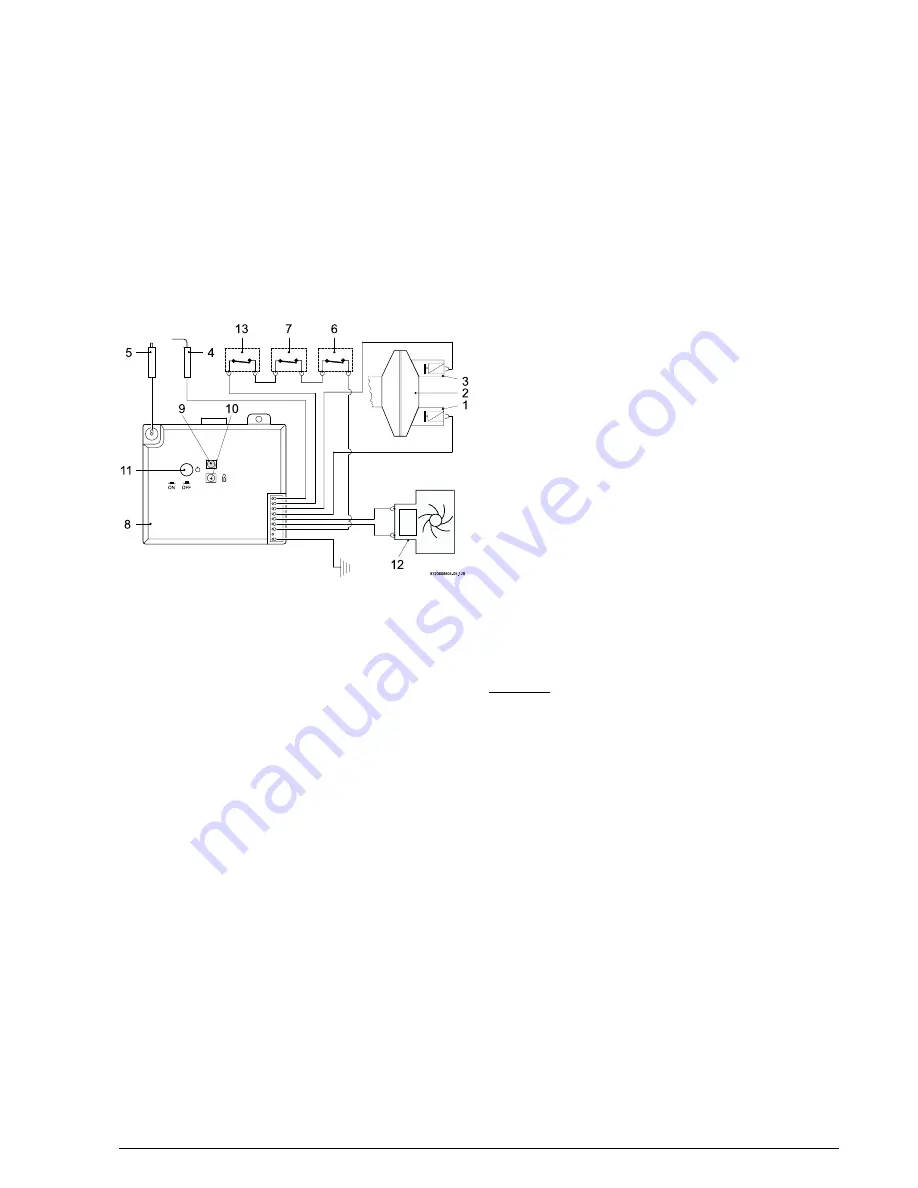
15
6 720 607 026
Fig. 13 - Electrical wiring diagram
5. Flue gas safety device tripped
Ventilate the room and operate the appliance 10 minutes
later. Provide more combustion air to the room and/or inspect
and correct venting system. Afterwards, if it happens again,
contact your service person.
WATER IS TOO HOT
1
.
Temperature Selection too high
Turn the temperature adjustment knob counter-clockwise
(to the left) to lower the maximum water temperature.
Note: This will increase the activation flow rate.
2. Inlet water temperature is too hot (as with solar
preheated water or high ground water temperatures)
Decrease gas pressure.
Note:
Only the model 125B LPS or
125B NGS should be used if the inlet water is preheated.
3. Ground water temperature is very warm
Reduce inlet gas supply to heater when inlet water
temperature is very warm (60-70 F). See also HOT WATER
TEMPERATURE FLUCTUATES / UNIT DEACTIVATED.
WATER IS NOT HOT ENOUGH
1. Temperature selection too low.
Change the setting. Turn the temperature adjustment knob
clockwise (to the right).
Note: This will decrease the activation flow rate.
2. Btu input is too low due to insufficient gas pressure
It is extremely important for a tankless instantaneous
water heater to have the right size gas line to obtain
the
correct
gas
pressure
See specifications on page 2. Unlike storage tank water
heaters, the burners of a tankless water heater must be very
powerful to heat water instantaneously since they do this
only at the time hot water is actually being used. It is therefore
imperative that the gas pressure requirement be met exactly.
Insufficient gas pressure will directly affect the water
temperature at the time of usage. See page 2 for correct
gas pressure settings and fig. 5 for locations where gas
pressures are taken.
3. Btu input is too low due to insufficient gas supply
Make sure your main gas line is fully opened. If using LP
gas, be sure that the size of the propane tank is adequate to
supply the required gas pressure.
4. Cold water is mixing with the hot water between the
425 HN and the outlet
Compare water temperature at outlet of the 425 HN (hold
the 425 HN outlet pipe with your hand) and at the tap. If
these two are very different, check for mixing valve or
plumbing crossover (see “NO SPARK AT THE PILOT”
paragraph #4).
5. Parts in water valve are dirty or damaged, which will
prevent the gas valve from being fully opened.
Water valve maintenance needs to be performed, see #6
under NO SPARK AT THE PILOT
PILOT LIGHTS BUT BURNERS WILL NOT COME ON
1. Confirm water valve assembly is working properly.
See Water Valve under
MAINTENANCE AND SERVICE
.
2. Confirm the flame sensor is in its proper position and
clean, lightly wipe clean if dirty.
See Fig. 10
3. Confirm the burner electrovalve switch is functioning
properly.
Measure milivoltage at burner electrovalve (see Fig. 13).
4. The Electronic Control Box (Fig. 13) may need to be
replaced.
Check wire connections and test operation of electronic
control box (see Fig. 13).
8
electronic control box
9
LED failure indicator
10
LED indicator main
burner operation
11
on/off switch
12
hydro-generator
13
flue gas safety device
1
burner electrovalve
2
gas control valve
3
pilot electrovalve
4
flame sensor
5
pilot electrode
6
overheat sensor
7
temperature limiter
MAIN BURNERS GO OUT DURING HOT WATER USE
1. Flow rate diminished below activation rate
Increase hot water flow rate.
2. Unbalanced pressure in the water lines
The added restriction caused by the 425 HN in the hot
water system can result in uneven pressures between the
cold and the hot. In such cases when mixing cold water at
the tap, the lower hot water pressure may be overpowered
by a much higher cold water pressure, which may cause the
425 HN burners to shut down. Make sure faucet aerators
and showerheads are free of minerals and dirt. Do not add
any flow restrictor to the shower head.
3. Minimum inlet pressure on well is inadequate
Check the inlet water pressure. On a private well, raise the
minimum pressure setting to 30 psi. Confirm that the
pressure tank is not water logged.
4. ECO (overheat sensor) tripped due to overheating
re-ignite the appliance 10 minutes later. If it happens again,
contact your service person.