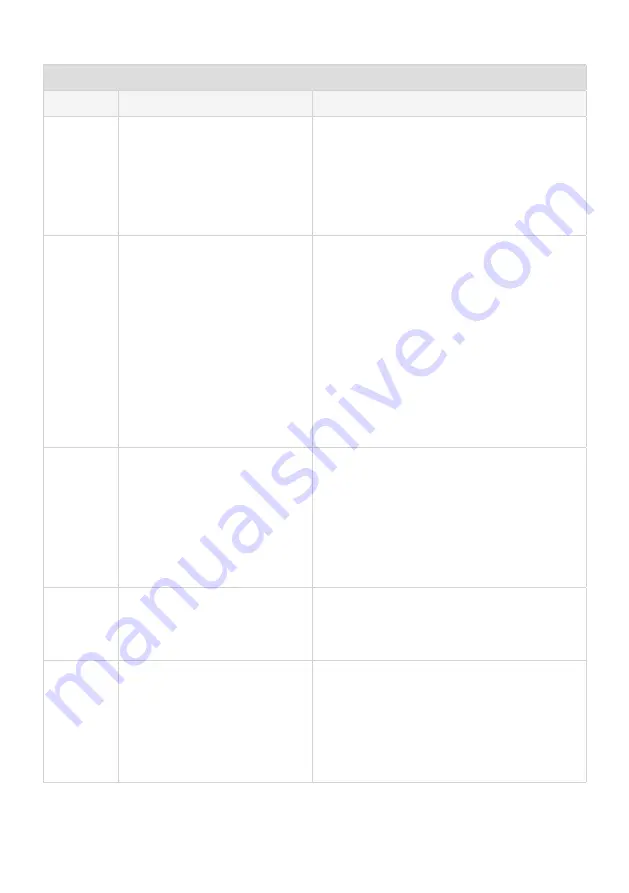
27
Troubleshooting guide
Problem
Cause
Solution
Porosity
in Weld
Deposit
5. Alloy impurities in the base metal
such as sulphur, phosphorous, lead
and zinc
6. Excessive travel speed with rapid
freezing of weld trapping gases
before they escape
7. Contaminated shield gas
5. Change to a different alloy composition which is
weldable. These impurities can cause a tendency to
crack when hot.
6. Lower the travel speed
7. Replace the shielding gas
Cracking in
Welds
1. Hot cracking in heavy section or
with metals which are hot shorts
2. Crater cracks due to improperly
breaking the arc or terminating the
weld at the joint edge
3. Post weld cold cracking due to
excessive joint restraint, rapid
cooling or hydrogen embrittlement
4. Centreline cracks in single pass weld
5. Underbead cracking from brittle
microstructure
1. Preheat. Increase weld bead cross-section size.
Change weld bead contour. Use metal with fewer
alloy impurities
2. Reverse direction and weld back into previous weld at
edge. Use Amprak or foot control to manually down
slope current
3. Preheat prior to welding. Use pure or non-
contaminated gas. Increase the bead size. Prevent
craters or notches. Change the weld joint design.
4. Increase bead size. Decrease root opening. Use
preheat. Prevent craters.
5. Eliminate sources of hydrogen, joint restraint, and use
preheat
Inadequate
shielding
1. Gas flow blockage or leak in hoses
or torch
2. Excessive travel speed exposes
molten weld to atmospheric
contamination
3. Wind or drafts
4. Excessive electrode stickout
5. Excessive turbulence in gas stream
1. Locate and eliminate the blockage or leak
2. Use slower travel speed or carefully increase the
flow rate to a safe level below creating excessive
turbulence. Use a trailing shield cup.
3. Set up screens around the weld area
4. Reduce electrode stickout. Use a larger size cup
5. Change to gas safer parts or gas lens parts
Arc Blow
1. Induced magnetic field from DC
weld current
2. Arc is unstable due to magnetic
influence
1. Rearrange the split ground connection
2. Reduce weld current and use arc length as short as
possible
Short parts
Life
1. Short water cooled leads life
2. Cup shattering or cracking in use
3. Short collet life
4. Short torch head life
1. Verify coolant flow direction. Return flow must be on
the power cable lead
2. Change cup size or type. Change tungsten position
3. Ordinary style is split and twists or jams. Change to
wedge style
4. Do not operate beyond rated capacity. Use water
cooled model. Do not bend rigid torches