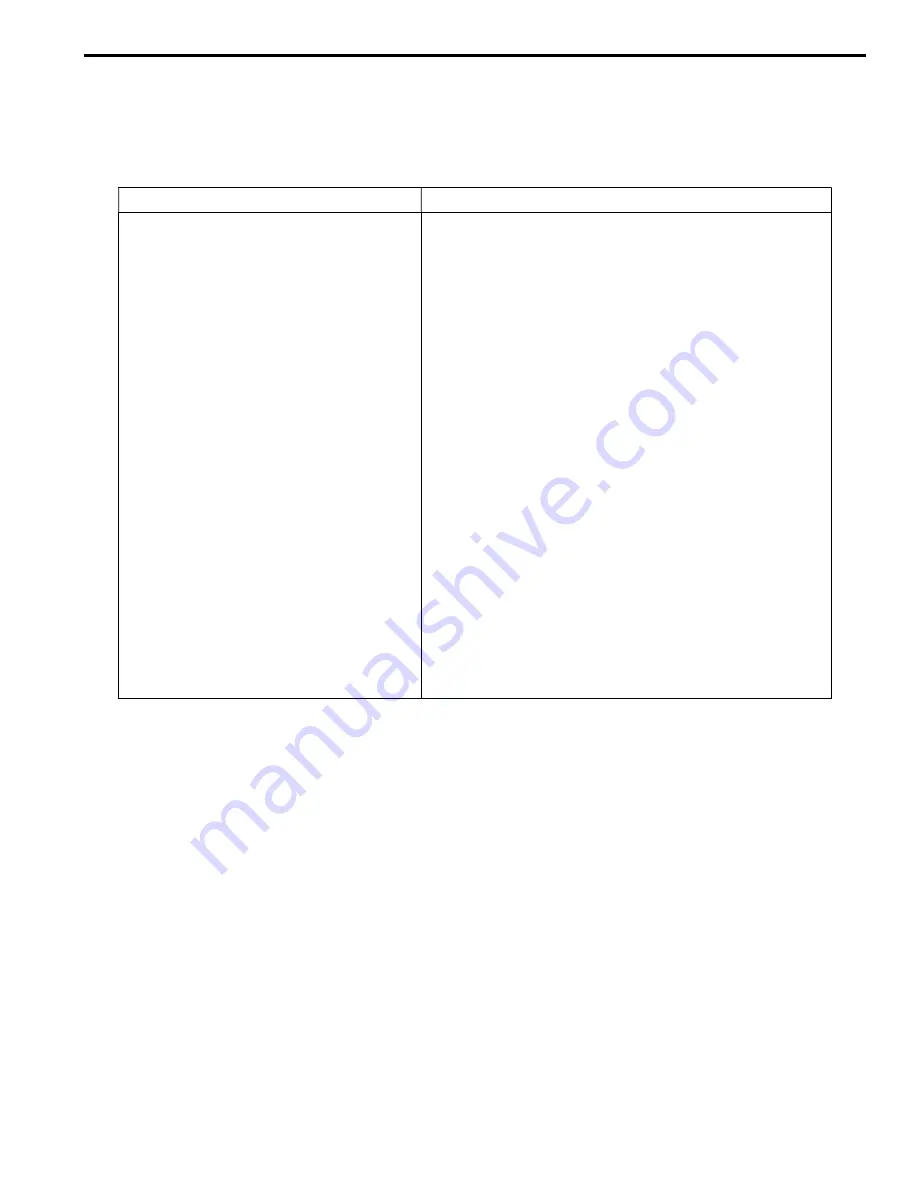
110-A01: Page 13/14
TROUBLESHOOTING
NOTICE:
Maintenance shall be performed by qualified technicians only,
following the appropriate procedures and warnings as presented in this manual.
PROBLEM
CAUSE
Pump Not Priming
See causes 1 through 7
Reduced Capacity
See causes 1 , 2, 3, 6 through 10
Noisy
See causes 1, 6, 7, 8, 9, 11 through 14
Damaged Vanes
See causes 8, 11, 16 through 21
Broken Shaft
See causes 7, 11, 13, 16, 17&20
Motor Overload
See causes 9, 13, 17, 22 & 23
1. Suction/discharge valve incorrectly set.
2. Leaks in suction piping.
3. Incorrect rotation.
4. Broken shaft.
5. Pump vapor locked.
6. Incorrect pump speed.
7. Vanes damaged, worn or incorrectly installed.
8. Cavitation.
9. Damaged or worn pump or system components.
10. Excessive piping/system friction losses.
11. Relief valve incorrectly set, worn or damaged.
12. Operating against a closed discharge.
13. Shaft bent or misaligned.
14. Worn or damaged bearings.
15. Piping inadequately anchored.
16. Foreign objects entering the pump.
17. Viscosity too high
18. Excessive heat.
19. Worn or damaged push rods.
20. Hydraulic hammer - pressure spikes.
21. Incompatible fluid(s).
22. Inadequate horsepower.
23. Incorrect voltage, wiring, phase loss.