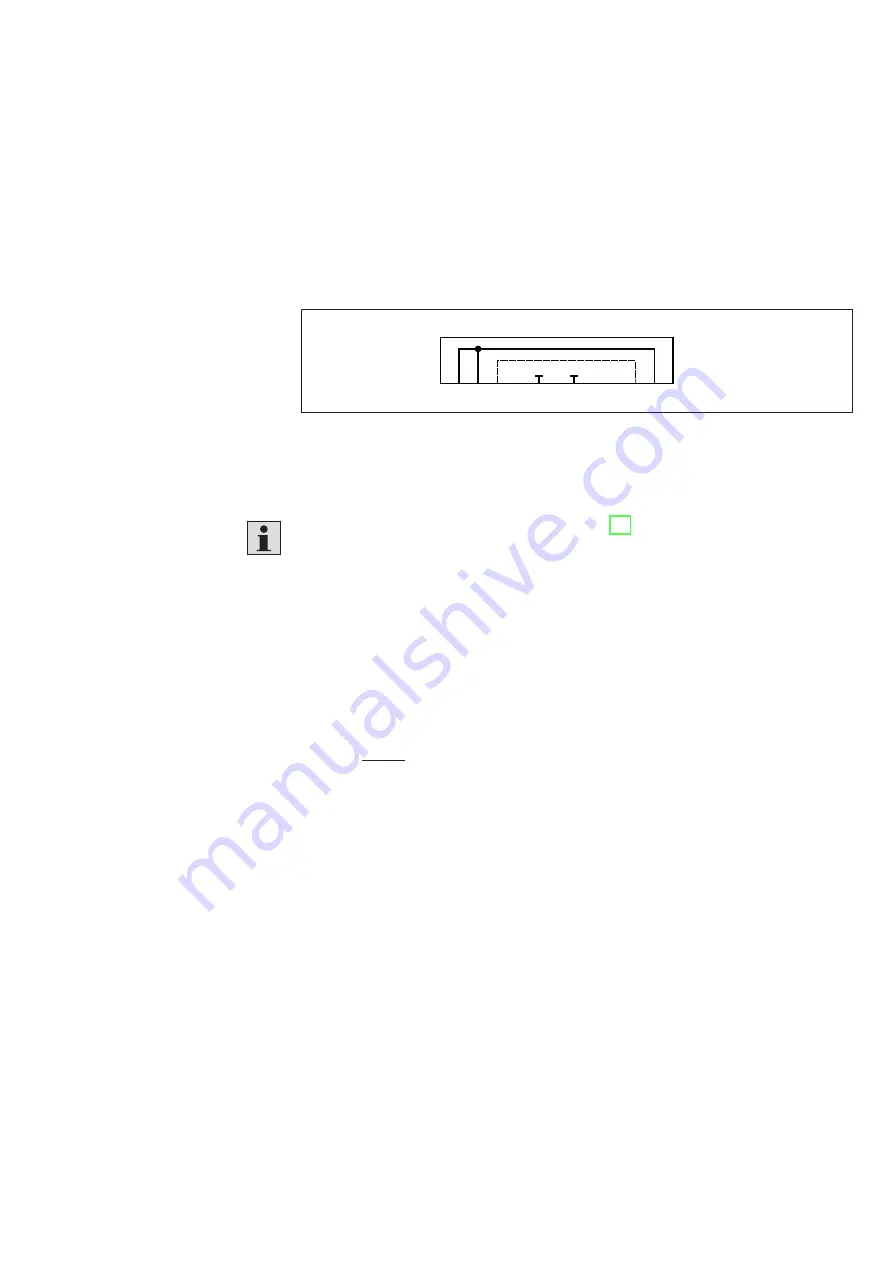
Assembly 25/44
RE29583-XH-B/09.19, 4WS2EM10..5X/...XH...,
Bosch Rexroth AG
Before installing the valve into a device or system, the system must be flushed.
Only then is the unobjectionable functioning of the valve guaranteed. With an external
pilot oil supply make sure that it is flushed, as well. Also observe the operating
instructions of the device and/or system into which the valve is installed.
For flushing the system into which the valve is to be installed, flushing plates with
FKM seals and porting pattern according to ISO 4401-05-05-0-05 are available. Ein For
a dimensional drawing of the flushing plate, see "
Data sheet 29583-XH...
". Within the
flushing plate, ports P, T and T1 as well as X and Y are connected with each other.
Fig. 2: Flushing plate, representation of the inner connections
Install this flushing plate into the system instead of the valve and subsequently flush
it.
When using the subplates mentioned under 7.6 "Required accessories" or in case
of assembly on comparable cast iron installation surfaces, tighten all four valve
mounting screws with a tightening torque of 12.5 Nm ± 1.5 Nm (with a friction
coefficient of µtotal = 0.09...0.14). This tightening torque refers to the maximum
admissible operating pressure.
The use of a directional valve with port in accordance with ISO 4401-05-05-0-05 is
suited better than a flushing plate.
This valve can also be used for flushing the actuator ports.
The following is a guideline for the necessary flushing time t in hours:
t
≥
V
- 5
q
v
V
Tank capacity in liters
q
V
Pump flow in liters / minute
The degree of contamination of the hydraulic fluid that can be monitored by
a continuous measurement using a particle counter is decisive for the flushing time.
Install a pressure differential-resistant pressure filter without bypass, if possible
with integrated clogging indicator, directly in front of the valve. During the flushing
procedure, check all filters in short intervals and exchange the contaminated filter
elements, if necessary.
T P X
A
B
Y T1