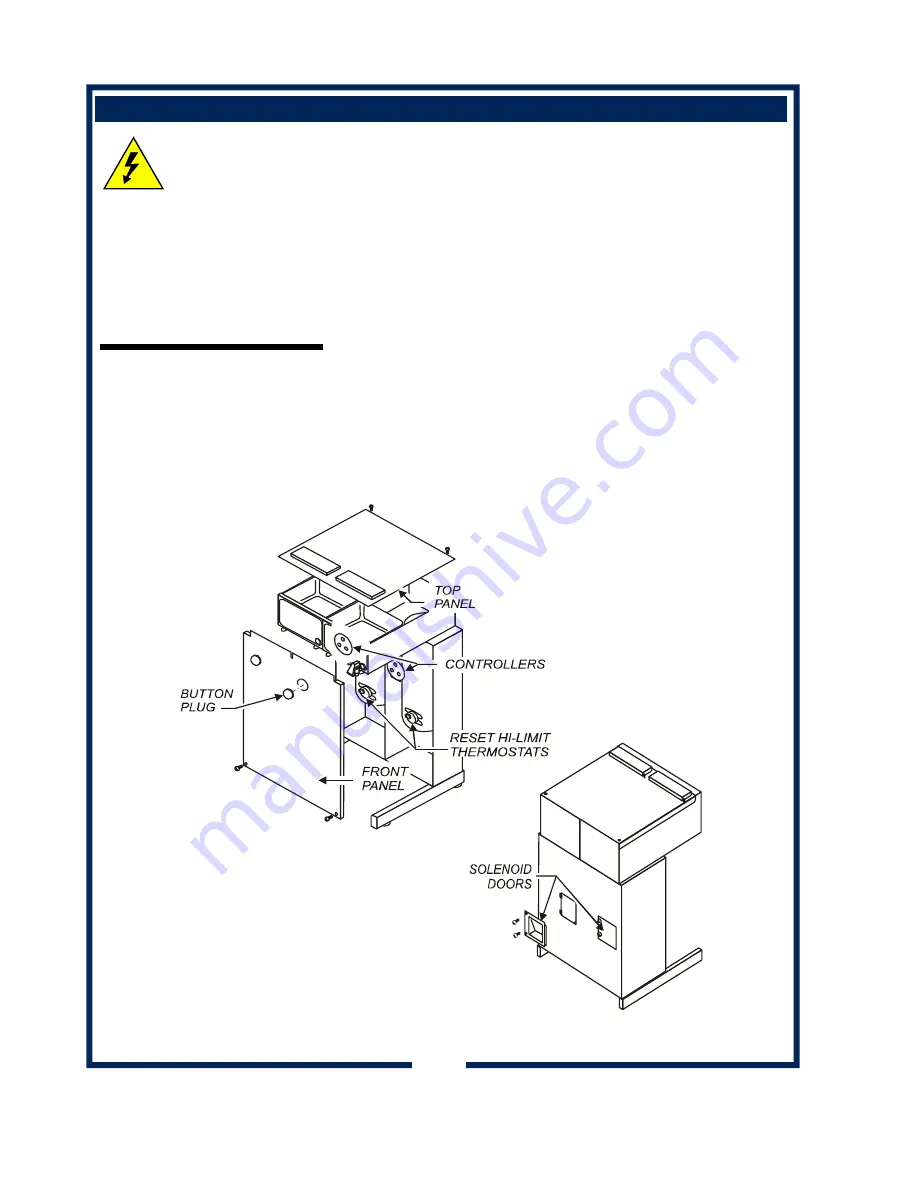
SERVICING INSTRUCTIONS
CAUTION:
SHOCK HAZARD
Opening access panels or
removing warmer plates on this
brew may expose uninsulated
electrical components.
Disconnect brewer from
electrical power before
removing any panel or warmer
plate.
ACCESS PANELS
TOP PANEL:
Remove top panel to access hot water tank, thermo probe,
heating elements, brew circuit tubing, faucet valve and piping.
Top panel is held by two screws at the rear and a retaining lip at
the front.
FRONT PANEL:
Remove front panel to access controller, terminal block and
solenoid.
Front panel is held by two screws at the bottom and a retaining
lip at the top.
SOLENOID DOOR:
Remove solenoid door to access solenoid plumbing connections.
Solenoid door is held by two screws and a retaining lip.
Fig. 12 Access Panels
14
645
75908
Owner
s M
anual E.B.C. Du
al Airpo
t/Thermal
B
rewer