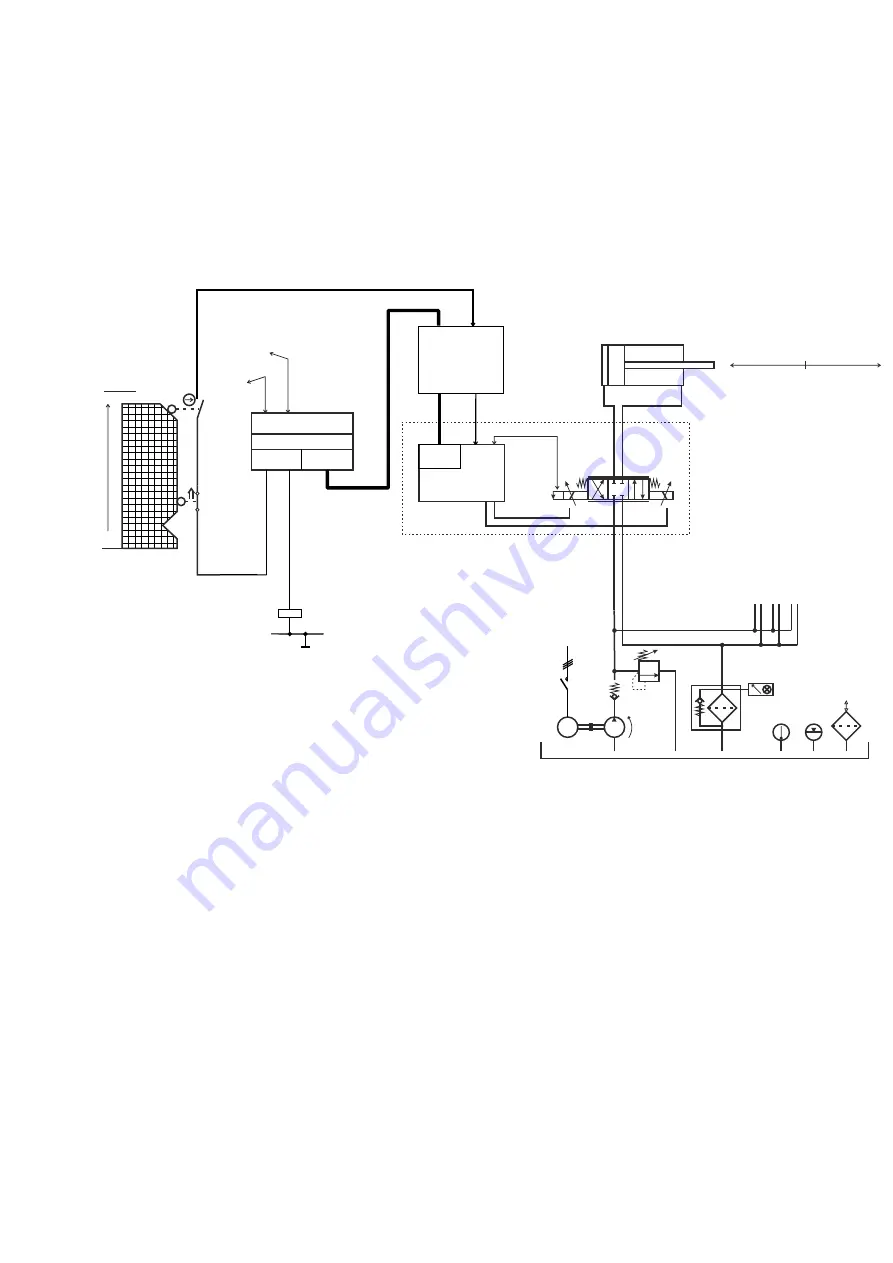
Safety instructions 19/44
RE 29118-B/09.2021; 4WRPEH6_3X, 4WRPEH10_3X, 4WRPE6_3X, 4WRPE10_3X, 4WRLE_4X;
Bosch Rexroth AG
For category 2, the valve with the OBEA-V5 interface must also be tested cyclically
via the PLC with regards to the connection example according to cat. 1. For error
cases, a second switch-off channel must also be implemented. In this example, the
oil supply/hydraulic pump is switched off. In compliance with EN13849-1, cat. 2
requires running testing of valve switch-off by machine control at start-up and in
adequate intervals during running operation.
Fig. 2: Category 2 block diagram
Category 2
M
3~
L
IO-Link terminal
with safe
separation of
power supply
from bus
K3
K2
IO-Link
24 V
1A
Dangerous
movement
High-response valve with
OBEA-V5 electronics and
IO-Link Class B
other actuators
Determination of
position
Control a
Control b
a
b
P
T
A
B
1V3
1S3
OBEA-V5
IO-Link
interface
IOL-Master
Outputs
PLC
Inputs
K1
O1.1
I1.1
I1.2
ÜB1
ÜB2
B1
ÜB1
B2
ÜB2
24 V
Open
Closed
1V2
1Z2
1S1 1S2
1Z1
1V1
1M
1P
O1.2
Q1
2.7.7 Connection example/block diagram for IO-Link valves
For category 1, the supply voltage of valve pin 2 and 5 must be safely switched off.
In this example, this is realized by means of safe limit switches at doors in
connection with a safe IO-Link terminal.
The voltage can also be safely switched off via an IO-Link-Master for safe shut-off of
the B voltage according to 13849-1.
Fig. 1: Category 1 block diagram
Category 1
M
3~
IO-Link
terminal with
safe separation
of power supply
from bus
K3
K2
IO-Link
24 V
1A
Dangerous
movement
High-response valve with
OBEA-V5 electronics and
IO-Link Class B
other actuators
Determination of
position
Control a
Control b
a
b
P
T
A
B
1V3
1S3
OBEA-V5
IO-Link
interface
IOL-Master
Outputs
PLC
Inputs
K1
O1.1
I1.1
I1.2
ÜB1
ÜB2
B1
ÜB1
B2
ÜB2
24 V
Open
Closed
1V2
1Z2
1S1 1S2
1Z1
1V1
1M
1P
Q1