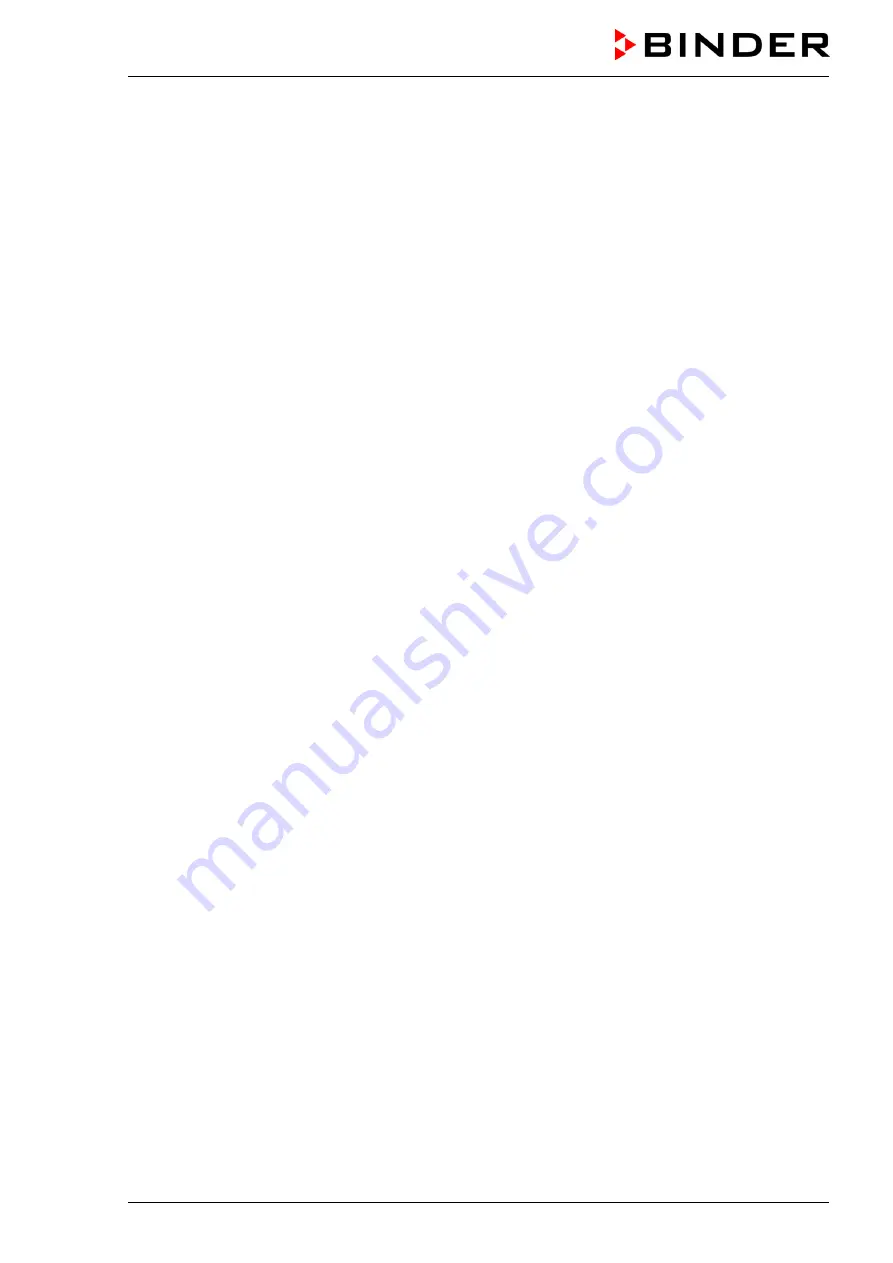
MK (E3) 07/2009
page 12/70
2.
Unit description
The temperature test chamber for natural simulation MK is a specially developed precision refrigerating /
warming cabinet with an unrivalled capacity, which by far exceeds the capabilities of normal test cabinets.
With its extensive program control, the temperature test chamber for natural simulation MK is designed
for optimum performance with regard to temperature accuracy and rapid heating up and cooling down
phases, thus providing the ideal facilities for solving all the problems which occur during material as well
as ageing and stress tests. In addition, the temperature test chamber for natural simulation provides al-
most unlimited possibilities for adaptation to individual customer requirements based upon extensive
programming options.
The patented APT.line™ preheating chamber and air conduction technology guarantees excellent spatial
temperature values for the total working area. The temperature test chamber MK provides a powerful
refrigerating system with rapid cooling-down speeds. In addition, the climatic test chamber MK provides
almost unlimited possibilities for adaptation to individual customer requirements based upon extensive
programming options.
The high-quality housing insulation guarantees both a low noise mode of operation and a consistently low
housing temperature. The inner chamber, the pre-heating chamber and the inside of the doors are all
made of stainless steel (material no. 1.4301 in Germany). When operating the chamber at temperatures
above 150°C /
302°F,
influence of the oxygen in the air might cause coloration of the metallic surfaces
(yellowish-brown or blue) by natural oxidation processes. These colorations are harmless and will in no
way impair the function or quality of the unit. The housing is RAL 7035powder-coated. All corners and
edges are completely coated.
The efficient program controller is regularly equipped with a multitude of operating functions, additional
recorder and alarm functions. Programming of test cycles is easily done via the modern color-display
controller MB1 and is also possible directly from the computer via Intranet in connection with the commu-
nication software APT-COM™ 3 DataControlSystem (option, chap. 14.1). The temperature test chamber
MK is regularly equipped with an Ethernet serial interface for computer communication. In addition, the
BINDER communication software APT-COM (option) permits networking up to 30 units and connecting
them to a PC for controlling and programming, as well as recording and representing temperature data.
For further options, see chap. 18.5.
The chambers
are equipped with
four castors.
Both
front
castors
can be
locked by brakes.
The temperature test chamber can be operated in a temperature range from -40°C /
104°F
up to +180ºC /
356°F
.
Summary of Contents for 9020-0146
Page 65: ...MK E3 07 2009 page 65 70 18 9 Dimensions MK 115 ...
Page 71: ......