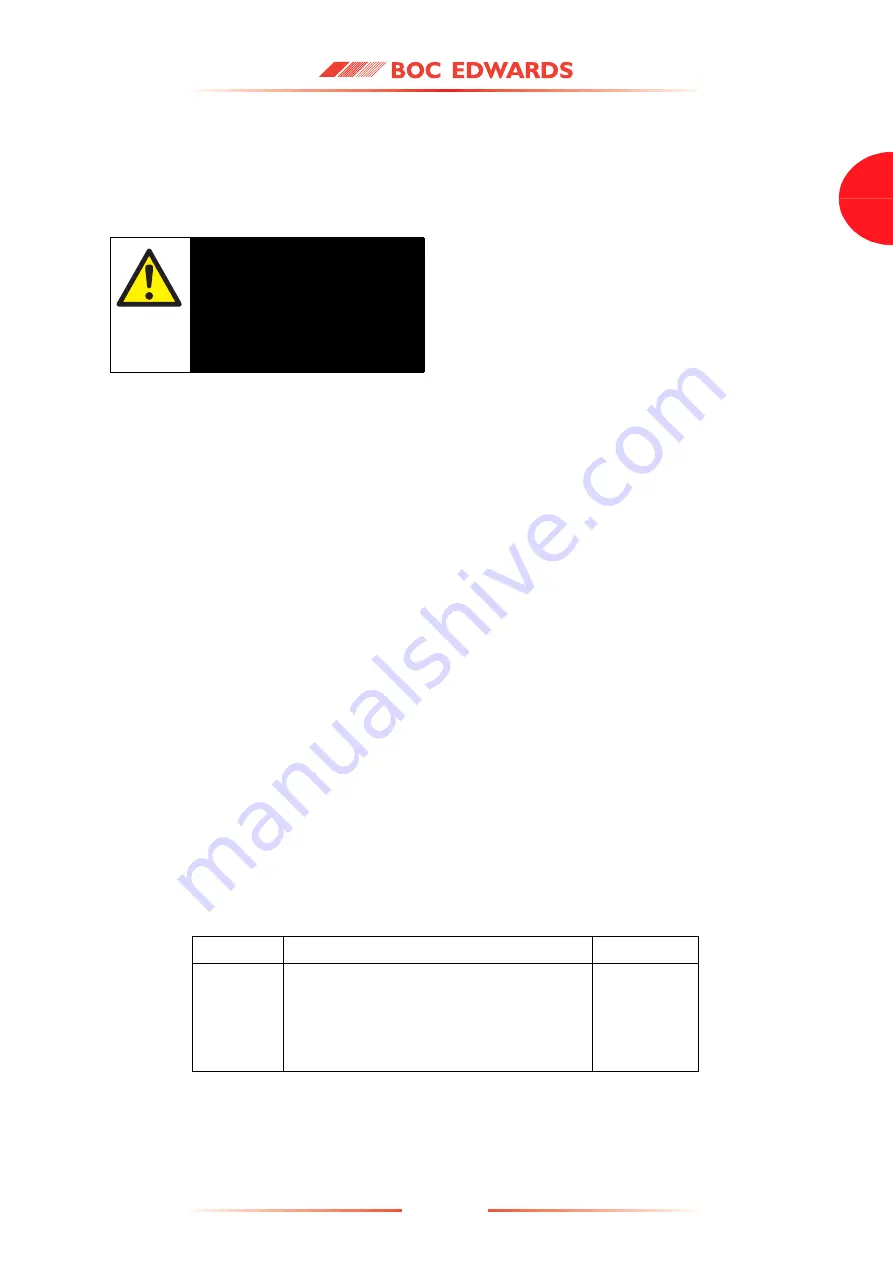
Feb 04
Issue A
18B4B Vapour Booster Pumps
PAGE
15
15
IN
STALLATION
3
INSTALLATION
3.1
Safety
• A suitably trained and supervised technician
must install the pump.
• Isolate the other components in the vacuum
system from the electrical supply before you
start work.
• Use suitable lifting equipment when you move
the pump.
• Ensure that the products handled by the
pumping system are compatible with the
materials of construction of the pump (see
Section 2.7). If you have any doubts about the
compatibility, contact your supplier or BOC
Edwards for advice.
• Do not use solvents to clean ‘O’ rings.
• Ensure that the installation technician is
familiar with the safety precautions which
relate to pump fluid and to the products
handled by the pumping system. Wear the
appropriate safety clothing when you come
into contact with pump fluid or contaminated
components. Dismantle and clean
contaminated components inside a fume
cupboard.
WARNING
Obey the safety instructions given
below and take note of appropriate
precautions. If you do not, you can
cause injury to people and damage to
equipment.
• Disconnect the other components of the
vacuum system from the electrical supply so
that they cannot be operated accidentally.
• Vent and purge the vacuum system with
nitrogen for 15 minutes before you start
installation work.
3.2
Unpack and inspect
1.
Remove all packing materials and protective
covers and check the pump. If the pump is
damaged, notify your supplier and the carrier in
writing within three days; state the Item
Number of the pump together with your order
number and your supplier's invoice number.
Retain all packing materials for inspection. Do
not use the pump if it is damaged.
2.
Check that you have received the items listed in
Table 9. If any item is missing, notify your
supplier in writing within three days.
3.
Check that your electrical supply voltage
corresponds to the voltage stated on the pump
identification and rating plate (Figure 3, item
11). If the pump is not suitable for use with your
electrical supply, do not continue to install and
use the pump.
If the pump is not to be used immediately, refit the
protective covers. Store the pump in suitable
conditions, as described in Section 6.1.
* Only supplied if the corresponding optional device is fitted: refer to the list of
Supplementary Publications at the end of the contents list.
Quantity
Description
Check (
✓
)
1
18B4B pump
❏
1
Fitting pack
❏
1
Pt100 temperature probe instructions *
❏
2
Fluid low level switch & sleeve instructions *
❏
Table 9 - Checklist of items
Summary of Contents for 18B4B
Page 1: ...B065 10 880 Issue A Original Instruction Manual 18B4B Vapour Booster Pumps...
Page 2: ...This page intentionally blank...
Page 12: ...Issue A Feb 04 18B4B Vapour Booster Pumps PAGE 6 6 This page intentionally blank...
Page 19: ...Feb 04 Issue A 18B4B Vapour Booster Pumps PAGE 13 13 TECHNICAL DATA Figure 3 Dimensions mm...
Page 20: ...Issue A Feb 04 18B4B Vapour Booster Pumps PAGE 14 14 This page intentionally blank...
Page 40: ...Issue A Feb 04 18B4B Vapour Booster Pumps PAGE 34 34 This page intentionally blank...
Page 54: ...Issue A Feb 04 18B4B Vapour Booster Pumps PAGE 48 48 This page intentionally blank...
Page 56: ...Issue A Feb 04 18B4B Vapour Booster Pumps PAGE 50 50 This page intentionally blank...
Page 61: ...This page intentionally blank...