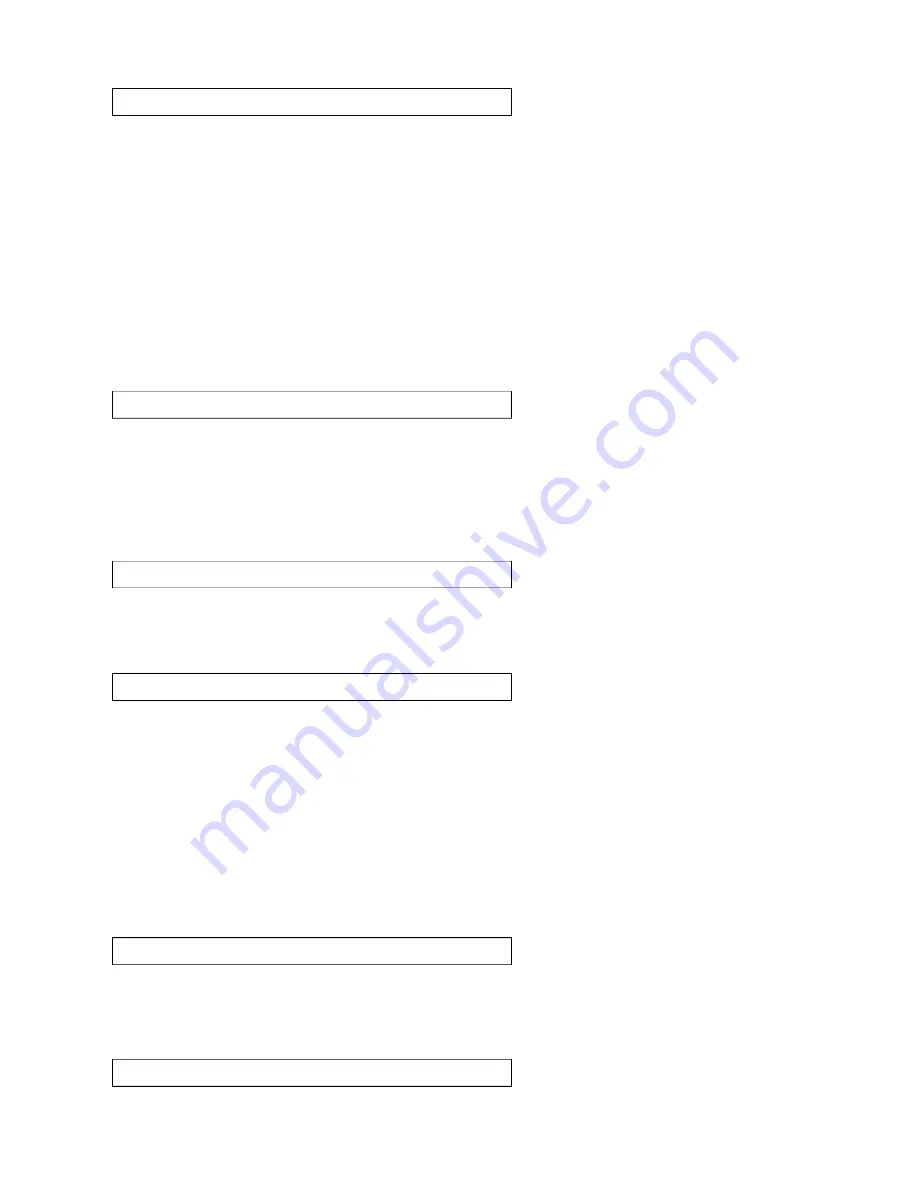
4
©BINKS 1999 – SB-E-A1-2
SAFETY WARNINGS
Solvents and coating materials can be highly flammable or combustible, especially when sprayed.
•
Work stations must be provided with adequate ventilation/exhaust to prevent the build-up of flammable vapours.
•
Smoking and naked flames must not be allowed in the spraying or mixing areas.
•
Fire extinguishing equipment must be provided in the spraying and mixing areas.
Users must comply with all local and national codes of practice and insurance company requirements governing ventilation, fire
precautions, operation, maintenance and housekeeping of work stations.
HALOGENATED HYDROCARBON SOLVENTS - for example 1,1,1-Trichloroethane and Methylene Chloride can chemically
react with aluminium and galvanised or zinc coated parts and cause an explosion hazard. Read the label and data sheet of the
material you intend to spray.
DO NOT USE SOLVENTS OR COATING MATERIALS CONTAINING HALOGENATED HYDROCARBONS WITH THIS
EQUIPMENT.
STATIC ELECTRICITY - is generated by fluid moving through pipes and hoses. A static spark, capable of igniting certain
solvents and coating materials, could be produced by high fluid flow rates. To prevent the risk of fire or explosion, earth
continuity to the spray equipment and object being sprayed should be maintained.
TOXIC VAPOURS - when sprayed, certain materials may be poisonous, create irritation or otherwise be harmful to health.
Always read carefully all labels and safety/performance data for the material being sprayed and follow any recommendations.
IF IN DOUBT, CONSULT THE MATERIAL SUPPLIER.
•
The use of respiratory protective equipment is recommended at all times when spraying. The type of respiratory protective
equipment used must be compatible with the material being sprayed and the level of concentration.
•
Always wear eye protection when spraying or cleaning the equipment.
•
Gloves must be worn for spraying or cleaning the equipment when certain coating materials and solvents are used.
Personnel should be given adequate training in the safe use and maintenance of this equipment. Training courses on all
aspects of the equipment are available. For details contact your local representative. The instructions and safety precautions
contained in this literature and the literature supplied with the coating material should be read and understood before the
equipment is used.
•
All spray guns project particles at high velocity and must never be aimed at any part of the body.
•
Never exceed the recommended safe working pressures for any of the equipment used.
•
The fitting of non-recommended or non-original accessories or spare parts may create hazardous conditions.
•
Before dismantling the equipment for cleaning or maintenance, all pressures, air and material, must be isolated and
released.
The disposal of non-metallic materials must be carried out in an approved manner. Burning may generate toxic fumes. The
removal of waste solvents and coating materials should be carried out by an authorised local waste disposal service.
The materials used in the construction of this equipment are (bearing in mind the warning on Halogenated Hydrocarbons)
solvent resistant enabling the equipment to be cleaned using gun washing machines. However, this equipment must not be left
inside the gun washing machine for prolonged periods of time after the automatic cleaning cycle has been completed. The
solvents used in the gun washing machine should be regularly checked to ensure that the equipment is not flushed through with
contaminated material. Follow the recommendations of the machine manufacturer.
The continuous A-weighted sound pressure level of this spray gun may exceed 85 dB(A) depending on the air cap/nozzle set-
up being used. Sound levels are measured using an impulse sound level meter and analyser, when the gun is being used in a
normal spraying application. Details of actual noise levels produced by the various air cap/nozzle set-ups are available on
request.
Spray equipment using high operating pressures may be subject to recoil forces, under certain circumstances such forces could
result in repetitive strain injury to the operator
OPERATING
NOISE LEVELS
MISUSE
TRAINING
PERSONAL PROTECTIVE EQUIPMENT
FIRE AND EXPLOSION