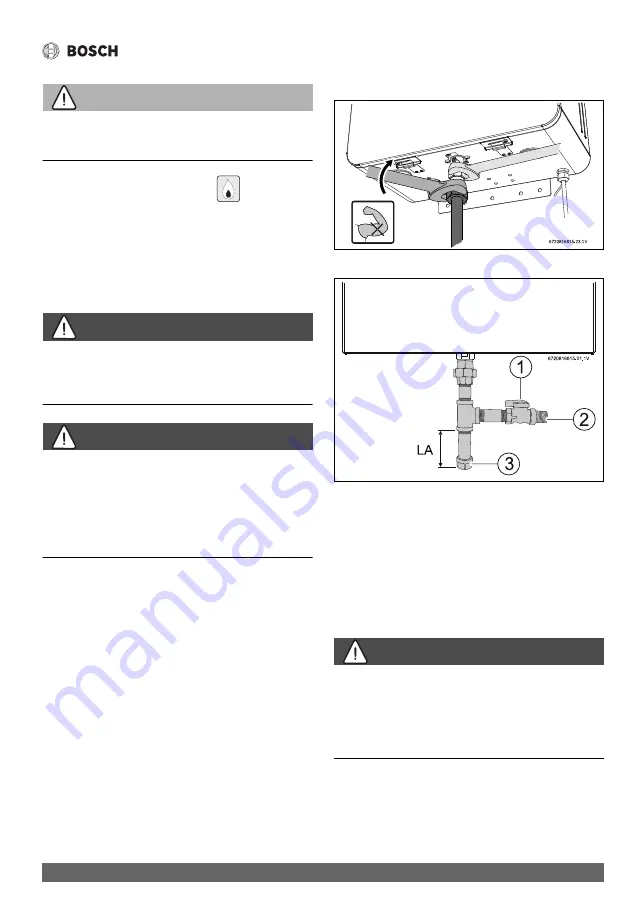
Installation instructions
33
Greentherm T9900 SE/i – 6 720 813 635 (2019/03)
WARNING:
▶ The gas type conversion must only be carried out by a
qualified contractor.
4.8
Gas piping & connections
Before connecting the gas supply, be sure that the heater is set
for the same gas to which it will be connected.
In the United States: The installation must conform with local
codes or, in the absence of local codes, the National Fuel Gas
Code ANSI Z223.1/NFPA 54.
In Canada: The Installation must conform to CGA B149
INSTALLATION CODES and/or local installation codes.
DANGER:
Explosion hazard!
▶ DO NOT connect to an unregulated or high pressure
propane line or to a high pressure commercial natural gas
line.
DANGER:
Explosion hazard!
▶ The heater must be isolated from the gas supply piping
system during any pressure testing of that system at test
pressures equal to or more than 0.5 psig. If overpressure
has occurred, such as through improper testing of the gas
lines or malfunction of the supply system, the gas valve
must be checked for safe operation.
GAS CONNECTIONS
▶ Install a manual gas shut off valve on the gas supply line
within easy reach of the appliance.
▶ Install a union when connecting the gas supply.
▶ Gas connection to the water heater is ¾" NPT. See chapter
4.8.1 for the minimum internal pipe diameter required.
▶ Undersized flexible appliance connector is not permitted.
▶ National Fuel Gas Code requires that a sediment trap (drip
leg) be installed on gas appliances not so equipped. The
drip leg must be accessible and not subject to freezing
conditions. Install in accordance with the
recommendations of the serving gas supplier, see fig. 25.
▶ Tighten gas pipe with the support of a wrench, see fig. 24.
Fig. 24
Tighten gas pipe to the heater
Fig. 25
Gas connection
[1]
Shut off valve
[2]
Gas supply
[3]
Cap
[LA] Minimum 3" sediment trap, (drip leg)
Once connections are made, check for gas leaks at all joints.
Apply some gas leak detection solution to all gas fittings.
Bubbles are a sign of a leak. A combustible gas detector may
also be used to detect for leaks.
DANGER:
Explosion hazard!
▶ If you detect a gas leak, shut off the gas and ventilate the
room (open windows, doors). Tighten appropriate fittings
to stop leak. Turn the gas on and check again with a gas leak
detection solution. Never test for gas leaks using a match or
flame.