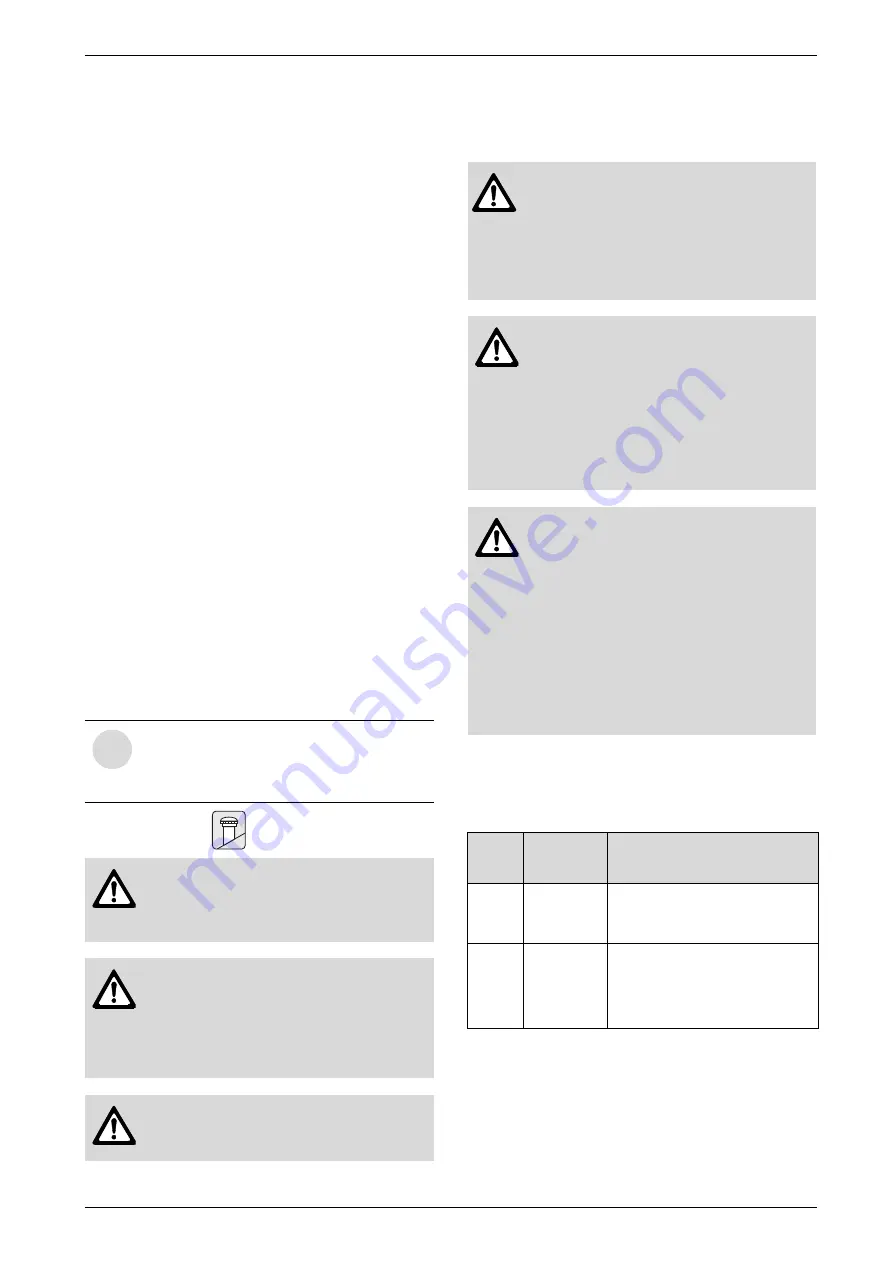
6 720 680 223
Installation instructions
9
3
Installation instructions
3.1
Tools required for installation
• Philips head screwdriver
• Flat head screwdriver
• Adjustable wrench
• Level
• Thermometer
• Standard plumbing tools
• Manometer
• Drill
• Pipe wrench
• Adjustable pliers
• Pipe fitting tools
• Hacksaw
• Hole saw.
3.2
Introduction
Please follow these instructions. Failure to follow
instructions may result in:
B
Damage or injury.
B
Improper operation.
B
Loss of warranty.
If you are unable to perform the tasks required to install
this heater properly, please contact a locally licensed
plumber or gas technician.
3.3
Venting
3.3.1
Vent material
Establish vent clearances that comply with the vent
manufacturer's specifications. In all cases, follow local
codes. See Table 2.
i
Common installation practice is to deter-
mine the venting/intake system layout and
penetration and then work back to the
heater.
Warning:
Do not reduce the vent
(exhaust and combustion) pipe sizes
and do not common vent with any other
vented appliance or stove.
Warning:
Failure to vent the exhaust
gases to the outside with sealed
stainless steel vent pipe (AL29-4C)
may result in dangerous flue gases
filling the structure in which it is
installed.
Warning:
Do not mix vent pipe or
joining
methods
from
different
manufacturers.
Warning:
Approved terminators must
be used for inlet and exhaust vent sys-
tems to prevent rain from entering the
appliance. Failure to do so may result in
damage to the appliance. This failure is
not covered under the manufacturer’s
warranty.
Caution:
The vent system must be
installed by a qualified installer in
accordance with these instructions. If
improperly installed, a hazardous
condition such as explosion or carbon
monoxide poisoning could result.
Bosch Water Heating will not be
responsible for improperly installed
appliances.
Warning:
In areas where outside
temperatures routinely come close to
freezing, sealed combustion operation
is required. Use separate terminations
for combustion and vent, which must be
installed on the same wall or roof
surface, however never facing the
direction of prevailing winds. Failure to
do so may result in heat exchanger
freezing up and bursting. This failure is
not covered under the manufacturer's
warranty.
Diam.
Material
Exhaust
Vent
3 or 4 inches
Sealed single wall stainless steel
(AL29-4C)
Intake
Vent
3 or 4 inches Sealed PVC or any other rigid pipe
Table 2 Venting Specifications