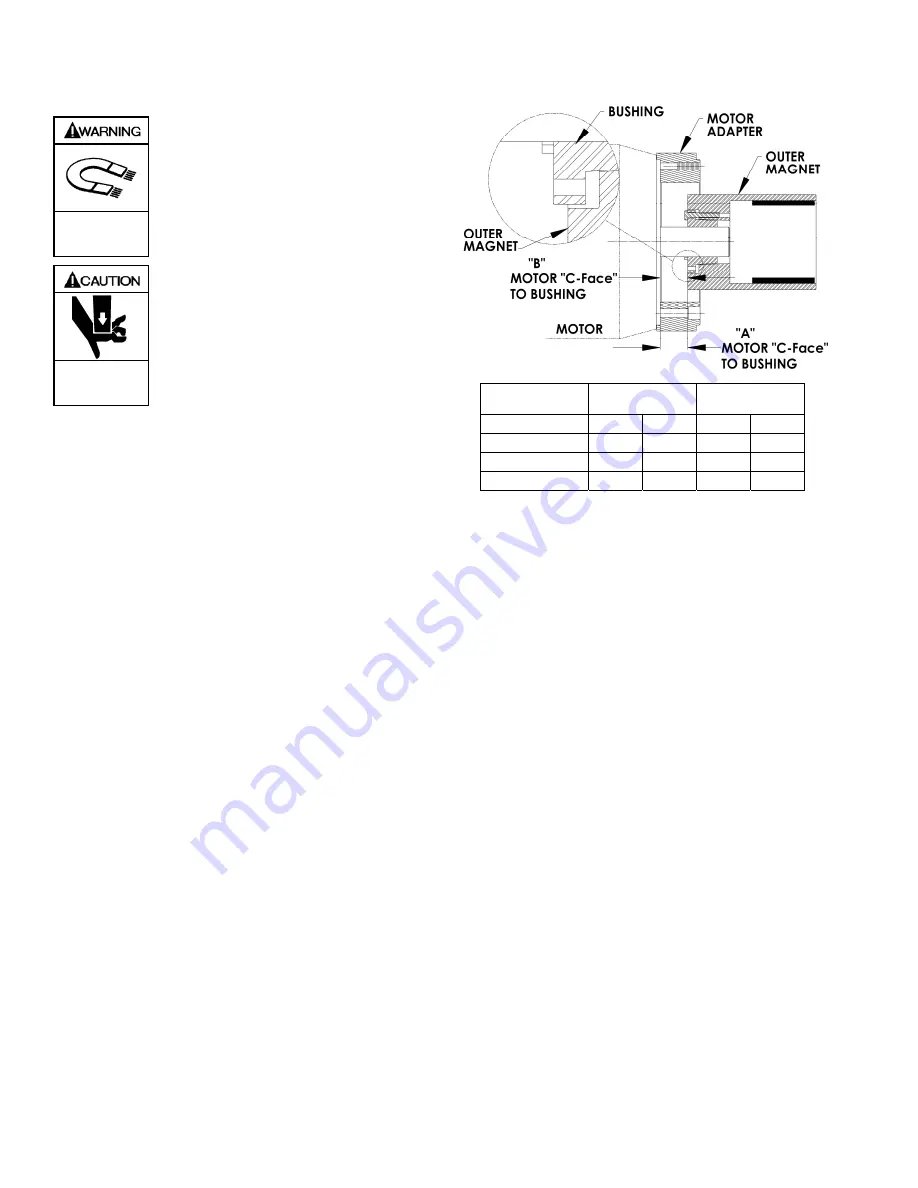
108-A00: Page 4/12
INSTALLATION
MOTOR INSTALLATION
Strong magnetic field can cause
personal injury or death to individuals
with medical implants or other magnetic
field sensitive medical conditions
Strong
Magnetic
field
Failure to use care when handling
magnets can cause personal injury
Strong magnetic
field can cause
personal injury
NOTICE:
Clear work area of all tools and materials affected by
magnets. Non-magnetic work surface recommended.
MAGNET SET
1. Put drive key in keyway on motor shaft.
2. Loosely assemble bushing with bolts & outer magnet.
Slide magnet assembly onto motor shaft.
3. Position bushing and magnet to Reference Dim “B”,
(see Table 1) and tighten setscrew over drive key.
4. Tighten the 3 bolts in a uniform sequence, torque to 9 ft
lbs. (12.2Nm)
5. When bolts are tightened, take a measurement for Dim
“A”. (see table 1)
Table 1
Dim “A”
Magnet Set
Dim “B”
Bushing Set
Motor Frame
INCH MM INCH MM
143TC / 145TC
0.464
11.8
0.454
11.5
182TC / 184TC
1.274
32.4
1.264
32.1
213TC / 215TC
1.374
34.9
1.364
34.6
6. If Measurement “A” does not match the value in the Table,
the bushing
MUST
be repositioned with a new Dim “B”.
Loosen the bolts and setscrew.
If Measurement “A” is
High:
Move the bushing towards the motor “C-Face”
New Dim “B” = table Dim “B” less the difference
between Measurement “A” and table Dim “A”.
If Measurement “A” is
Low
:
Move the bushing away from the motor “C-Face”
New Dim “B” = table Dim “B” plus the difference
between Measurement “A” and table Dim “A”
7. Retighten setscrew over drive key. Repeat Steps 4 – 6
8.
When Dim “A” is set correctly.
Ensure that Shaft &
Outer Magnet assembly rotate freely without binding
9. Slide the motor adapter ring (86) over the outer magnet to
the “C-Face” of the motor. Ensure that the flange of the
motor adapter ring is fully and squarely seated. Install the
adapter ring capscrews (56) torquing to 40 lbs ft (54 Nm)
NOTICE:
Be prepared for strong magnet attraction between the
inner and outer magnets, forcibly pulling the motor
coupling adapter assembly inward.
10. Ensure that the magnet housing (57) is bolted to the base.
11. Using an appropriately sized hoist, CAREFULLY insert the
outer magnet and motor into the mounted magnet housing
(57).
12. With the magnet housing fully and squarely seated, install
the four housing capscrews (54B); torque to 40 lbs ft (54
Nm).
Figure 3