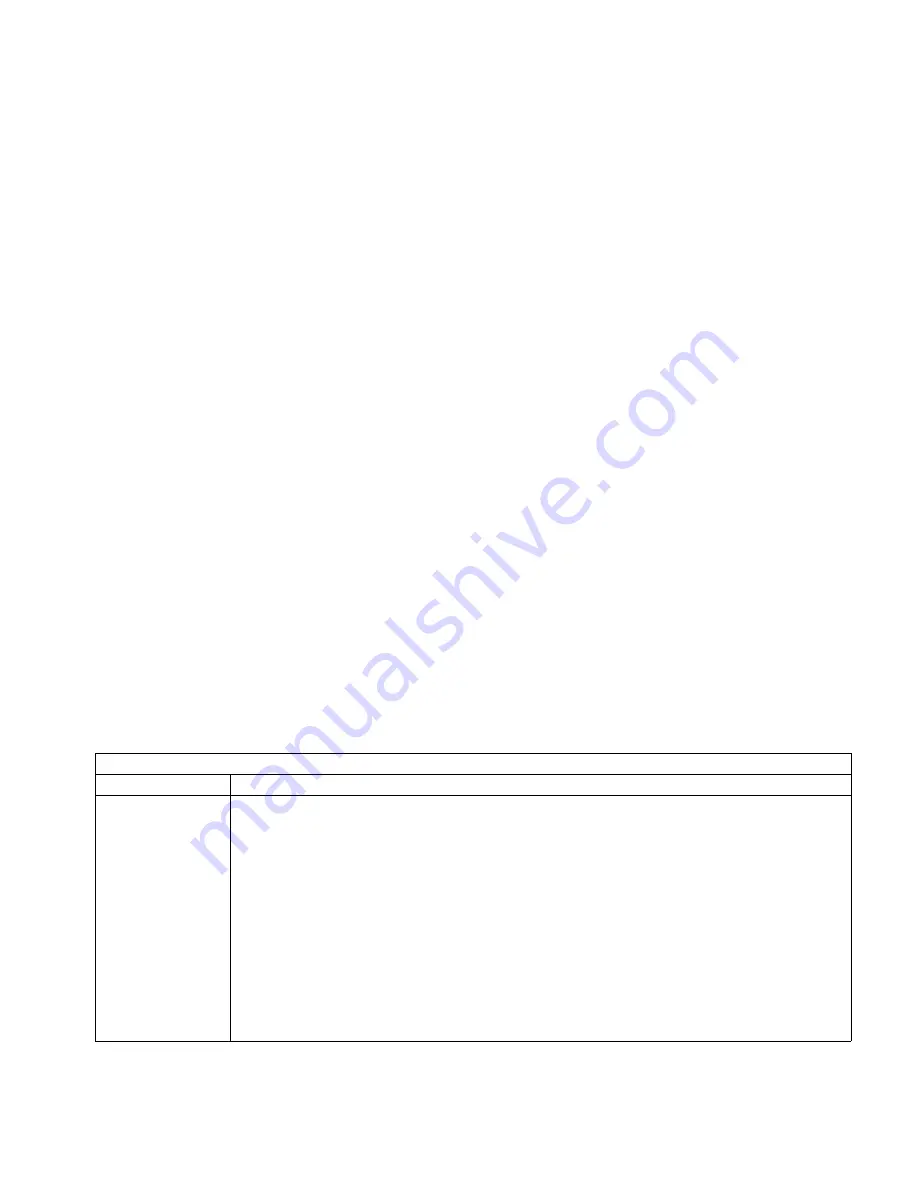
SECTION 3
PLANNED MAINTENANCE
3-1.
GENERAL.
Planned maintenance consists of periodic visual and
operational checks, parts inspection, lubrication, and
scheduled maintenance designed to prevent or dis-
cover malfunctions and defective parts. The operator
, and refers any
required servicing to a qualified maintenance techni-
cian who performs the scheduled maintenance and
any required servicing.
3-2.
MONTHLY AND QUARTERLY CHECKS.
is a monthly and quarterly inspection and
service chart based on normal usage of equipment
eight hours per day, five days per week. If the lift truck
is used in excess of forty hours per week, the fre-
quency of inspection and service should be increased
accordingly. These procedures must be performed by
a qualified service technician or your
Blue Giant
Ser-
vice Representative.
3-3. BATTERY CARE.
3-3.1.
General
The PDS may be equipped with maintenance free or
industrial wet cell batteries.
The care and maintenance of the battery is very
important to obtain efficient truck operation and maxi-
mum battery life.
CAUTION:
Gases produced by a battery can be
explosive. Do not smoke, use an open
flame, create an arc or sparks in the
vicinity of the battery. Ventilate an
enclosed area well when charging.
CAUTION:
Batteries contain sulfuric acid which may
cause severe burns. Avoid contact with
eyes, skin or clothing. In case of contact,
flush immediately and thoroughly with
clean water. Obtain medical attention
when eyes are affected. A baking soda
solution (one pound to one gallon of
water) applied to spilled acid until bub-
bling stops, neutralizes the acid for safe
handing and disposal.
Leakage voltage from battery terminals to battery case
can cause misleading trouble symptoms with the truck
electrical system. Since components of the truck elec-
trical system are insulated from truck frame, leakage
voltage will not normally affect truck operation unless a
short circuit or breakdown of circuit wire insulation to
truck frame occurs.
A voltage check from battery connector terminal to
battery case should indicate near zero volts. Typically,
however, the sum of the voltages at both terminals will
equal battery volts. This leakage voltage will discharge
the battery. As battery cleanliness deteriorates, the
usable charge of the battery decreases due to this self
discharge.
Table 3-1 Monthly and Quarterly Inspection and Service Chart
VISUAL CHECKS
INTERVAL
INSPECTION OR SERVICE
Monthly
Check electrical brake for proper operation.
Monthly
Check load wheels for wear. A poly load wheel must be replaced if worn to within 1/16 inch
of hub. Check for separation from hub.
Monthly
Check drive wheel for wear. A poly drive wheel must be replaced if worn to within 3/4 inch
of hub. Check for separation from hub.
Monthly
Inspect wiring for loose connections and damaged insulation.
Monthly
Inspect contactors for proper operation.
Monthly
Check deadman brake switch for proper operation.
Monthly
check lift chain tension, lubrication & operation (see paragraph
)
Quarterly
Check lift cylinder for leakage.
Quarterly
Check for excessive jerking of steering arm when stopping or starting.
Semi-annually
Inspect for chain wear (See
13
Summary of Contents for BGN-40
Page 6: ...Figure 1 2 PDS Lift Truck R6765 6...
Page 12: ...NOTES 12...
Page 18: ...NOTES 18...
Page 34: ...NOTES 34...
Page 39: ...Figure 5 4 Cap Assembly R6809 39...
Page 44: ...Figure 7 1 Transmission Motor Brake Assembly R6811 44...
Page 45: ...Figure 7 2 Adjustable Straddle R6814 45...
Page 46: ...NOTES 46...
Page 48: ...Figure 8 2 Elevation System Telescopic R6816 48...
Page 50: ...Figure 8 3 Mast TRIMAST R6817 50...
Page 52: ...NOTES 52...
Page 56: ...Figure 9 2 Mast Telescopic R6816 56...
Page 57: ...Figure 9 3 Lift Cylinder Telescopic R6825 57...
Page 59: ...Figure 9 4 Mast TRIMAST R6817 59...
Page 60: ...Figure 9 5Free Lift Cylinder TRIMAST R6826 60...
Page 62: ...Figure 9 6 Secondary Lift Cylinder TRIMAST R6827 62...
Page 64: ...Figure 10 1 Electrical System R6478 R6828A 64...
Page 67: ...Figure 10 3 Transmission Motor Brake Assembly R6811 67...
Page 68: ...NOTES 68...
Page 70: ...NOTES 70...
Page 72: ...Figure 12 1 Steering System R6807 72...
Page 74: ...Figure 12 2 Control Head R6808 74...
Page 76: ...Figure 12 3 Cap Assembly R6809 76...
Page 79: ...NOTES 79...
Page 80: ...Figure 12 5 Transmission Motor Brake Assembly R6811 80...
Page 82: ...Figure 12 6 Compartment R6813 82...
Page 84: ...Figure 12 7 Adjustable Straddle R6814 84...
Page 86: ...Figure 12 8 Fixed Straddle PDS 40 ONLY R6844 86...
Page 88: ...Figure 12 9 Caster Adjustable Straddle R6834 88...
Page 90: ...Figure 12 10 Caster Fixed Straddle R6845 90...
Page 92: ...Figure 12 11 Elevation System Telescopic R6816 92...
Page 94: ...Figure 12 12 Elevation System TRIMAST R6817 94...
Page 96: ...Figure 12 13 Lift Carriage R6815 96...
Page 100: ...Figure 12 16 Pump Motor Assy R6820 100...
Page 102: ...Figure 12 17 Hydraulic System Telescopic R6821A 102...
Page 104: ...Figure 12 18 Hydraulic System Telescopic R6822A 104...
Page 106: ...Figure 12 19 Hydraulic System TRIMAST R6823A 106...
Page 108: ...Figure 12 20 Hydraulic System TRIMAST R6824 108...
Page 110: ...Figure 12 21 Lift Cylinder Telescopic R6825 110...
Page 112: ...Figure 12 22 Free Lift Cylinder TRIMAST R6826 112...
Page 114: ...Figure 12 23 Secondary Lift Cylinder TRIMAST R6827 114...
Page 116: ...Figure 12 24 Electrical System R6828A 116...
Page 119: ...NOTES 119...
Page 120: ...Figure 12 26 Drive Motor R6830 120...
Page 125: ...125...