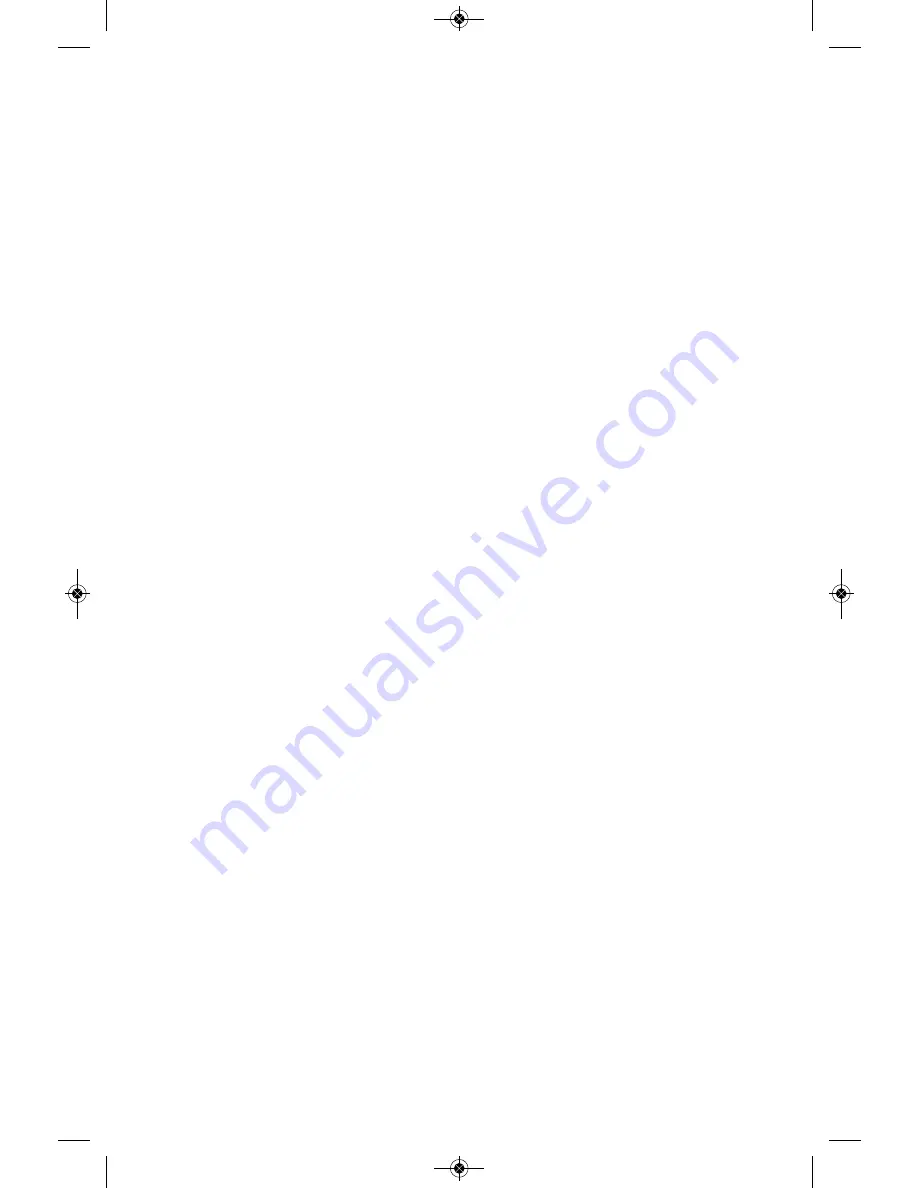
-4-
Wear personal protective equipment.
Depending on application, use face shield,
safety goggles or safety glasses. As
appropriate, wear dust mask, hearing
protectors, gloves and workshop apron
capable of stopping small abrasive or
workpiece fragments.
The eye protection
must be capable of stopping flying debris
generated by various operations. The dust
mask or respirator must be capable of filtrating
particles generated by your operation.
Prolonged exposure to high intensity noise may
cause hearing loss.
Keep bystanders a safe distance away from
work area. Anyone entering the work area
must wear personal protective equipment.
Fragments of workpiece or of a broken
accessory may fly away and cause injury
beyond immediate area of operation.
Hold the power tool by insulated gripping
surfaces only, when performing an
operation where the cutting accessory may
contact hidden wiring or its own cord.
Cutting accessory contacting a “live” wire may
make exposed metal parts of the power tool
“live” and could give the operator an electric
shock.
Position the cord clear of the spinning
accessory.
If you lose control, the cord may be
cut or snagged and your hand or arm may be
pulled into the spinning accessory.
Never lay the power tool down until the
accessory has come to a complete stop.
The spinning accessory may grab the surface
and pull the power tool out of your control.
Do not run the power tool while carrying it
at your side.
Accidental contact with the
spinning accessory could snag your clothing,
pulling the accessory into your body.
Regularly clean the power tool’s air vents.
The motor’s fan will draw the dust inside the
housing and excessive accumulation of
powdered metal may cause electrical hazards.
Do not operate the power tool near
flammable materials.
Sparks could ignite
these materials.
Do not use accessories that require liquid
coolants.
Using water or other liquid coolants
may result in electrocution or shock.
Kickback and Related Warnings
Kickback is a sudden reaction to a pinched or
snagged rotating wheel, backing pad, brush or
any other accessory. Pinching or snagging
causes rapid stalling of the rotating accessory
which in turn causes the uncontrolled power
tool to be forced in the direction opposite of the
accessory’s rotation at the point of the binding.
For example, if an abrasive wheel is snagged
or pinched by the workpiece, the edge of the
wheel that is entering into the pinch point can
dig into the surface of the material causing the
wheel to climb out or kickout. The wheel may
either jump toward or away from the operator,
depending on direction of the wheel’s
movement at the point of pinching. Abrasive
wheels may also break under these conditions.
Kickback is the result of power tool misuse
and/or incorrect operating procedures or
conditions and can be avoided by taking proper
precautions as given below.
Maintain a firm grip on the power tool and
position your body and arm to allow you to
resist kickback forces. Always use auxiliary
handle, if provided, for maximum control
over kickback or torque reaction during
start-up.
The operator can control torque
reactions or kickback forces, if proper
precautions are taken.
Never place your hand near the rotating
accessory.
Accessory may kickback over your
hand.
Do not position your body in the area where
power tool will move if kickback occurs.
Kickback will propel the tool in direction
opposite to the wheel’s movement at the point
of snagging.
Use special care when working corners,
sharp edges etc. Avoid bouncing and
snagging the accessory.
Corners, sharp
edges or bouncing have a tendency to snag the
rotating accessory and cause loss of control or
kickback.
Do not attach a saw chain woodcarving
blade or toothed saw blade.
Such blades
create frequent kickback and loss of control.
Safety Warnings Specific for
Grinding and Abrasive
Cutting-Off Operations:
Use only wheel types that are
recommended for your power tool and the
specific guard designed for the selected
wheel.
Wheels
for
which
the
power tool was not designed cannot be
adequately guarded and are unsafe.
The grinding surface of centre depressed
wheels must be mounted below the plane of
the guard lip.
An improperly mounted wheel
that projects through the plane of the guard lip
cannot be adequately protected.
2610041357 09-15 GWS10 GWS13.qxp_GWS series 9/18/15 12:56 PM Page 4