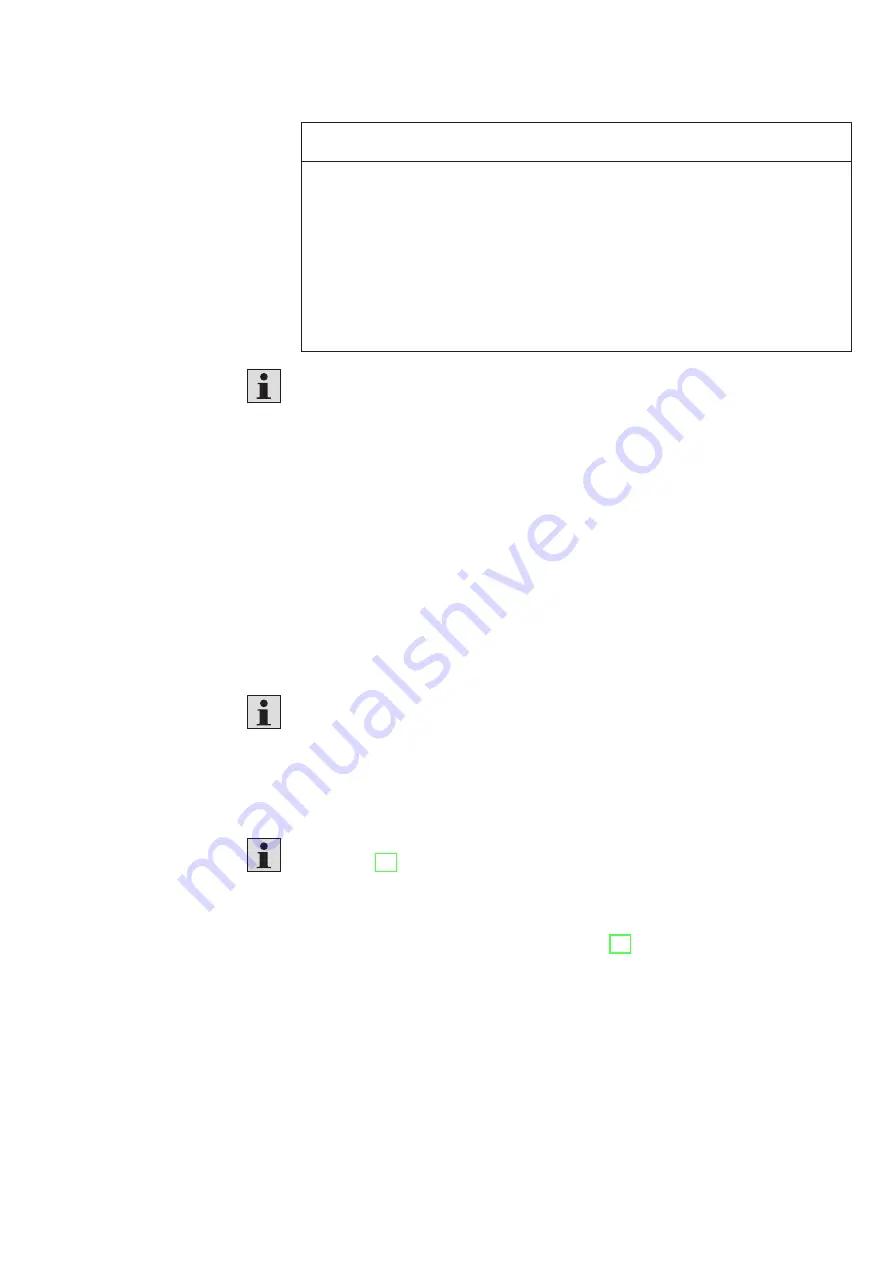
Installation 29/48
RE29583-XL-B/09.20, 4WS2EM 10...XL...,
Bosch Rexroth AG
NOTICE
Wear, tear and malfunctions!
The cleanliness of the hydraulic fluid has a considerable impact on the cleanliness
and life cycle of the valve. Any contamination of the hydraulic fluid will result in
wear and malfunctions. Particularly foreign particles may damage the valve.
▶
Always ensure absolute cleanliness.
▶
Install the valve in a clean condition.
▶
Make sure that all connections, hydraulic lines and attachment parts are clean.
▶
Ensure that no cleaning agents are able to penetrate the hydraulic system.
▶
Do not use hemp as a sealant under any circumstances.
If the valve is directly attached to a moveable actuator, the installation of the
valve control spool in parallel to the direction of acceleration of the actuator has
to be avoided.
1.
Before any assembly and disassembly work starts, the surroundings must be
cleaned so that no dirt can get into the oil circuit.
2.
Check the valve contact surface for the required surface quality
(see
"Data sheet 29583-XL"
). Remove the protective plate from the valve and
keep it safe for returns in case any repairs become necessary later.
3.
Dry the valve connection surface using suitable cleaning materials.
4.
Check the seal rings at the valve connection surface for completeness.
Other sealants are not admissible.
5.
Remove existing preservative agent.
6.
Check whether at the subplate, the pressure connecting line is connected to P,
and the return line to T.
Swapping P and T may cause damage at the valve when pressurized.
The valve ports X and Y are also pressurized in case of internal pilot oil supply
and pilot oil return. You must therefore make sure that the connection surfaces
X and Y are in any case sealed.
7.
Place the valve on the contact surface.
For reasons of stability, exclusively use the valve mounting screws specified in
chapter 7.6 "Required accessories"!
Always fasten the valve with all 4 valve mounting screws, otherwise leak-tightness
is not guaranteed.
8.
When using the subplates mentioned under 7.6 "Required accessories" or in case
of an assembly on comparable cast iron installation surfaces, tighten all four
mounting screws with a tightening torque of 12.5 Nm ± 1.5 Nm (with a friction
coefficient of µ
total
= 0.09...0.14). This tightening torque refers to the maximum
admissible operating pressure.