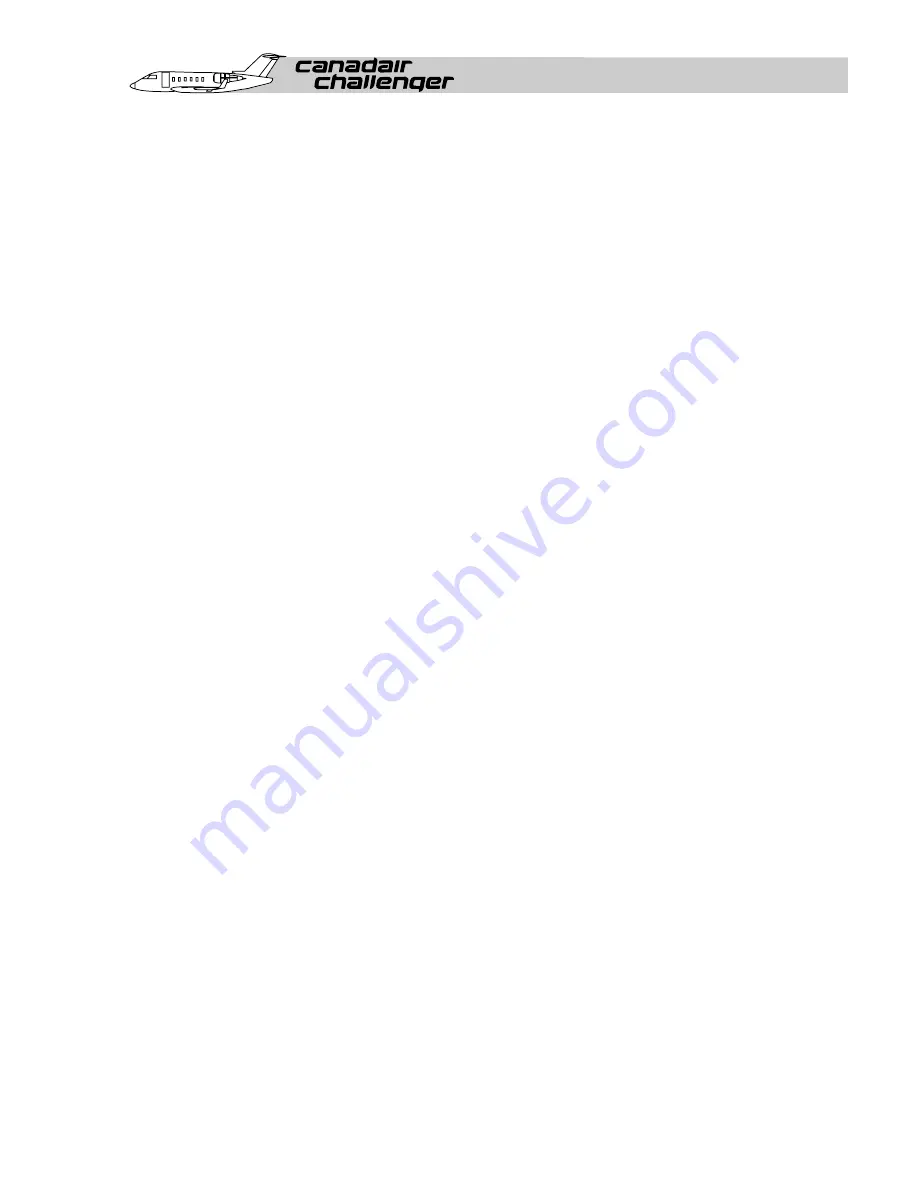
NEGATIVE PRESSURE RELIEF
A negative pressure-relief feature is part of
each outflow valve to prevent atmospheric
pressure from exceeding cabin pressure. In
effect, one side of each outflow valve di-
aphragm is exposed to atmospheric pressure
while the opposite side is exposed to cabin
pressure. If the atmosphere to cabin pressure
differential reaches approximately 0.5 psid,
atmospheric pressure will open the outflow
valve poppets and equalize the cabin and at-
mospheric pressures. If this occurs during de-
scent, the cabin will descend at the same rate
as the airplane. This can produce physical dis-
comfort if the rate is sufficiently high.
PNEUMATIC RELAY
A pneumatic relay is incorporated in the pneu-
matic (right) outflow valve only. In the auto-
matic mode, the pneumatic relay is inactive.
Loss of battery bus power or moving the
MODE switch to MANual activates the pneu-
matic relay which then responds to the MAN-
ual regulator UP-DOWN lever and the manual
RATE knob to control the metering rate of
both outflow valves.
ASSOCIATED SYSTEM
(GROUND MODE)
A ground pressurization control mode is in-
corporated and is identified as an associated
system which is operational only on the ground
in the automatic mode.
GROUND OPERATION
(BEFORE TAKEOFF)
The pressurization system may be programmed
prior to engine starting if electrical power is
available and the MODE selector switch is in
the AUTOmatic position. The cabin will not
normally pressurize even if both air condi-
tioners are selected “ON” because the WOW
(weight-on-wheels) system is in the ground
mode and the automatic selector controls the
left outflow valve, causing both valves to go
to the full open position. This condition will
prevail until the thrust levers are advanced
beyond the 35° thrust lever quadrant position
which equates to approximately 80% N
1
rpm.
Then the automatic selector will signal the
left outflow valve to close (the right outflow
valve is slaved to the left and will also close),
and a predetermined cabin pressure buildup (at
a controlled rate) will occur. This tends to
eliminate pressure surges after lift-off. Fol-
lowing lift-off, the WOW system will go to the
flight mode and normal pressurization schedul-
ing will begin.
GROUND OPERATION
(LANDING)
Normal pressurization scheduling for landing
is field elevation for 60 seconds and then both
outflow valves open fully. When the WOW sys-
tem goes to the ground mode, the automatic se-
lector schedules outflow valve opening at the
selected rate of depressurization.
FlightSafety Canada
L t é e
L t d .
CL-600-2B16 PILOT TRAINING MANUAL
CL 601-3A
12-5
FOR TRAINING PURPOSES ONLY