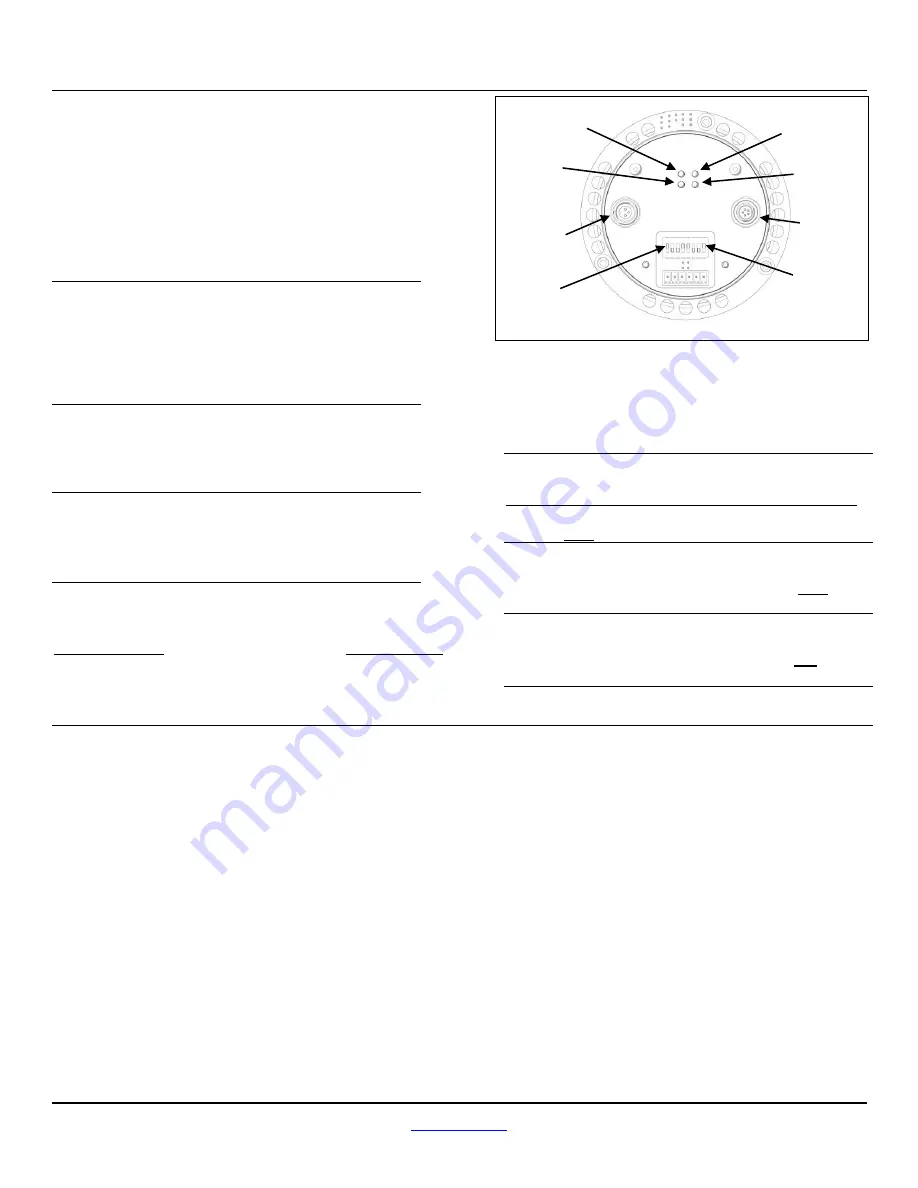
This document is subject to change without prior notification.
Warranty
Binsfeld Engineering Inc. warrants that its RT406 Series Transmitters will be free from defective materials and workmanship f or a period of two years
from the date of delivery to the original purchaser and that its products will conform to specifications and standards published b y Binsfeld Engineering
Inc. Upon evaluation by Binsfeld Engineering Inc., any product found to be defective will be replaced or repaired at the sole discretion of Binsfeld
Engineering Inc. Our warranty is limited to the foregoing. Binsfeld Engineering Inc. disclaims any warranty of merchantability or fitness for intended
purpose.
Binsfeld Engineering Inc. | 231-334-4383
852400-9_J.doc
RT406-2C Rotary Temperature Transmitter (852-400)
Troubleshooting
Four green LEDs are used to indicate the operational status
of the RT406 system. If all LEDs are on solid, the system is
operating properly. If there are any flashing, flickering or
LEDs off, there is a problem or error in operation.
Stator LED
On solid:
The Stator is functioning properly.
Flash:
Power supply error, power supply out of range.
Off:
No/Low power or fatal stator circuit error.
Rotor LED
On solid:
Data is being received from the Rotor
and all RTDs are in range.
Flash slow:
Intermittent data from the Rotor.
Flash fast:
One or more of the RTDs measured out
of range (possibly open or shorted).
Off:
No data from the Rotor.
CAN 1 LED
On solid:
Messages are being properly sent and
received on CAN bus 1.
Flash/flicker: Intermittent errors on CAN bus 1.
Off:
No communication on CAN bus 1.
CAN 2 LED
On solid:
Messages are being properly sent and
received on CAN bus 2.
Flash/flicker: Intermittent errors on CAN bus 2.
Off:
No communication on CAN bus 2.
Fault Condition Display Codes
When a fault condition exists the following temperature
will be displayed:
Fault Condition
Display Value
System Resetting
252
RTD sensor out of range low (including short)
253
DIP Switch
The 8 position DIP switch is used to set the node
address on CAN bus 1. It also is used to select
termination resistors on CAN bus 1 and 2 if needed.
(The DIP switch is located under the Switch cover.)
Switches 1
– 5
These 5 switches set the CAN bus 1 node address.
Set them the same as the unit that is being replaced.
Switch 6
Must be
OFF
for normal operation.
Switch 7
When on, this switch connects a 120 Ω termination
resistor across the CAN bus 1 lines. Leave
OFF
for
normal operation.
Switch 8
When on, this switch connects a 120 Ω termination
resistor across the CAN bus 2 lines. Leave
ON
for
normal operation.
RTD sensor out of range high (including open) 254
Rotor data error
255
Specifications
Rotor:
Number of sensors:
6
Sensor connection:
M3 set screw terminals with 2.38mm hole for ferrule access
Input sensor type:
PT1000 RTD (1000 ohm at 0°C, alpha = .00385)
Sensor range:
0
– 300°C
Speed:
10,000 RPM
Stator:
I/O Connectors:
CAN 1: 3-socket (Tyco Electronics PN: 6-1437719-6)
CAN 2: 5-pin (Tyco Electronics PN: 6-1437719-5)
I/O signals:
CAN bus 1: 125k baud for communication with operator interface
CAN bus 2: 100k baud for communication with heater power controller
Power Input:
17
– 30 VDC, 500mA (max)
General:
Accuracy (max error)
±0.5°C (max over ambient operating temperature range for 0-300°C RTD range)
Operating Temperature
0
– 85°C
Status Indicators
CAN bus 2
Connector
CAN bus 1
Connector
Stator
Indicator
CAN 1
Indicator
Rotor
Indicator
DIP
Switch
#1
CAN 2
Indicator
DIP
Switch
#8