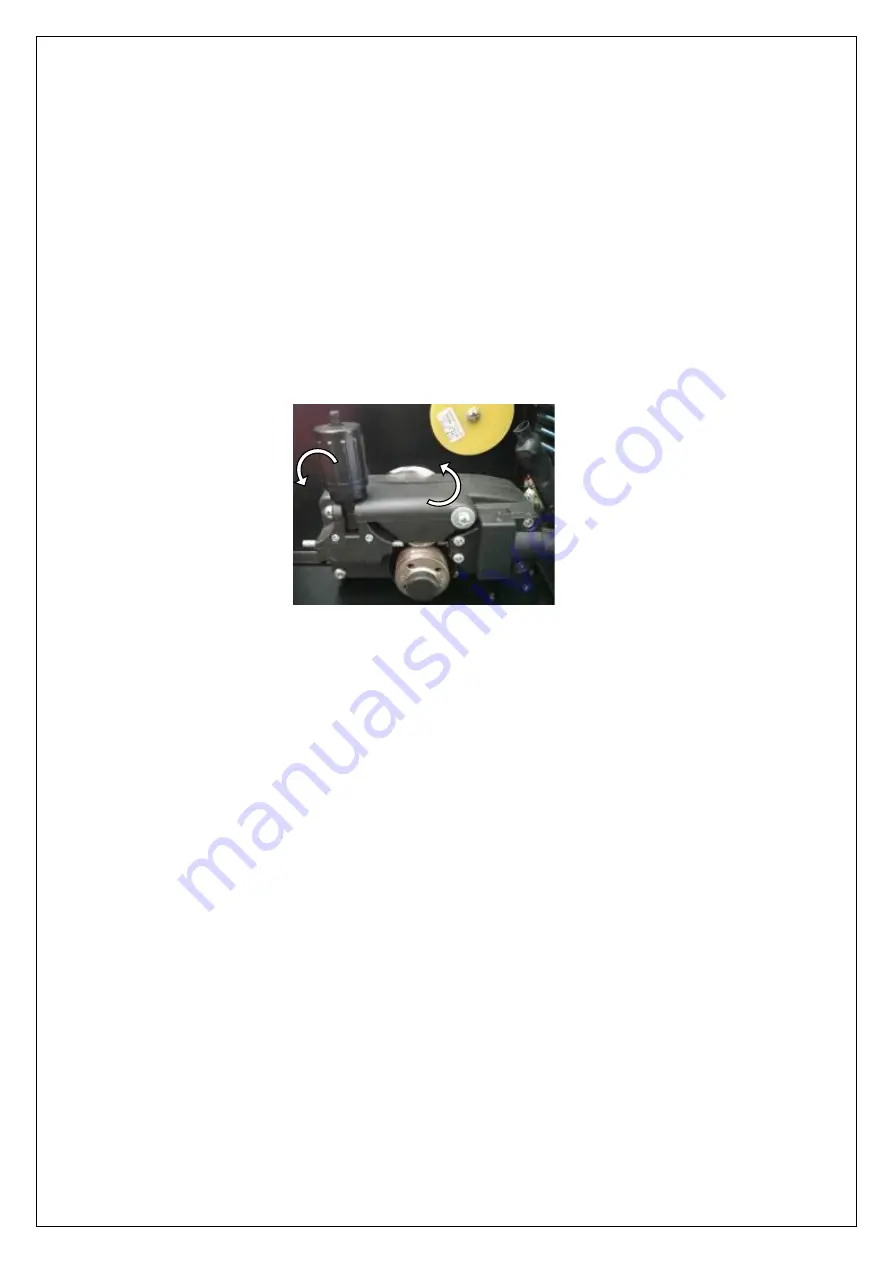
9
5.INSTALLTION
5.1. MIG Welding Set Up & Operation
5.1.1 Fitting the spool
5.1.1.1 open the cover door for the wire feed compartment. Remove the wire spool retainer(14) by threading off counter-
clockwise.
5.1.1.2 fit either a 4in or 8in diameter wire spool to the spool holder, ensuring the end of the wires exits towards the wire
feeder from the bottom of the spool. Refit the wire spool retainer(14) and finger tighten.
5.1.1.3 set the spool brake tension by rotating the adjustment screw(14) using an Allen wrench. Clockwise to increase brake
tension, counter-clockwise to decrease brake tension. The spool brake tension should be set so that the spool can rotate
freely, but does not continue to rotate once the wire feed stops. This may need to be adjusted as the wire is used up and
the spool weight decreases.
5.1.2 Loading wire feeder
5.1.2.1 release the wire feeder tension arm (shown below) by pivoting the wire feed tension adjuster(13) as pictured below
5.1.2.2 check the wire drive roller (12) groove matches the selected MIG wire type and size. The drive roller will have two
different sized grooves, the size of the groove in use is stamped on the side of the drive roller. For flux cored ‘soft’
wire ,such as that used in gasless MIG welding, the drive roller groove in knurled
. For solid ‘hard’ MIG wire, the roller
groove
has a ‘v’ shaped profile
.
5.1.2.3 the drive roller(12) is removed by threading the drive roller retainer off in the counter-clockwise direction. Once
the correct drive roller profile is selected, re-fit the drive roller.
5.1.2.4 thread the MIG wire from the spool through the input guide tube, through the roller groove and into the outlet
guide tube
5.1.2.5 Replace the tension arm and the tension adjustment. Double check the wire has located correctly in th
e drive
roller groove.
5.1.2.6 Adjusting wire feed tension: this is accomplished by winding the knob on the wire tension adjustment arm.
Clockwise will increase tension, counter-clockwise will decrease tension. There is a numbered scale on the tensioner to
indicate the position. Ideal tension should be as little as possible, while maintaining a consistent wire feed with no drive
roll slippage. Check all other possible causes of slippage, such as; incorrect/ worn drive roller, worn/ damaged torch
consumables, blocked/ damaged torch feed liner, before increasing feed tension.
Warning! - Before changing the feed roller or wire spool, ensure that the mains power is switched off
Warning! - The use of excessive feed tension will cause rapid and premature wear of the drive roller, the
support bearing and the drive motor.