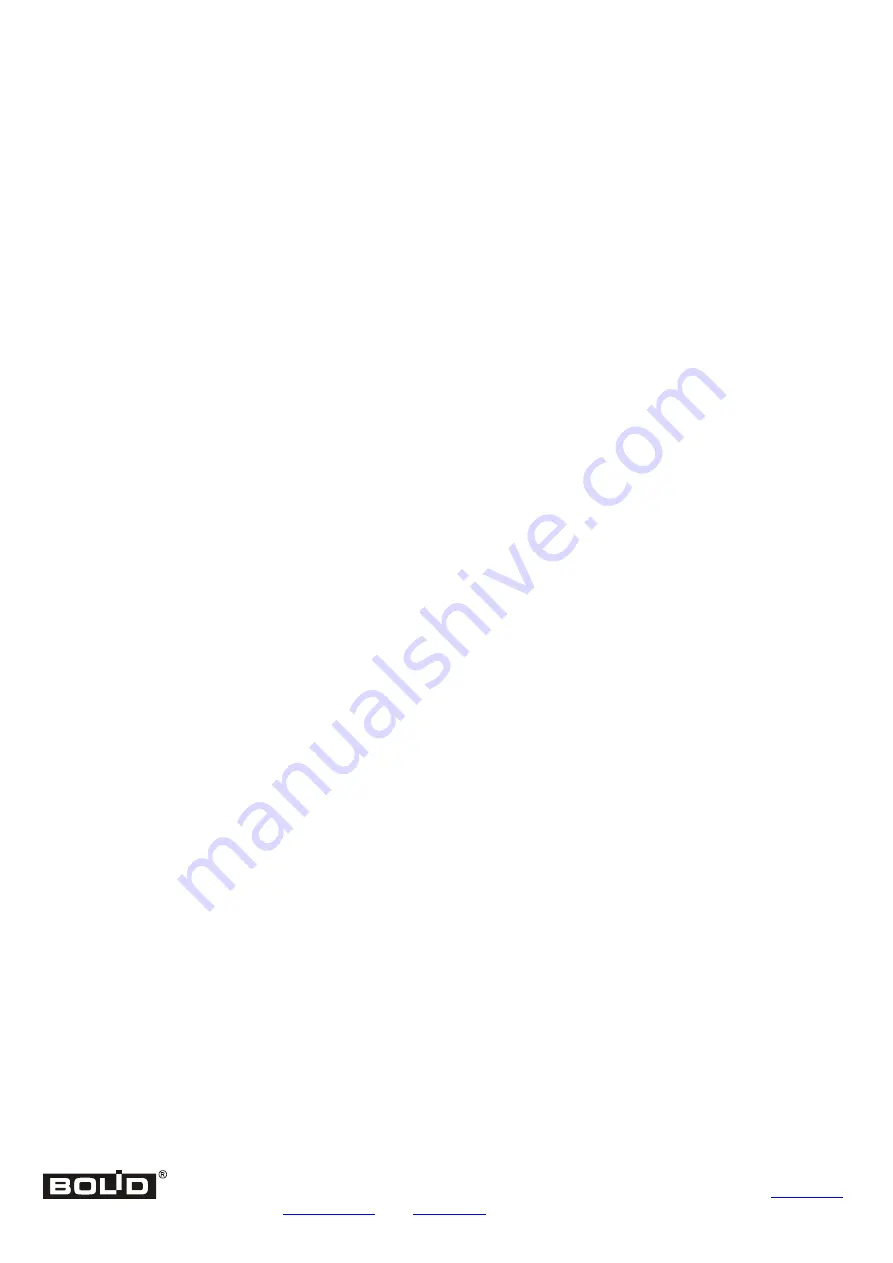
A T T E N T I O N
To install the detector on the base plate, align the guide on the detector with the short guide of the base plate. Then turn the detector clockwise until the
detector guide is aligned with guide 3 as shown in Figure 2 (A)
.
2.3
Programming the Detector Address
The detector provides storing its address within the polling loop for communicating with the PLC in the non-volatile memory. The factory address for the gas part
of the detector is 126 while the factory address for the thermal part of the detector is 127.
There are two ways to give an address to an S2000-IPG, the first way is to set a required address and the second way is to change the known address value to the
required value. Each of these commands can be sent from a network controller or by means of the UProg configuration tool.
When the command for setting a given address is used (for example, in case when the same address is incorrectly assigned to two different devices into the polling
loop), together with sending the command within 5 minutes press on the detector’s LED or light it with the beam of a laser test tool. The network controller shall show
a message about disconnecting the device with an old address and connecting the device with the newly programmed address. In the case when two devices had the
same address no message about disconnecting the device with the old address is indicated.
If the current address of the detector is known and should be changed for another address, send the change address command from the network controller with the
old address and the new address as the parameters. The network controller shall indicate a message about disconnecting the device with the old address and connecting
the device with the new address.
Then write the programmed address on the address label provided and stick this label to the detector base.
2.4
Testing
2.4.1
Before testing notify the proper authorities that the detector is undergoing maintenance and will be temporarily out of service. Disconnect all outputs of
control devices and executive modules that can run an automated fire-fighting system.
2.4.2
Power on the S2000M panel or Orion Pro Workstation and the PLC and observe steady lighting of the detector’s LED. As soon as communication between
the detector and the polling loop controller has been established the detector’s LED starts pulsing once per 4 s indicating the Norm condition.
2.4.3
Observing safety regulations spray a small amount of test gas from the aerosol can into the detector. The S2000M panel or Orion Pro Workstation shall
display a Fire Alarm for the relevant address. The detector’s LED shall flash doubly with intervals 0.5 s in pairs once per four seconds.
2.4.4
To test the thermal part of the detector, blow it with hot air (for example, from a hairdryer). A Fire Alarm message shall be issued with the relevant address.
2.4.5
The detector can also be tested by pressing on its LED and keeping it pressed for at least 2 s or by lighting it with the laser beam of a laser test tool. This will
cause the LED to show solid light: if an S2000-KDL of version 1.40 or higher is in use then the network controller (S2000M or Orion Pro Workstation) shall indicate
Alarm Test or Fire Alarm depending on the test mode. To get more information about light indication of the detector when an S2000-KDL of version 1.30 and higher is
in use and about testing please refer to user’s manuals for the S2000-KDL, S2000M and Orion Pro software.
2.4.6
When the light emitter is released or the laser test tool is disposed ensure the network controller indicates the Norm condition of the detector. If the S2000M
panel or Orion Pro software has displayed no messages mentioned above for the address of the detector or the detector’s LED performs in a different way, then the
detector is unhealthy and must be replaced
.
2.4.7
After testing, restore all binds between system executive outputs and automated fire-fighting system and notify the proper authorities that the system is back
in operation.
2.5
Maintenance
2.5.1
Inspect operation of the detector as discussed in Section 2.4 annually.
2.5.2
Inspect operation of the detector when it sends trouble messages.
W A R N I N G
1)
To avoid contamination of the detector please do not remove the protective cover until the surrounding area is cleaned from dirt and dust.
2)
Do not attempt to remove the detector PCB. Disassembling the detector automatically cancels the warranty.
3)
The detector is not designed to be installed within areas where air velocity exceeds 15 m/s.
3
CERTIFICATES
3.1
S2000-IPG Analog Addressable Combined Gas and Rate-of-Rise and Fixed Temperature Detector is approved by Conformity Certificate
№
C-RU.
ЧС
13.
В
.00542.
3.2
Production of S2000-IPG detectors is certified according to
ОСТ
ISO 9001-2011 by Conformity Certificate No.
РОСС
RU.
ИК
32.
К
00153.
4
PRODUCT ACCEPTANCE CERTIFICATE
The S2000-IPG analog addressable combined gas and rate-of-rise and fixed temperature detector (the serial number can be seen on the detector enclosure) is
qualified as proper for operation and packaged by CJSC NVP “Bolid”.
Accepted and packaged by
Quality Department __________________________________ _____________________________________
Full Name
Date, Month, Year
ZAO NVP Bolid, 4 Pionerskaya Str., Korolev 141070, Moscow Region, Russia; Phone/fax: +7 495 775-7155; Email:
Technical Support:
; Web:
http://bolid.ru