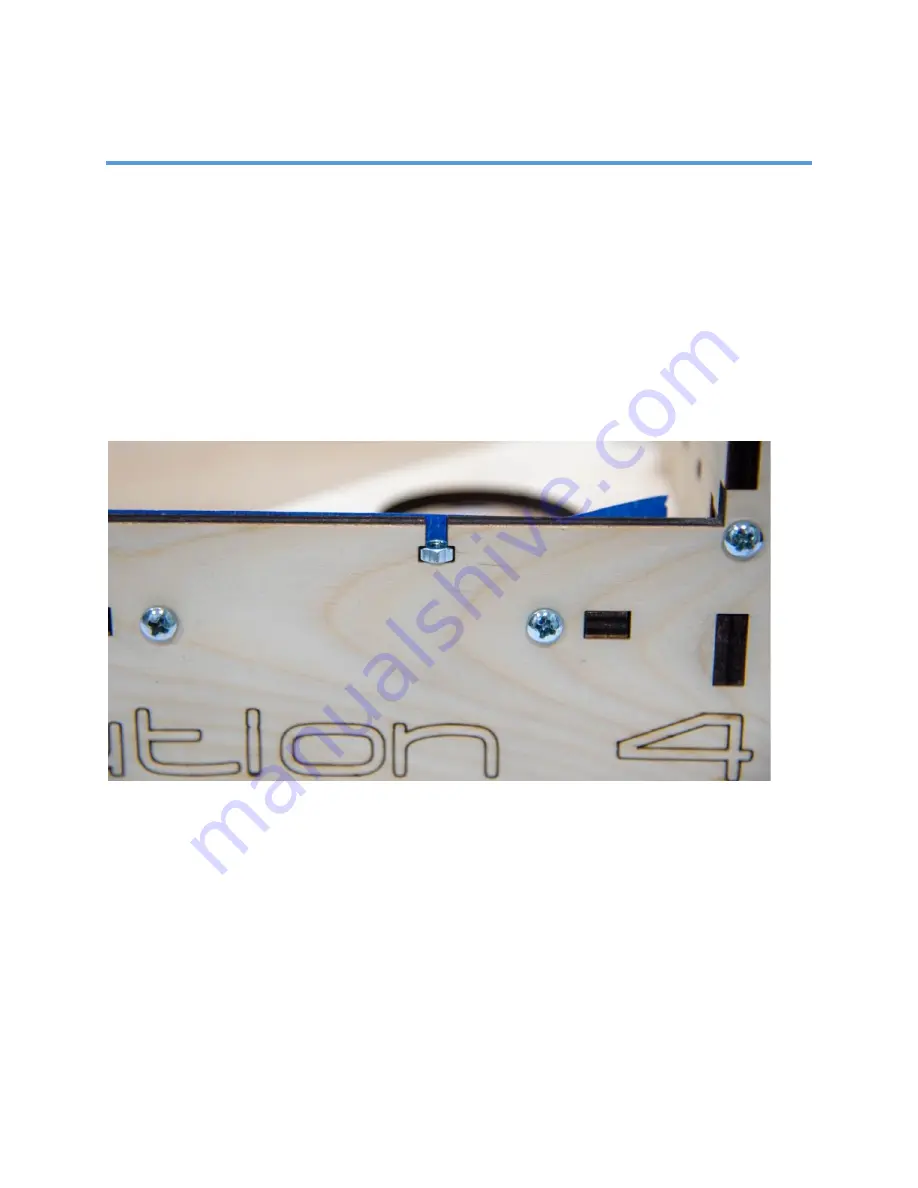
126
Spoilboard installation (optional)
Installing the Spoilboard. NOTE: Whether you are installing the Spoilboard
from BobsCNC or one of your own design, you should follow the same
basic steps.
Step 1
Insert 24 M4 Nuts into the Frame S
upport. Use 1” strips of
painter’s tape to hold them in place
as illustrated below.
Summary of Contents for Evolution 4
Page 1: ...Evolution 4 Assembly Manual Rev 1 06 ...
Page 20: ...19 1 2 3 4 ...
Page 22: ...21 The finished Z Assembly should look like this ...
Page 70: ...69 23d Connect the Y Home Switch plug to the Y pin on the Arduino Controller as shown ...
Page 78: ...77 28b Route the Power Wire through the Controller Mount as shown ...
Page 82: ...81 ...
Page 93: ...92 H60 M6 Nuts 8 H38 M4 x 30 Machine Screw 5 H15 M4 Nuts 4 R2 R3 Makita or DeWalt Router 1 ...
Page 129: ...128 Completed Views Front View Back View ...
Page 130: ...129 X1 Home Switch X1 Side View ...
Page 131: ...130 X2 Home Switch X2 Side View ...
Page 132: ...131 Z Home Switch Y Home Switch ...
Page 133: ...132 ...