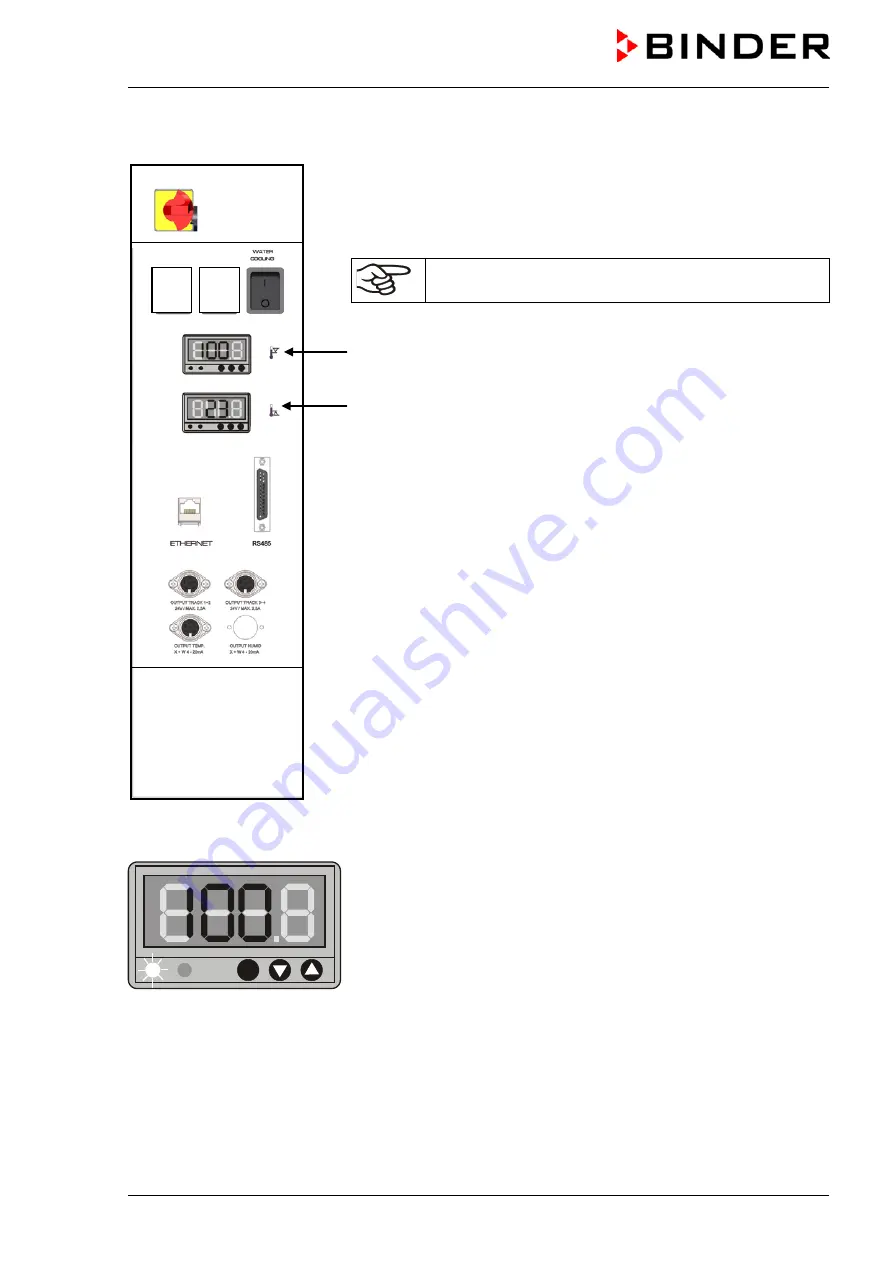
MK / MKT (E5) 03/2019
page 73/158
12.3 Over/under temperature safety device class 2 (option)
Example: MK 56
The over-/under temperature safety device (4) consists of two entry
modules (4a) and (4b) located in the lateral control panel. Both mod-
ules can be set from -50 °C /
-58°F
(MK) or -80 °C /
-112 °F
(MKT) up
to 200 °C /
392°F
and serve to define the maximum high and low tem-
perature limits.
With this option, the safety controller (chap. 12.2) must be
set to maximum temperature.
(4a) Upper module: Entry of the higher limit temperature.
(4b) Lower module: Entry of the lower limit temperature.
When the temperature inside the chamber leaves this tolerance
bandwidth, the temperature control, and herewith the heating and re-
frigeration, are turned off permanently.
At the corresponding entry module, the red pilot lamp K1 lights up (K2
is without function).
The controller displays the alarm message “Temp. safety device”
(chap. 11.1.2). Additionally there is an audible alert, provided that the
buzzer has not been deactivated (chap. 11.4).
Let the chamber heat up or cool down to the defined safety tempera-
ture range.
Then reset the alarm message on the controller (see chap. 11.3) to re-
activate the chamber. The red pilot lamp K1 goes off.
P
K2
K1
Setting limit temperatures at modules (4a) and (4b):
•
Press down button P
•
The display changes to entry mode
•
Enter the desired limit temperature via the arrow keys
•
The entered temperature value is adopted after a few seconds.
The display shows the actual temperature again.
Function check:
Check the over/under temperature safety device class 2 at appropriate intervals for its functionality. It is
recommended that the authorized operating personnel should perform such a check, e.g., before starting
a longer work procedure.
Summary of Contents for MK 115
Page 138: ...MK MKT E5 03 2019 page 138 158 24 12 Dimensions MK 56 dimensions mm ...
Page 139: ...MK MKT E5 03 2019 page 139 158 MK MKT 115 dimensions mm ...
Page 140: ...MK MKT E5 03 2019 page 140 158 MK 240 dimensions mm ...
Page 141: ...MK MKT E5 03 2019 page 141 158 MKT 240 dimensions mm ...
Page 142: ...MK MKT E5 03 2019 page 142 158 MK MKT 720 dimensions mm ...
Page 144: ...MK MKT E5 03 2019 page 144 158 ...
Page 145: ...MK MKT E5 03 2019 page 145 158 ...
Page 146: ...MK MKT E5 03 2019 page 146 158 25 2 EU Declaration of Conformity for MKT ...
Page 147: ...MK MKT E5 03 2019 page 147 158 ...
Page 148: ...MK MKT E5 03 2019 page 148 158 ...
Page 150: ...MK MKT E5 03 2019 page 150 158 ...
Page 151: ...MK MKT E5 03 2019 page 151 158 26 Product registration 26 1 Registering a BINDER chamber ...
Page 159: ......