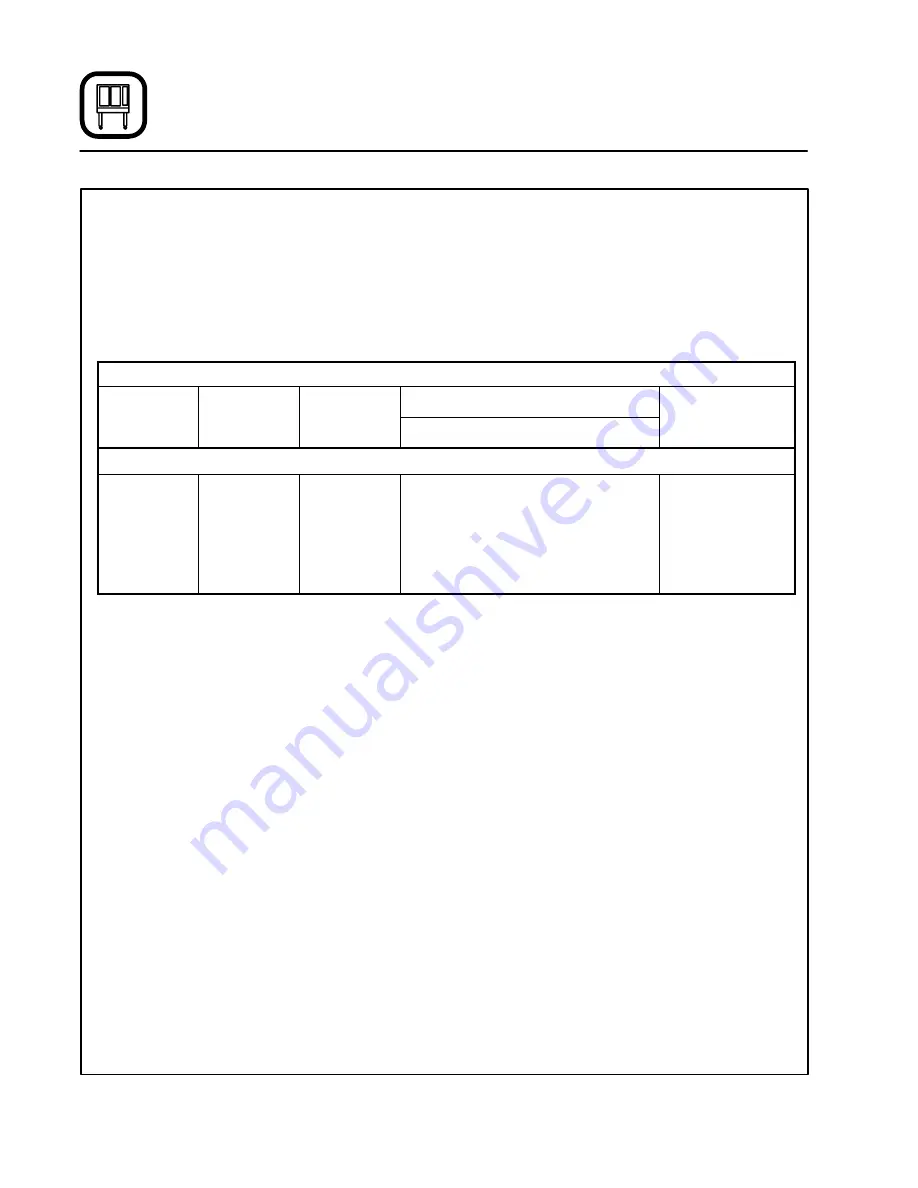
Introduction
2
Oven Description and Specifications
Cooking in a convection oven differs from cooking
in a conventional deck or range oven since heated
air is constantly recirculated over the product by
a fan in an enclosed chamber. The moving air conĆ
tinually strips away the layer of cool air surroundĆ
ing the product, quickly allowing the heat to peneĆ
trate. The result is a high quality product, cooked
at a lower temperature in a shorter amount of time.
Blodgett convection ovens represent the latest adĆ
vancement in energy efficiency, reliability, and
ease of operation. Heat normally lost, is recircuĆ
lated within the cooking chamber before being
vented from the oven: resulting in substantial reĆ
ductions in energy consumption and enhanced
oven performance.
ELECTRICAL SPECIFICATIONS: XCEL50EC
Amperes
Electrical
Connection
KW/Section
Volts
Phase
L1
L2
L3
N
Connection
AWG*
60 HZ UNITS
13.0
208
3
38
38
34
-
8
13.0
240
3
34
34
30
-
8
13.0
208
1
63
63
-
-
2
13.0
240
1
55
55
-
-
2
NOTE: *Electric connection wiring is sized for 90
_
C copper wire at 125% of rated input. Refer to Page 4
in this manual for Electrical Connection specifications.
NOTE: Double units can have phase loads partially equalized by matching lines during hookĆup. Otherwise
double unit load ratings are twice the above data.