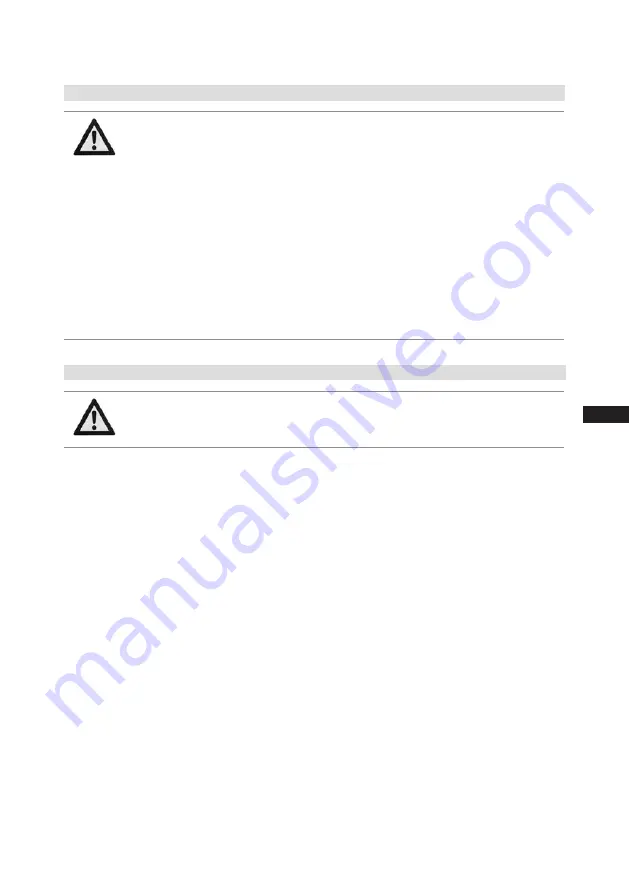
D
GB
F
E
I
Ru
5
09971-01.2021-DGbFEIRu
1
|
Safety
1.4 Intended use
1.3 General safety instructions
WARNING
Risk of accidents.
Refrigerating compressors are pressurised machines and as such
call for heightened caution and care in handling.
The maximum permissible overpressure must not be exceeded,
even for testing purposes.
Risk of burns!
- Depending on the operating conditions, surface temperatures of
over 60°C on the discharge side or below 0°C on the suction side
can be reached.
- Avoid contact with refrigerant necessarily.
Contact with refrigerant can cause severe burns and skin
damage.
WARNING
The compressor may not be used in potentially explosive
environments!
These assembly instructions describe the standard version of the compressor named in the title
manufactured by Bock. Bock refrigerating compressors are intended for installation in a machine
(within the EU according to the EU Directives 2006/42/EC Machinery Directive, 2014/68/EU Pressure
Equipment Directive).
Commissioning is permissible only if the compressor has been installed in accordance with these as-
sembly instructions and the entire system into which it is integrated has been inspected and approved
in accordance with legal regulations.
The compressors are intended for use in refrigeration systems in compliance with the limits of
application.
Only the refrigerant specified in these instructions may be used.
Any other use of the compressor is prohibited!